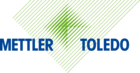
Group: Mettler-Toledo

Catalog excerpts

White Paper Validation of Weighing Processes Are You Up-to-Date? Good Manufacturing Practice guidelines are continuously revised to consider technological changes and current practices in pharmaceutical manufacturing. Process validation is a key requirement of all regulations. The weighing experts from METTLER TOLEDO help you design weighing processes, qualify weighing equipment and continuously monitor it to ensure reliable product quality and avoid unpleasant surprises during audits. Process validation contributes significantly to ensuring drug quality, but it also places a heavy burden on pharmaceutical manufacturers. It requires significant effort and resources that result in additional costs. Pharmaceutical production, and the validation of such a process, is a complex task that needs to consider many aspects, including weighing. Weighing has a significant impact on quality, both in production and in the laboratory. Therefore, weighing equipment must be qualified and critical weighing processes need to be validated. This white paper explains how METTLER TOLEDO weighing compliance experts can help you get through the validation lifecycle efficiently. Contents 1 Validation Overview & Recent Regulatory Changes 2 Weighing Processes in Pharmaceutical Manufacturing 3 Process Design 4 Efficient Process Qualification for Weighing Processes 5 Continuous Weighing Process Verification 6 Summary 7 Additional resources
Open the catalog to page 1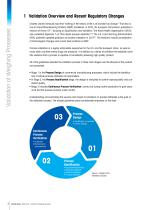
Validation of Weighing Processes 1 Validation Overview and Recent Regulatory Changes Charles Darwin famously said that "nothing in the history of life is as constant as change." That also is true for Good Manufacturing Practice (GMP) Guidelines. In 2015, the European Commission published a revision of Annex 15[1], focusing on Qualification and Validation. The World Health Organization (WHO) also published Appendix 7 on "Non-sterile process validation."[2] The U.S. Food and Drug Administration (FDA) published updated guidance on process validation in 2011[3]. The revisions include...
Open the catalog to page 2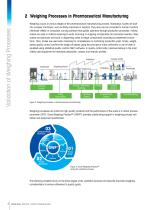
Validation of Weighing Processes 2 Weighing Processes in Pharmaceutical Manufacturing Weighing occurs at various stages of the pharmaceutical manufacturing process. Nowadays, scales are built into complex machinery, such as filling machines or reactors. They also can be connected to human machine interfaces (HMIs) or computers running software that guides operators through production processes. Initially, scales are used in material receiving to verify incoming or outgoing components and reconcile inventory. Next, scales and balances are found in dispensing areas to weigh components...
Open the catalog to page 3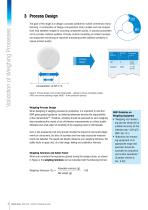
Validation of Weighing Processes Process Design The goal of this stage is to design a process suitable for routine commercial manufacturing. A combination of Design-of-Experiment (DoE) studies and risk analysis tools help establish ranges for incoming component quality, in-process parameters and in-process material qualities. Process controls consisting of material analysis and equipment monitoring at important processing points address variability to assure product quality. Raw Material Process Design Process Concentration of API in % Concentration of API in % Figure 4: Process design,...
Open the catalog to page 4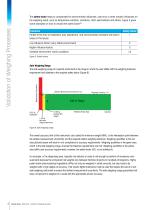
Validation of Weighing Processes The safety factor helps to compensate for environmental influences, user error or other random influences on the weighing result, such as temperature variation, vibrations, draft, electrostatics and others. Figure 5 gives some examples on how to choose the safety factor[5]. Figure 5: Safety factors Safe Weighing Range The safe weighing range of a specific instrument is the range in which the user fulfills both the weighing tolerance requirement and adheres to the required safety factor (Figure 6). The lowest accuracy limit of the instrument, also called the...
Open the catalog to page 5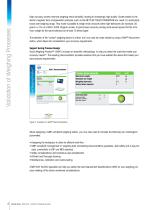
Validation of Weighing Processes High-accuracy scales minimize weighing result variability, leading to increasingly high quality. Scales based on the electro-magnetic force compensation principle, such as the METTLER TOLEDO PBK9/PFK9 line, result in a particularly broad safe weighing range. They make it possible to weigh small amounts within tight tolerances (for example, 50 grams +/-1% on a 600 x 0.001 kilogram scale). A typical lower accuracy analog scale would require that the minimum weight for the same tolerance be at least 10 times higher. The selection of the "correct" weighing...
Open the catalog to page 6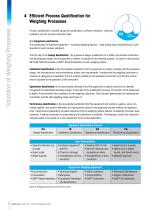
Validation of Weighing Processes 4 Efficient Procesglgualification fo0 Weighing Processes Process qualification includes equipment qualification, software validation, cleaning validation and the process validation itself. 4.1. Equipment qualification The qualification of important equipment - including weighing devices - used during drug manufacturing is a prerequisite for each process validation. The first step is the Design Qualification. The purpose of design qualification is to obtain documented verification that the proposed design of the equipment or system is suitable for the...
Open the catalog to page 7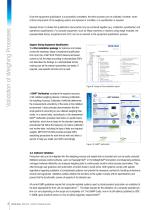
Once the equipment qualification is successfully completed, the entire process can be validated. However, when critical components of the weighing system are replaced or modified, a re-qualification is required. Revised Annex 15 states that qualification documents may be combined together (e.g. installation qualification and operational qualification). For complex equipment, such as filling machines or reactors using weigh modules, the preassembled factory acceptance test (FAT) can be an element in the equipment qualification process. IPac Installation Report Validation of Weighing...
Open the catalog to page 8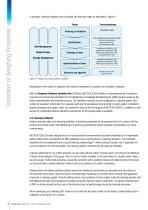
Validation of Weighing Processes In principle, software validation can be divided into five basic steps as described in Figure 11. Phase Documents/steps Revalidation of the system is required when critical components of a system are modified or replaced. With the Computer Software Validation Pac (CSVPac), METTLER TOLEDO offers a comprehensive set of validation manuals and product documentation for FormWeigh.Net or FreeWeigh.Net following the GAMP guide to speed up the entire implementation and validation process. The validation manuals are pre-configured for a general system and contain all...
Open the catalog to page 9All METTLER TOLEDO catalogs and technical brochures
-
TMA/SDTA 2+ STARe System
14 Pages
-
C-Series Checkweighers
6 Pages
-
InPro 6000 Sensor Series
12 Pages
-
Portable pH Meter Pro2Go
4 Pages
-
InPro® 3100 / InPro® 3100UD
4 Pages
-
Industrial Weighing Catalog
136 Pages
-
Weighing Component Catalog
272 Pages
-
eBook: Connected Weighing
12 Pages
-
Compact Weighing Systems
20 Pages
-
IND690batch
4 Pages
-
ACT100 Weight Transmitter
2 Pages