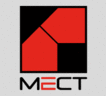
Catalog excerpts
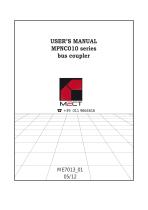
USER'S MANUAL
Open the catalog to page 1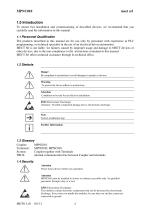
1.0 Introduction To ensure fast installation and commissioning of described devices, we recommend that you carefully read the information in this manual. 1.1 Personnel Qualification The products described in this manual are for use only by personnel with experience in PLC programming, or technical specialist in the use of an electrical-driven automation. MECT Srl is not liable for failures caused by improper usage and damage to MECT devices or other devices, due to the non-compliance to the instructions contained in this manual. MECT Srl offers technical assistance through its technical...
Open the catalog to page 4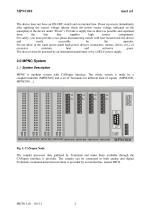
The device does not have an ON-OFF switch and an internal fuse. Power up occurs immediately after applying the correct voltage (please check the power source voltage indicated on the nameplate of the device under "Power"). Provide a supply line as direct as possible and separated from the line that supplies high power components. For safety, you must provide a two-phase disconnecting switch with fuse located near the device and easily accessible by the operator. Do not allow in the same power panel high power devices (contactors, motors, drives, ect.), or excessive moisture, heat and...
Open the catalog to page 5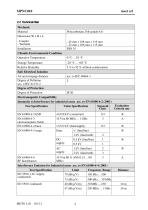
2.2 Technical Data Mechanic Material Dimension W x H x L - Coupler - Terminal Installation Climatic Environmental Condition Operative Temperature Storage Temperature Relative Humidity Safe Electrical Isolation Air and creepage distance Degree of Pollution acc. o IEC 61131-2 Degree of Protection Degree of Protection Electromagnetic Compatibility Immunity to Interference for industrial areas acc. to EN 61000-6-2 (2001) Evaluation Test Specification Value Specification Strength Criteria one Class EN 61000-4-2 ESD EN 61000-4-3 electromagnetic fields EN 61000-4-4 burst EN 61000-4-5 surge 1 kV/2...
Open the catalog to page 6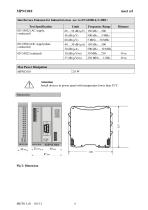
Interference Emission for Industrial areas acc. to EN 61000-6-3 (2001) Test Specification EN 55022 (AC supply, conducted) EN 55022 (DC supply/data, conducted) EN 55022 (radiated) Limit Frequency Range 66 Value/IQPI ... 56 dB (µV) 150 kHz ... 500 kHz kHz ... 5 MHz 56 dB (µV) 500 60 dB (µV) 5 MHz ... 30 MHz 40 ... 30 dB (µA) 150 kHz ... 500 kHz kHz ... 30 MHz 30 dB (µA) 500 30 dB (µV/m) 30 MHz ... 230 MHz 37 dB (µV/m) 230 MHz ... 1 GHz Attention Install devices in power panel with temperature lower than 55°C Dimension
Open the catalog to page 7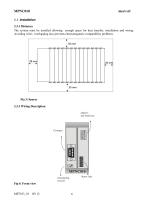
2.3 Installation 2.3.1 Distances The system must be installed allowing enough space for heat transfer, installation and wiring. Avoiding wires overlapping also prevents electromagnetic compatibility problems. Fig 3: Spaces 2.3.2 Wiring Description address and baud rate Status leds terminating resistor
Open the catalog to page 8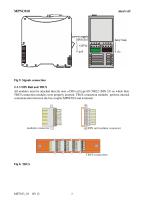
Fig 5: Signals connection 2.3.3 DIN Rail and TBUS All modules must be attached directly onto a DIN rail type EN 50022 (DIN 35) on which their TBUS connection modules were properly inserted. TBUS connection modules perform internal communication between the bus coupler MPNC010 and terminals. modular connector DIN rail modular connector TBUS connection
Open the catalog to page 9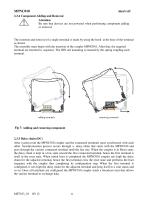
2.3.4 Component Adding and Removal Attention Be sure that devices are not powered when performing component adding or removal. The insertion and removal of a single terminal is made by using the hook at the base of the terminal as shown. The assembly must begin with the insertion of the coupler MPNC010. After that, the required terminal are inserted in sequence. The DIN rail mounting is ensured by the spring coupling each terminal. adding terminals removing terminals Fig 7: Adding and removing component 2.3.5 Daisy chain (DC) After system reset the MPNC010 coupler and the connected...
