Catalog excerpts
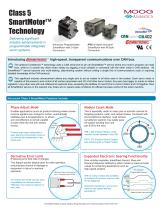
Class 5 SmartMotor™ Technology Delivering significant industry advancements in programmable integrated servo systems Introducing Advanced Programmable SmartMotor with D-Style Connectors IP65 & Higher Industrial SmartMotor with M-Style Connectors high-speed, transparent communications over CAN bus. The optional Combitronic™ technology uses a CAN serial port to join all SmartMotor™ servos where any motor’s program can read from, write to or control any other motor simply by tagging a local variable or command with the other motor’s CAN address. All SmartMotor™ servos become one multi-tasking, data-sharing system without writing a single line of communications code or requiring detailed knowledge of the CAN protocol. This significant industry advancement allows any single axis to act as master to all other axes in the system. Each servo motor is capable of full access to and control of all motion parameters and I/O of all other servo motors. Any axis may trigger on inputs or status registers in any other axis with sub-millisecond response time, exceeding the abilities of most PLCs to control motion and I/O together. Now all SmartMotor servos on the network may freely act on system-wide conditions for efficient process control of the entire machine. Advanced Class 5 SmartMotor Features Include: Phase Adjust Mode Modulo Count Mode Enables applications (such as product tracking) where moves must be applied over a target in motion, automatically stabilizes pan & tilt applications, or allows arm end effectors to remain parallel to base while the mid arm section Phase Encoder moves. This is especially useful in rotary pan or azimuth controls for targeting systems, radar, and camera bases. Combined with the Combitronic interface, multi camera surveillance systems may easily pass off subject tracking from one pan & tilt to the next. Phased origin stays referenced to base allowing commanded moves to be dynamically independent of the phase axis PML= 360 (Position Modulo Limit) maintain counts between 0 and 359 PMT= 270 (Position Modulo Target) take shortest path to Target Position Derivative Error Limit Expanded Electronic Gearing Functionality (Following error limit rate of change) This feature quickly detects jams for safer operation, ensuring less chance of damage to equipment or injury to machine operators. Derivative Error Limit used on Servo Controlled Spot Welder On contact with metal, the jaw stops immediately for minimal product deflection and maximum balance to each side Now includes separate, predefined Ascend, Slew and Descend distances defined by either master or slave encoder values for enhancing applications such as high-speed winders. Pre-defined Trapezoidal Gearing With an array of status bits available, all portions of the move may be used for I/O triggering Automatic transitions in and out are ideal for high speed labeling applications All Integrated Motor products made by Moog Animatics are covered by patent number 5,912,541 Slave Geared Velocity Slew Ratio Bit Trajectory Bit Descend Bit Master Encoder Input
Open the catalog to page 1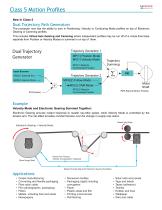
Class 5 Motion Profiles New in Class 5 Dual Trajectory Path Generators The processor now has the ability to sum in Positioning, Velocity or Contouring Mode profiles on top of Electronic Gearing or Camming profiles. This includes Virtual Axis Gearing and Camming where independent profiles may be run off of a virtual time base separate from Position or Velocity Modes or summed in on top of them. Dual Trajectory Generator Trajectory Generator 1 MP(1) Position Mode MV(1) Velocity Mode RPC(1) Reports Commanded Position Input Sources Trajectory Summing Motor Shaft MC(2) CAM Mode RPC(2) Reports...
Open the catalog to page 2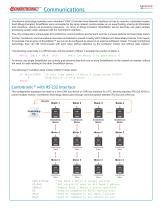
Combitronic technology operates over a standard “CAN” (Controller Area Network) interface but has no need for a dedicated master. Each Moog Animatics' SmartMotor servo connected to the same network communicates on an equal footing, sharing all information and, therefore, sharing all processing resources. An array of Moog Animatics' SmartMotor servos becomes one giant parallelprocessing system when equipped with the Combitronic interface. The only configuration prerequisites for Combitronic communications are that each axis has a unique address and baud rates match. Further, Combitronic...
Open the catalog to page 3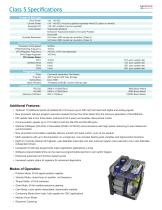
MOOG ’^^•AnimaticS Class 5 SpecificationsPower & Encoder Drive Power: +20 - 48 VDC Additional Features: • Optional: 10 additional points of isolated 24V I/O source (up to 300 mA) that read both digital and analog signals • New processor delivers program execution speeds that are five times faster than the previous generation of SmartMotors • PID update rate is four times faster (reduced to 62.5 psec) and enables ultra-precise motion • Communication speeds up to 115.2 kBd in both the RS-232 and RS-485 ports • Optional CANopen (CiA 402) or DeviceNet (Profile 16 ODVA) communications with...
Open the catalog to page 4
Class 5 Connector Pinouts M-Style SmartMotor D-Style SmartMotor I/O – 6 GP, Index Input or “G” Command +5 VDC Out RS-232 Transmit RS-232 Receive SIG Ground Main Power +20-48 VDC Ground Control Power In Chassis Control, Com, I/O and Amplifier Ground Amplifier Power In Control, Com, I/O and Amp Ground RS-485 B, Com ch. 0 RS-485 A, Com ch. 0 Encoder A+ Input/Output Encoder B- Input/Output Encoder A- Input/Output +5 V Out Encoder B+ Input/Output I/O – 0 GP or Encoder A or Step Input I/O – 1 GP or Encoder B or Direction Input I/O – 2 Positive Overtravel or GP P2 DB-15 D-Sub I/O – 3 Negative...
Open the catalog to page 5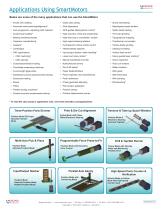
Applications Using SmartMotors Below are some of the many applications that can use the SmartMotor • Anode wire welding • Glass tube cutting • Shock load testing • Glue dispensers • Step/tapered spool winders • Auto-progression, adjusting parts indexers • GPS-guided steering/drive control* • Tactile switch testing • Audio/visual mobility* • High-accuracy, three-axis positioning* • Tire tread grinding • Bearing inserters/presses • High-axis-count, coordinated motion* • Topographical mapping • Capacitor manufacturing • High-speed indexing labelers • Transformer coil winders • Hydroelectric...
Open the catalog to page 6All Moog GmbH - Niederlassung Memmingen catalogs and technical brochures
-
product catalog
52 Pages
-
Power Supplies and Shunts
10 Pages
-
M6S
1 Pages
-
PSC
1 Pages
-
SL17406D
2 Pages
-
SM23216MH
5 Pages
-
SM23166MT
5 Pages
-
SM23305D
2 Pages
-
SM23165DT
2 Pages
-
SM23165MT-IP
2 Pages
-
SM23205D
2 Pages
-
SM23375D
2 Pages
-
SM23405D
2 Pages
-
SM23375DT
2 Pages
-
SM34165D
2 Pages
-
SM34205D
2 Pages
-
SM34165DT
2 Pages
-
SM34165MT-IP
2 Pages
-
SM34305D
2 Pages
-
SM34405D
2 Pages
-
SM34505D
2 Pages
-
Open Frame Shunts
1 Pages
-
Moog Animatics Catalog 2013
224 Pages
Archived catalogs
-
TTR Table Top Robot
1 Pages
-
SmartMotor™ User's Guide
144 Pages
-
SmartMotor™ User's Guide
126 Pages