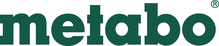

Catalog excerpts
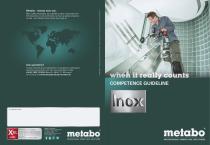
With 1,800 employees, 23 subsidiary sales companies and 100 importers on all continents, we have a global presence on site - and always there where you need us. Any questions? A team of product and application consultants is looking forward to hearing from you. You can reach them under +49 (0) 7022 72-3230 (Mon-Fri, 08:00 - 17:00 hours) or by email to anwendungsberatung@metabo.de. 6.54350.00/0911 · Printed in Germany/Imprimé en Allemagne – Subject to changes due to technical progress, factual and printing errors. Metabo - always near you. when it really counts Competence Guideline Your Metabo dealer: Your Metabo dealer: The Metabo 3-year warranty We give you an extra long 3 year warranty on all our products. Simply register up to 4 weeks after your purchase on the Internet and your regular guarantee is extended to three years. Register at www.metabo.com/xxl Metabo UK Limited 25 Majestic Road, Southampton Telephone 02380 732000 Fax 02380 747500 E-Mail metabo@metabo.co.uk www.metabo.co.u
Open the catalog to page 1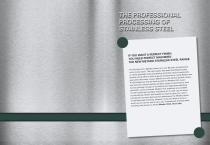
The professional processing of stainless steel ct finish, you want a perfe If machines: you need perfect Steel range. Metabo Stainless the NEW e 80 years of experienc etabo flows from over ace The life blood of a M mands that Metabo pl r. The high quality de in the metal secto in technically sing machines result ecialist metal proces can on these sp ies to match Metabo de range of accessor a wi sults. excellent tools. With will achieve perfect re using a Metabo you ar guarantee that when the Metabo XXL 3 ye t that we back up with ams, from A bold statemen ces, pipes or weld se it when...
Open the catalog to page 2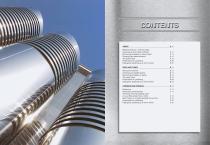
©oinrEmts AREAS Material removal - the first steps (opening up hot-rolled surfaces) Removing scratches on sheet metal Preparing the base structure The satin finish Preparation for polishing High-gloss polishing to a mirror shine Removal of tarnish Grinding out welded seams Removing scratches on pipes The satin finish Preparation for polishing High-gloss polishing to a mirror shine Deburring Reparing a small surface Grinding off a TIG welding seam on a profile welded into a mitre Satin finish on a profile welded into a mitre Preparation for polishing High-gloss polishing to a mirror shine
Open the catalog to page 3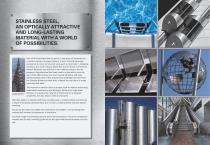
STAINLESS STEEL, AN OPTICALLY ATTRACTIVE AND LONG-LASTING MATERIAL WITH A WORLD OF POSSIBILITIES. You will find stainless steel is used in a vast array of industries, be it nuclear reactors in power stations, to vats in food & beverage companies to more commercial areas such as hand rails in shopping centres to the more intricate details that may be found in the family kitchen. Wherever you will look it won't take you long to find its presence. Stainless steel has been used in construction since the start of the 20th century as it is an visually attractive and long-lasting material. One of...
Open the catalog to page 4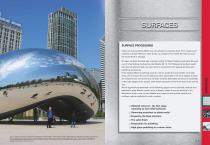
Surfaces Surface processing There are many surface effects you can achieve on stainless steel. From rough, matt surfaces to brush effects, to satin sheen, to a bright mirror finish like that found on the Cloud Gate in Chicago. On open surfaces the best way to achieve either of these finishes is primarily through use of a burnishing machine like the Metabo SE 12-115. Professional surface results can only be achieved with low rpm tools in conjunction with special grinding and polishing accessories. If the desired effect is anything close to a mirror polish the tool handler must take are...
Open the catalog to page 5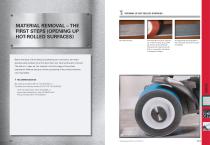
Opening up hot rolled surfaces Material removal – the first steps (opening up hot-rolled surfaces) Hot rolled surface. The rolled skin must be "opened up" in the first step using a P40 grit and full speed setting 6*, otherwise the metal will be left with an unworkable hard glaze in subsequent stages. A longitudinal grinding pattern, the rolled skin has been removed completely. Before the steps of burnishing and polishing can commence, hot rolled stainless steel surfaces must first have their very hard surface skin removed. The skill is to "open up" the material in the first stage of the...
