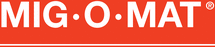
Catalog excerpts
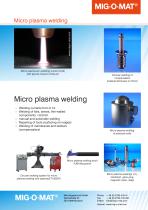
Micro plasma welding Micro plasma arc (welding current 0,5A) with typical column of the arc Circular welding of compensators (material thickness 0,15mm) Micro plasma welding » » » » » Welding currents from 0.1A Welding of foils, sieves, thin-walled components <0,5mm manual and automatic welding Repairing of tools (surfacing ion edges) Welding of membranes and bellows (compensators) Micro plasma welding of pressure cells Micro plasma welding torch PJB100superior Micro plasma weldings (f.l.): membran, glow plug, magnetic valve, relay) Circular welding system for micro plasma welding with plasmaJET100SPS Mikrofügetechnik GmbH Werksstraße 20 DE-57299 Burbach
Open the catalog to page 1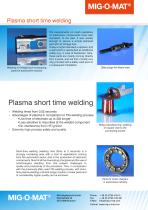
Plasma short time welding Welding of Omega-lock at stamping parts for automotive industry The requirements on crash resistance of automotive components have also increased. In the past, it was usually enough to secure a simple stamped part with an Omega lock. Today a higher standard is applied, and a weld point is demanded as additional safety (e.g. in case of headrests). Here, these parts are mostly coming directly from a press, and are then (mostly very oily) provided with a safety weld point in a subsequent installation. Glow plugs for diesel-cars Plasma short time welding » Welding...
Open the catalog to page 2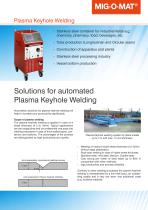
» Stainless steel container for industrial fields e.g. chemistry, pharmacy, food, beverages, etc. » Tube production (Longitudinal- and Circular seam) » Construction of apparatus and plants » Stainless steel processing industry » Vessel bottom production Automation solutions for plasma keyhole welding will help to increase your productivity significantly. Scope of plasma welding The plasma keyhole welding is applied in case of a sheet thickness of 2 to 10mm. Typical applications are the longitudinal and circumferential one pass butt welding processes in case of thick-walled pipes, containers...
Open the catalog to page 3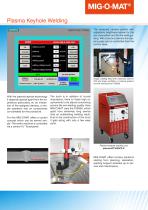
Plasma Keyhole Welding The assigned camera system with adjustable brightness serves for the arc observation and for the weld guiding. With a second camera the capping pass can be controlled from the control desk. Image: welding head with motorized slide for AVC and linear oscillation, 2 camera systems and the welding torch PJB350 With the plasma keyhole technology it depends special apart from the experience particularly on an interaction of the assigned devices, a simple operation and on components co-ordinated for the procedure. For this MIG·O·MAT offers a control concept which can be...
Open the catalog to page 4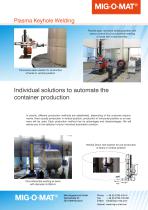
Plasma Keyhole Welding Flexible pipe- and tank welding system with sector-control for circumferential welding of tubes with small diameter. Transverse seam welder for production of tanks in vertical position Individual solutions to automate the container production In practis, different production methods are established, depending of the customer requirements. Here usually production in vertical position, production in horizontal position or on seamers will be used. Each production method has its advantages and disadvantages. We will advise you in the selection of your individual...
Open the catalog to page 5
Plasma-arc powder surfacing Anti-wear surfacing at tools Plasma-arc powder surfacing of valves Powder-feeder and Plasma powder welding torch 350A Plasma-arc powder surfacing » » » » » » Surfacing for anti-wear protection and corrosion resistance Repair-welding of tools Low dilution with base material (<5% possible) Low rework Even and well adjustable layer thickness by separating the supply of energy and filler material Areas of application: Manufacturing of fittings, power plant construction, refineries, knife coating, extruder manufacturing, mining industry, coating of cylinders and screw...
Open the catalog to page 6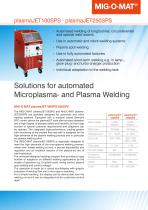
» Automated welding of longitudinal, circumferential and special weld seams » Use in automatic and robot welding systems » Plasma spot welding » Use in fully automated factories » Automated short-term welding e.g. in lamp-, glow plug- and turbo charger production » individual adaptation to the welding task Solutions for automated Microplasma- and Plasma Welding MIG-O-MAT plasmaJET100SPS/250SPS The MIG-O-MAT plasmaJET100SPS and MIG-O-MAT plasma-JET250SPS are specially designed for automatic and robot welding systems. Equipped with a modular based Siemens SPC control device the plasmaJET...
Open the catalog to page 7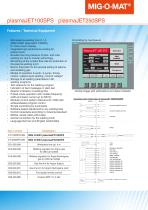
Features / Technical Equipment » Microplasma welding from 0,1 A (MIG-O-MAT plasmaJET 100SPS) » 6” colour touch display » Integrated high-perfomance cooling for plasma torch » Excellent burning behavior of pilot- and main welding arc due to inverter technology » Monitoring of the coolant flow-rate for protection of the plasma welding torch » Built-in flowmeter for the precise setting of plasma and shielding gas » Modes of operation 2-cycle / 4-cycle / timing control / plasma spot welding / control voltage* » Storage of all welding parameters in 60 welding programs » Test sequence for the...
Open the catalog to page 8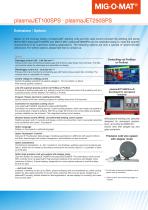
plasmaJET100SPS · plasmaJET250SPS Extensions / Options Based on the modular design of plasmaJET welding units and the used control concept the welding unit series MIG·O·MAT plasmaJET100SPS and MIG·O·MAT plasmaJET250SPS can be extended easily to meet the specific requirements of its customers welding applications. The following options are only a sample of recommended extensions. For further options, please feel free to contact us. Options Plasmagas control 0,05 – 2,00 liter/min ** Precise control and monitoring of plasma gas with thermal mass stream flow controller. The different nominal...
Open the catalog to page 9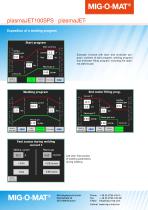
Exposition of a welding program Ptcfkjw shield Inq qas See Start program Start current Is Current A MIGOMAT' Example: 2-stroke with start- and endcrater program, consists of start program, welding program and endcrater filling program, including the optional plasma gas MIG-O-MAT® Mikrofugetechnik GmbH WerksstraBe 20 DE-57299 Burbach
Open the catalog to page 10All MIG-O-MAT catalogs and technical brochures
-
Flame-Polishing Equipment
2 Pages
-
Microfl ame Soldering Units
2 Pages
-
MIG·O·MAT® company brochure
8 Pages