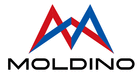
Group: HITACHI

Catalog excerpts
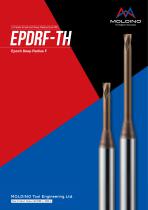
4 Flutes Small and Deep Radius End Mill AA MOLDINO The Edge To Innovation fpdrf-thEpoch Deep Radius FMOLDINOTool Engineering, Ltd. New Product News No. 1216E-5
Open the catalog to page 1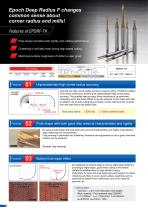
Epoch Deep Radius F changes common sense about corner radius end mills! Features of EPDRF-TH Flute shape provides both rigidity and cutting performance. Chattering is not likely even during high-speed cutting. Machined surface roughness of bottom is also good. Carbon steel Alloy steel Stainless steel Pre-hardened Tool steel steel Like ball end mills, corner radius accuracy is kept to within ±0.005mm relative to the tool's central axis, achieving an unprecedented high corner radius accuracy. This enables high-accuracy finish machining to be performed, something which has been difficult to do...
Open the catalog to page 2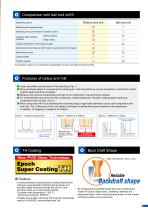
^Comparison based on the individual characteristics of radius end mills and ball end mills O Large step widths can be taken for flat machining. (Fig. 1) 2 Since peripheral speed is increased at the cutting point, machining efficiency can be increased on machines for which rotation speed cannot be increased. e Because chip removal characteristics are high at the cutting point, chip jamming is reduced. o For small-diameter long-neck end mills in particular, cutting resistance is reduced, enabling stable machining compared to ball end mills. (Fig. 2) 5 When using tools with R size matching the...
Open the catalog to page 3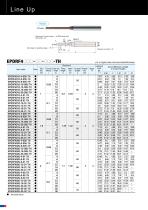
EPDRF4 TH 0 4 or higher does not have backdraft shape.
Open the catalog to page 4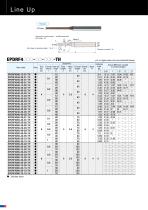
Line Up Radius 4 Flutes Tolerance on Corner radius r:±0.005 center axis) ( Helix Angle:20° Back taper on peripheral edge:1.5~6° φ 4 or higher does not have backdraft shape. Size(mm) ●:Stocked Items. Corner Under neck Flute radius length length R r R 2 0.1 Neck Overall Shank dia. length dia. D1 L Ds Interference Actual Effective Length angle in Incline Angles θ κ (° ) 0.5° 1° 1.5° 2°
Open the catalog to page 6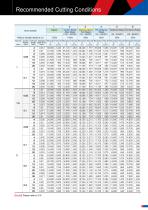
[Note] Please refer to P.9
Open the catalog to page 7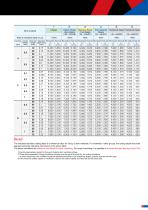
Work material The indicated standard cutting depth is a reference value for Group 2 work materials. For materials in other groups, the cutting depth should be adjusted using the reference ratio shown in the above table. The above conditions are reference conditions for finish machining. For rough machining, it is possible to increase the feed rate by around 30%. ®Use the appropriate coolant for the work material and machining shape. ©These Recommended Cutting Conditions indicate only the rule of a thumb for the cutting conditions. In actual machining, the condition should be adjusted...
Open the catalog to page 9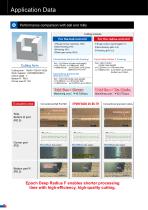
Application Data Performance comparison with ball end mills Cutting process R2 ①Rough contour machining(R 2) ②Semi-finishing (R1) ③Finishing (R1) ④Side-open cavity (R0.5) Conventional ball end mill (Finishing) Cutting form Cutting form:15(W)×15(H)×15(D) Work material:HPM38(52HRC) Incline angle : 1° Bottom R:R0.5 Corner area R:R2 Epoch Deep Radius F (Finishing) Tool:φ2×r 0.5×20 Tool:R1×20mm (Under neck length) (Under neck length) n =14,175min-1 (v c=89m/min) Wet v f=868mm/min a p=0.02mm a e=0.02mm n =12,500min-1(v c=79m/min) Wet (bottom) a e=0.1mm v f=1,008mm/min a p=0.02mm a...
Open the catalog to page 10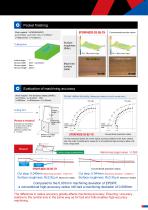
Conventional precision radius Surface roughness (Side) Cutting form Chattering created Fine surface Incline angle :1° Groove width :3mm(at bottom) Groove depth :5mm Groove length :20mm Machined surface (side) Evaluation of machining accuracy Work material:Pre-hardened steels (38HRC) a p=0.03mm a e=0.05mm Wet n=9600min-1 v f =900mm/min f z =0.03mm/t Cutting form Machining target value 0.05 Evaluation of machining accuracy when cutting in 0.050mm from a reference surface with a 1° incline Reference surface (Incline angle 1° ) Reference surface Corner radius accuracy (Measured relative to...