Open the catalog to page 6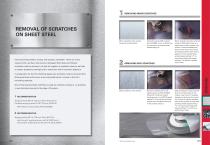
Removing minor scratches Removal of scratches on sheet steel Minor scratches to the surface caused by transportation Incorrect transportation, bumps and scrapes, vandalism - there are many reasons why a surface may become damaged. Both deep and shallow scratches must be removed, not just for hygienic or aesthetic reasons, but also Using the special VKS compact disc (6.26368), minor scratches can be removed in a single process (speed setting 5). Removing deep scratches Minor scratches are fully removed using the VKS wheel. Only very slight traces of disc rotation may remain. If required...
Open the catalog to page 7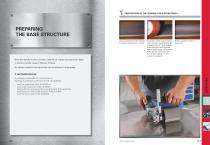
Preparation of the surface for a satin finish Preparing the base structure Coarse longitudinal finish left after the surface skin has been ’opened’. Preparation of the surface in three steps: start with sanding belt P 80 in speed setting 6*, then move on to the flap/nylon sanding wheel P 60 in speed setting 1-2* and then finish with the new sinus roller form P 180 in setting 1-2*. Part numbers on page A6. Perfect satin finish with no transitions. Once the material surface has been ’opened-up’ further processing can begin to achieve a whole range of different finishes. An almost...
Open the catalog to page 8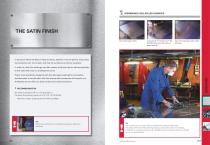
Burnishing cold rolled surfaces The satin finish Cold rolled sheet 1.4301. Using the SE 12-115 with the P 180 6.23499 rubber sanding roller on speed setting 1*. Very fine longitudinal satin finish achieved. In particular when working on large surfaces, attention must be paid to ensure that the transitions can not be seen and that the surfaces are without scratches. In order to meet this challenge, we offer system solutions that are tailored perfectly to this need and ensure a professional result. Power tools specificaly designed with the right speed settings for processing stainless steel...
Open the catalog to page 9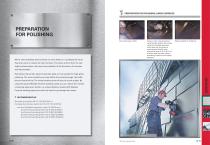
Preparation for polishing large surfaces Preparation for polishing Cold rolled sheet 1.4301. Using a "criss-cross procedure" systematically prepare the surface using the inflatable expansion roller fitted with the Pyramid sanding belts. Steadily work through the grits, A 45, A 30, A 16, A 06 one after the other with the burnishing machine on full speed setting 6*. Sheet prepared for polishing. Mirror shine stainless steel surfaces not only reflect on a professional result, they also serve to reduce the risk corrosion. The lower and the finer the raw depth surface values, the lower the...
Open the catalog to page 10All Metabowerke catalogs and technical brochures
-
KE 3000
2 Pages
-
MAG 32
2 Pages
-
Basic 250-50 W OF
2 Pages
-
TS 254
2 Pages
-
TKHS 315 C
2 Pages
-
W 18 LTX 150 QUICK
2 Pages
-
WB 18 LTX BL 150 QUICK
2 Pages
-
WPB 18 LTX BL 150
2 Pages
-
POWERMAXX BS QUICK PRO SET
2 Pages
-
POWERMAXX BS QUICK PRO
2 Pages
-
POWERMAXX BS QUICK BASIC
2 Pages
-
POWERMAXX BS BASIC SET
2 Pages
-
PowerMaxx BS Basic
2 Pages
-
METABO INDUSTRIAL BROCHURE
11 Pages
-
Metabo main catalogue 2018/2019
306 Pages
-
Metabo
40 Pages
-
METABO'S COMPRESSED AIR SYSTEMS
37 Pages
-
MT 400 Quick Set
2 Pages
-
INTERFACE PAD 150 MM
1 Pages
-
KPA 18 LTX 600
2 Pages
-
METABO COMPRESSED AIR
37 Pages
-
2014/2015 Power Tools + Accessories
291 Pages
-
Accessory Range 2011/2012
268 Pages
-
Contents, Cordless Tools
40 Pages
-
Main Catalogue 2010/2011
268 Pages