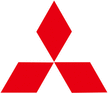
Catalog excerpts
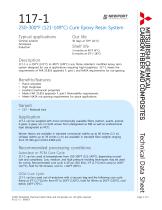
250-300°F (121-149°C) Cure Epoxy Resin System Typical applications General aviation Aerospace Industrial Out life 30 days at 70°F (21°C) Shelf life 3 months at 40°F (4°C) 6 months at 0°F (-18°C) Description 117-1 is a 250°F (121°C) to 300°F (149°C) cure, flame retardant, modified epoxy resin system designed for use in applications requiring high toughness. 117-1 meets the requirements of FAR 25.853 appendix F, part I, and NASA requirements for out-gassing. Benefits/features • Flame retardant • High toughness • Excellent mechanical properties • Meets FAR 25.853 appendix F, part I flammability requirements • Meets NASA out-gassing requirements for space applications Variant • 117 - Reduced tack Application 117-1 can be supplied with most commercially available fibers (carbon, quartz, aramid, S-glass, E-glass, etc.) in both woven form (designated as NB) as well as unidirectional tape (designated as NCT). Woven fabrics are available in standard commercial widths up to 60 inches (1.5 m). Unitape widths up to 39 inches (1 m) are available in standard fiber weights ranging from 70-300 gsm (0.014-0.060 psf). Recommended processing conditions Autoclave or PCM Cure Cycle 117-1 can be cured at temperatures from 250-300°F (121-149°C), depending on part size and complexity. Low, medium, and high pressure molding techniques may be used for curing. Recommended cure cycle is 45 psi (310 kPa), 3°F (1.7°C)/min ramp to 260°F (127°C), hold for 90 minutes, cool to <140°F (60°C). OOA Cure Cycle 117-1 can be cured out-of-autoclave with a vacuum bag and the following cure cycle. Ramp at 3°F (1.7°C)/min from RT to 265°F (130°C), hold for 90min at 265°F (130°C), cool below 140°F (70°C). ©2017 Mitsubishi Chemical Carbon Fiber and Composites, Inc. All rights reserved PL-117-1 - 060917
Open the catalog to page 1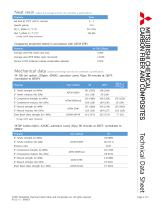
[values are average and do not constitute a specification] Value Gel time @ 275°F (135°C), minutes 5 - 7 Outgassing properties tested in accordance with ASTM E595 Property 34-700 150gsm Average value TML (Total mass loss) 0.36% Average value WVR (Water vapor recovered) < 0.01% Percent CVCM (Collected volatile condensable materials) 0.07% Mechanical data [values are average and do not constitute a specification] 34-700 Uni carbon, 150gsm, 40%RC, autoclave cured, 45psi, 90 minutes at 260°F, normalized to 60%FV Property Test method RT 160°F 160°Fwe.* (71°CwJ 0° Tensile...
Open the catalog to page 2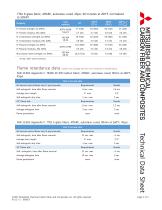
7781 E-glass fabric, 40%RC, autoclave cured, 45psi, 90 minutes at 260°F, normalized to 50%FV Test method 0° Tensile strength, ksi (MPa) 0° Tensile modulus, Msi (GPa) 0° Compressive strength, ksi (MPa) 0° Compressive modulus, Msi (GPa) 0° Flexural strength, ksi (MPa) 0° Flexural modulus, Msi (GPa) Short beam shear strength, ksi (MPa) Flame retardance data [values are average and do not constitute a specification] FAR 25.853 Appendix F, TR30S 3K PW Carbon fabric, 40%RC, autoclave cured, 90min at 260°F, 60-Second vertical flame test (7-ply laminate) Requirements Results...
Open the catalog to page 3
Vertical burn test Requirements Results Max longest burning particle 3 sec. max None 45° Burn test Requirements Results Penetration none none ©2017 Mitsubishi Chemical Carbon Fiber and Composites, Inc. All rights reserved PL-117-1 - 060917
Open the catalog to page 4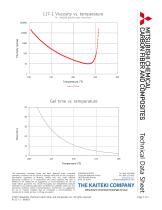
117-1 Viscosity vs. temperature TA - AR2000 parallel plate rheometer Viscosity (poise) The information contained herein has been obtained under controlled laboratory conditions and are typical or average values and do not constitute a specification, guarantee, or warranty. Results may vary under different processing conditions or in combination with other materials. The data is believed to be reliable but all suggestions or recommendations for use are made without guarantee. You should thoroughly and independently evaluate materials for your planned application and determine suitability...
Open the catalog to page 5