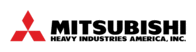
Catalog excerpts
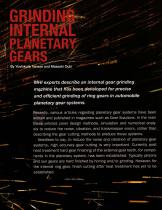
By Yoshikot© Yanase and Masashi Oqhi MHI experts describe an internal gear grinding mqphine that has beery developed for precise and efficient grinding of ring gears in automobile planetary gear systems. Recently, various articles regarding planetary gear systems have been written and published in magazines such as Gear Solutions. In the main these articles cover design methods, simulation and numerical analy- sis to reduce the noise, vibration, and transmission errors, rather than describing the gear cutting methods to produce these systems. Needless to say, to reduce the noise and vibration of planetary gear systems, high accuracy gear cutting is very important. Currently post heat treatment hard gear finishing of the external gear teeth, for compo- nents in the planetary system, has been established. Typically pinions and sun gears are hard finished by honing and/or grinding. However, for the internal ring gear, finish cutting after heat treatment has yet to be
Open the catalog to page 1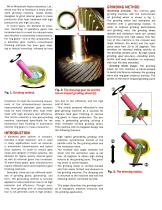
We at Mitsubishi Heavy Industries, Ltd., would now like to introduce a newly devel- oped grinding machine, model ZI20A, designed to grind internal gears in mass production after heat treatment with high productivity and high accuracy. In recent years, the demand for preci- sion machining of planetary gears has increased due to a need for reduced noise and vibration in automotive transmissions. For ring gears—one of the components of a planetary gear system—conventional finishing methods has been gear shap- ing or helical broaching, followed by heat treatment. To meet the increasing require-...
Open the catalog to page 2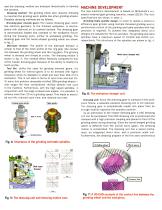
and the dressing method are analyzed theoretically to develop Dressing method: The grinding wheel also requires dressing to maintain the grinding worm profile like other grinding wheels. Possible dressing methods are as follows. Dressing gear (master gear): The master dressing gear, which has identical geometry to the finished workpiece, is electro- plated with diamond on its toothed surface. The dressing gear is automatically loaded and clamped to the workpiece fixture during the dressing cycle, similar to workpiece grinding. The dressing gear and the barrel-shaped grinding wheel are shown...
Open the catalog to page 3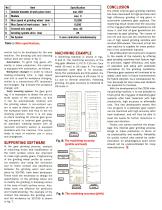
Fig. 9: The machining accuracy (pitch). The ZI20A internal gear grinding machine has been developed for high precision and high efficiency grinding of ring gears in automobile planetary gear systems. The machining result shows that the accuracy of the ring gear after heat treatment is JIS class 4, and that all gear geometries are improved by gear grinding. The issues of tool life and tool cost are resolved by the use of high speed grinding spindles and vitrified CBN wheels. The result is that the new machine is capable for mass produc- tion in the automobile industry. We at Mitsubishi will...
Open the catalog to page 4