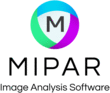

Catalog excerpts
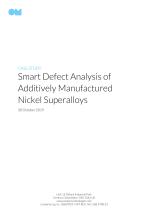
CASE STUDY: Smart Defect Analysis of Additively Manufactured Nickel Superalloys 30 October 2019 Unit 15 Oxford Industrial Park Yarnton, Oxfordshire, OX5 1QU, UK www.oxmet-technologies.com company reg. no. 10687859 | VAT REG. NO. 268 5780 53
Open the catalog to page 1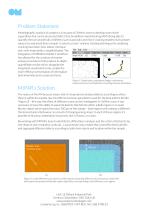
Problem Statement Metallographic analysis of samples is a key part of OxMet’s work to develop novel nickel superalloys that can be processed defect-free by additive manufacturing (AM). Being able to quantify the size and density of defects such as porosity and micro-cracking enables much greater value to be extracted than a simple “cracks/no cracks” analysis. Existing techniques for analysing cracking have been slow, labour-intensive and, most-importantly, unsophisticated. The integration of MIPAR to OxMet’s workflow has allowed for the creation of smarter analysis procedures that produce...
Open the catalog to page 2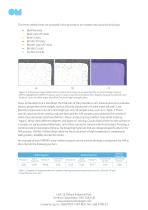
The seven defects that are analysed in this procedure are named and coloured as follows: • • • • • • • Bulk Porosity Bulk Lack of Fusion Bulk Cracks Border Porosity Border Lack of Fusion Border Cracks Surface Cracks Figure 3: a) Raw input image obtained from optical microscopy, b) an automatically-processed image showing defects highlighted in different colours, and c) cracks coloured according to their lengths, showing how Border and Surface Cracks are often longer than Bulk Cracks for high-strength alloys Once all the defects are identified, the final part of the procedure runs...
Open the catalog to page 3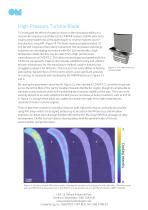
High-Pressure Turbine Blade To investigate the effect of material choice on the manufacturability of a real-world component and fully test the MIPAR analysis, OxMet selected a small turbine blade from a helicopter engine to reverse engineer and remanufacture using AM (Figure 4). The blade measured approximately 31 mm tall and is typical of the type of component that aerospace and energy industries are attempting to produce with AM. Conventionally, a hightemperature blade like this may be made from a high-performance superalloy such as CM247LC. This alloy was developed and optimised in the...
Open the catalog to page 4All MIPAR catalogs and technical brochures
-
Porosity Analysis
2 Pages
-
Cracks and Pores
2 Pages
-
Aerial Applications
2 Pages
-
Fibers Analysis
1 Pages
-
Fiber Cross Sections
2 Pages
-
Coarse Fibers
2 Pages
-
Satellite Particles
2 Pages
-
Powder Particles
2 Pages
-
Particle Sorting in Asphalt
1 Pages
-
Crystals
2 Pages
-
Cracks in Particles
2 Pages
-
Ti Alloy Microstructure
1 Pages
-
Gamma Prime Detection
1 Pages
-
Alpha Beta in Ti
1 Pages
-
Twin Grains Analysis
1 Pages
-
Grains Analysis
1 Pages
-
Largest Grain
1 Pages
-
Ceramics Grains 2
2 Pages
-
Ceramic Grains
1 Pages
-
Beta Grains in Ti
1 Pages
-
MIPAR API
2 Pages
-
Additive Manufacturing
1 Pages
-
Metals infographic
1 Pages
-
Ceramics infographic
1 Pages
-
Battery Flyer
1 Pages
-
Banner 2
1 Pages
-
Banner 1
1 Pages
-
AMP 2019 Article
7 Pages
-
MIPAR LIVE BROCHURE
4 Pages
-
MIPAR - QAQC Brochure
12 Pages
-
MIPAR Brochure
6 Pages
Archived catalogs
-
Nanoparticles
2 Pages
-
Deep Learning
1 Pages