Open the catalog to page 11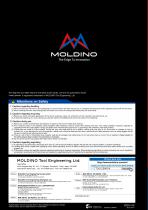
The diagrams and table data are examples of test results, and are not guaranteed values. “ ” is registered trademarks of MOLDINO Tool Engineering, Ltd. Attentions on Safety 1. Cautions regarding handling (1) When removing the tool from its case (packaging), be careful that the tool does not pop out or is dropped. Be particularly careful regarding contact with the tool flutes. (2) When handling tools with sharp cutting flutes, be careful not to touch the cutting flutes directly with your bare hands. 2. Cautions regarding mounting (1) Before use, check the outside appearance of the tool for...
Open the catalog to page 12All MOLDINO Tool Engineering Europe GmbH catalogs and technical brochures
-
CBN-EPSB/CBN-EPSR
16 Pages
-
EPBTS
12 Pages
-
EMXR
16 Pages
-
EMXA
12 Pages
-
EPDBPE-ATH
20 Pages
-
Epoch TH Power Mill
12 Pages
-
Radius Precision ARPF
20 Pages
-
Carbide Thread Mill series
16 Pages
-
SCE-R
6 Pages
-
RV type
12 Pages
-
ABPFN type
6 Pages
-
TD4N type
8 Pages
-
EHHB-ATH
8 Pages
-
EPCDS
4 Pages
-
Epoch CFRP series
6 Pages
-
EPSM-PN/ EPSW-PN
32 Pages
-
GALLEA series
24 Pages
-
WHMB-TH
12 Pages
-
EMBE-ATH/EMBPE-ATH
16 Pages
-
ETR(P)-TH,ETM(LN/P)-TH
16 Pages
-
EPDRE-ATH
24 Pages
-
CBN-EHB
12 Pages
-
EHHBE-TH3
8 Pages
-
TD6N type
12 Pages
-
EB4HR-ATH
12 Pages
-
EHX
12 Pages
-
EPHB-PN
8 Pages
-
EHHRE-TH3
8 Pages
-
EDT
16 Pages
-
EHSE-TH
8 Pages
-
NSB
12 Pages
-
WHNSB-TH
20 Pages
-
EMSBS
8 Pages
-
Ball Precision F ABPF type
16 Pages
-
Carbide Drill for SR machining
12 Pages
-
Radius Mill RD16B Type
8 Pages
-
GS4TN type
4 Pages
-
Red Screw Arbor
8 Pages
-
ABP4F
8 Pages
-
EPDBE-PN/ATH EPDSE-PN/ATH
32 Pages
-
EPDBEH-TH3
20 Pages
-
MINIATURE DRILL WHMB
8 Pages
-
Epoch ® Combination Rib Ball
8 Pages
-
PRODUCTS CATALOGUE 2015 - 2016
1070 Pages
-
Carbide Non Step Borer series
28 Pages
-
Drills for High-hardness Steels
16 Pages
-
Face Mill : ASF type
8 Pages
-
Face Mill : AFE45 type
8 Pages
-
Ball Precision F : ABPF type
16 Pages
-
Ball End Mill : ASB type
8 Pages
-
Radius Precision : ARPF type
12 Pages
-
Polish Mill V Type : ASPV Type
20 Pages
-
Roughing End Mill : AME Type
12 Pages
-
Radius Mill : AR type
20 Pages
-
JM4060
4 Pages
-
Epoch Micro?End Mill TH : EMM-TH
24 Pages
-
Epoch Deep Radius Evolution
24 Pages
-
Epoch Deep Ball Evolution Hard
16 Pages
-
Epoch Micro Drill?EMD
24 Pages
-
Radius Mill : ASR type
20 Pages
-
Super Excellent MINI : ASM type
12 Pages
-
Epoch "Mirus" Series
12 Pages
-
Epoch G Turbo
8 Pages
-
Roughing End Mill AME Type
12 Pages
-
Z Plunging Borer?ZPB-TH
4 Pages
-
Face Mill AFE45
8 Pages
-
Epoch Micro Step Borer S
8 Pages
-
Epoch CBN End Mill series
16 Pages
-
HX3505 & HX3515
6 Pages
-
GX2140
4 Pages
-
Epoch "Panacea"
16 Pages
-
Epoch Deep Evolution series
24 Pages
-
Epoch SUS End Mill series
32 Pages
-
Epoch Pencil Deep Ball Evolution
20 Pages
-
Epoch Deep Radius F
12 Pages
Archived catalogs
-
Carbide End Mills
280 Pages
-
HSS Non Step Borer
36 Pages
-
Surface Treatment Tribec
8 Pages
-
CBN End Mills
20 Pages
-
Re-grinding & Re-coating
20 Pages
-
Cutters
10 Pages
-
Reamers
16 Pages
-
HSS End Mills
98 Pages
-
Turning Inserts
44 Pages
-
Threading Tools
6 Pages
-
Indexable Tools
160 Pages
-
Milling Inserts
16 Pages
-
Micro Series for Micro Machining
14 Pages
-
2009-2010 New Products Guide
5 Pages