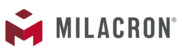
Group: MILACRON
Catalog excerpts
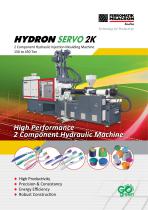
2 Component Hydraulic Injection Moulding Machine Design Advantages & Features CLAMP • • • • • • • • • • • • • • • Hollow Headless Ram with Mono Seal & No Piston Rings Large Prefill Designed for Fast Tonnage Build-up Rapid Traverse Cylinders Conical Strain Rod Nuts & Controlled Stress on Tie Rods Adjustable moving Platen Skates Rigid Cast Platens with FEA Adjustable Pressure setting of Closing & Opening Stage Proportional Speed Control with 5 Closing & 5 Opening Speed Adjustable 2 Stage Mould Safety Pressure & 1 Stage Speed Position Based Ramping for Accurate Position Switching Precise Speed & Pressure Control Linear Position Transducer for Accurate Clamp Position Control Sensitive Mould Protection with Try Again Circuit Stage Wise Actual Time Display Insert Moulding Program Actual Tonnage Display on Screen Knock-Out Bar 2 Stage Programmable Ejector Forward Profile with Soft Eject Ejector Speed & Pressure adustable on Screen Linear Transducer for Ejector Position Pulsating Ejector Strokes upto 9 Pulses Intermediate Retract Set Point Ejector Stay Forward & Forward Dwell Timer MAIN INJECTION UNIT • • • • • • • • • • • • • • 6 Stage Injection Velocity & 15 Stage Injection Pressure Profile 5 Stage Screw Speed & 5 Stage Back Pressure Control (Setting through Screen) Digital setting of Extruder RPM & Digital Read out of Actual RPM Wide Choice of Injection Units with A’-A-B Screw/Barrel Combinations Easy Injection Unit Swivelling Switch Over from Fill to Pack based on Position or Time Linear Position Transducer for Accurate Injection Position Control Injection Decompression Before / After Refilling or Both Semi-Auto Purge, Cold Slug removal & Intrusion Moulding Programs Aluminum Chequered Plate below Purge Area Sprue Break with Timer Injection start, Suck-back & Melt Decompresion - Delay Timer Graphically Adjustable Alarm Bands for Injection Pressure Sliding Hopper TEMPERATURE CONTROL • Actual Current Display of Heating Zones • Heater Failure & Thermocouple Failure Detection • Accurate PID Temperature Control settable on Screen • Feed Throat Temperature Indication • Auto Heat Startup & Shutdown • Heat Standby after set number of Cycles • Soak Timer for Cold Start Protection • High / Low Temperature Alarm • Set & Actual Temperature Data with Bar Graph CONTROLS • 22 Parameter Monitoring for last 1000 cycles with Graphics • 10.4” TFT Color Display with Alpha - Numeric Keypad • Actual Injection Speed & Pressure Graph Display • 80 Mould Data Storage • Configurable Multilevel Password with Operator’s Name • Graphically Presentation of Last 48 Hours Production • Daily Production Data of Last 1 Year • Customized Setup Menu • High / Low Limit Display for Each Adjustable Parameter • I / 0 diagnosis - Analog & Digital • Timer Precision in 0.01 Second • Change Log Menu: logs last 100 Set Points Changes with Time & Date • Statistical Process Control ( SPC ) with Graphics • Process Mode: Functions with its Co-fuctions on a Single Key Press • Note Pad & Maintenance Scheduling • Freely Programmable Smart Outputs & Inputs • Over View Screen with Graphical Display of Machine Functions • Soft Keys for Fast Access of Select Menus • Auto shut down • Visual & Audible Alarm • 1000 Alarm History with Date & Time Log • Printer Interface with USB Port 2 Component Hydraulic Injection Moulding Machine 150 to 450 Ton Servo Motor Driven Pump Ergonomic Hydraulic Layout for Easy Approach Valves Placed near Actuators for Rapid Response Pre-Heating Circuit for Hydraulic Oil Low Oil Level Audible Alarm & Motor Shut Down Continuous Oil Filtration with 10 Micron Filter Audible Alarm for Filter Clogging Injection by Dedicated Servo Motor Reffiling by Dedicated Servo Motor Seperate Controller for Secondary Injection Unit 6 Stage Injection Velocity & 10 Stage Injection Pressure Profile 3 Stage Screw Speed & 3 Stage Back Pressure Control (Setting through Screen) Digital setting of Extruder RPM & Digital Read out of Actual RPM Wide Choice of Injection Units with A-B-C Screw/Barrel Combinations Switch Over from Fill to Pack based on Position or Time Accurate Injection Position Control through Direct Servo Injection Decompression Before / After Refilling or Both Injection start, Suck-back & Melt Decompresion - Delay Timer Auto Lubrication on Secondary injection Unit with Monitoring Mould Data Storage Process Data Monitoring High Performance 2 Component Hydraulic Machine AVAILABLE OPTIONS • • • • • • • • • • Air Ejection Hydraulic Core pull Feed Throat Temperature Control PID Oil Temperature Control Part Drop Detect for Single Cavity Water Battery with Temperature Indicator Water Manifolds Robot Interface (SPI / EUROMAP) Extra Heating Zones Nozzle Contact Force by Pressure Switch Jam Bar T-slot Platens Extended Daylight with Ram Spacer Eject Retract Limit Switch Verification Insulated Heater Band Bimetallic Barrel & Hardened / Coated Screw All specifications reflect average values based on typical machine layouts. Actual figures will vary depending on final machine configuration. Performance specifications are based on theoretical data. Photograph may show attachments or accessories, which may not be part of the standard scope of supply. Due to continual improvements, specifications & some components are subject to change without notice. FERROMATIK MILACRON INDIA PVT. LTD. (Formerly known as Cincinnati Milacron Ltd.)
Open the catalog to page 1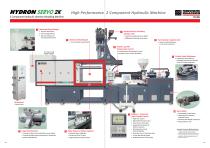
HYDRON SERVO 2K High Performance 2 Component Hydraulic Injection Moulding Machine ~| Advanced Clamp Design • Separate Prefill Tank • Fast Tonnage Build-up • Special Hydraulics for Fast Clamp Movements 3| Generous Mould Space • Accommodates Large Moulds 2 Component Hydraulic Machine M5HI1 fu!u MILACRON ii wmm India Vertical Electric Secondary Injection Unit • Injection by Dedicated Servo Motor • Reffiling by Dedicated Servo Motor Closed Loop PID Temperature Control • Provides precise Temperature Control • Excellent Process Control & Stability Twin Cylinder Injection Unit • Uniform Load...
Open the catalog to page 2