Open the catalog to page 10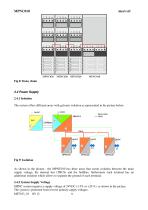
2.4 Power Supply 2.4.1 Isolation The system offers different areas with galvanic isolation as represented in the picture below. Fig 9: Isolation As shown in the picture , the MPNC010 has three areas that create isolation between the main supply voltage, the internal bus (TBUS) and the fieldbus; furthermore each terminal has an additional isolation which allows to separate the ground of each terminal. 2.4.2 System Supply Voltage MPNC system requires a supply voltage of 24VDC (-15% or +20 %) as shown in the picture. The system is protected from reverse polarity supply voltages. ME7013_01 05/...
Open the catalog to page 11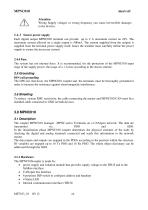
mect srl Attention Wrong Supply voltages or wrong frequency can cause irreversible damages to the devices. 2.4.3 Sensor power supply Each digital output MPNC020 terminal can provide up to 2 A maximum current on 24V. The maximum current allowed on a single output is 500mA. The current supplied from the outputs is supplied from the terminal power supply itself, hence the installer must carefully define the power supply to ensure the necessary current. 2.4.4 Fuse The system has not internal fuses. It is recommended, for the protection of the MPNC010 input stage of the supply power, the usage...
Open the catalog to page 12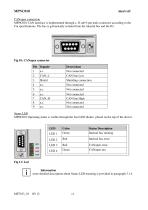
CANopen connection MPNC010 CAN interface is implemented through a D sub 9-pin male connector according to the Cia specifications. The bus is galvanically isolated from the internal bus and the IO. Fig 10: CANopen connector Pin Segnale 1 n.c Shielding connection Not connected CAN line High Not connected Not connected Status LED MPNC010 Operating status is visible through the four LED diodes placed on the top of the device. Color Green Status Description Internal bus running CANopen error Fig 11: Led Information more detailed description about Status LED meaning is provided in paragraph 3.1.4
Open the catalog to page 13
Address (module ID) The DIP switch is used to set both the baud rate and the address (module ID) of the CANopen bus. The address setting is done using switches 1 to 5, so valid addresses are 1 to 31. The address setting must be done before applying the supply voltage since one of the first transactions on power-on is reading the state of the DIP switches. Finding zero as module address triggers an error condition so the four LED start blinking. Address encoding is shown in the table below. S-1 To set a “1” move the switch on the DIP toward the ON side.
Open the catalog to page 14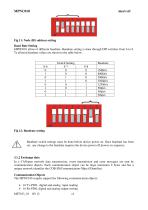
Fig 11: Node (ID) address setting Baud Rate Setting MPNC010 allows 6 different baudrate. Baudrate setting is done through DIP switches from 6 to 8. Te allowed baudrate values are shown in the table below. Baudrate switch settings must be done before device power on. Once baudrate has been set, any change to the baudrate requires the device power off /power on sequence. 3.1.2 Exchange data In a CANopen network data transmission, event transmission and error messages are sent by communication objects. Each communication object can be large maximum 8 bytes and has a unique network identifier...
Open the catalog to page 15All MECT SRL catalogs and technical brochures
-
TPAC1008
22 Pages
-
TPAC1007
14 Pages
-
TPAC1006
22 Pages
-
MPA-MPV M6
42 Pages
-
MPA386 M6
39 Pages
-
MPP P6
19 Pages
-
MPA-MPV P6
18 Pages
-
MP40 P6 Simple imput
16 Pages
-
MP40 P6 Multi input
17 Pages
-
MPX28
8 Pages
-
MPSN20
2 Pages
-
MPCV015
20 Pages
-
MPT390 M6
61 Pages
-
MPT91 M1
66 Pages
-
MPT90 M1
46 Pages
-
MPT60 M1
45 Pages
-
MPT100 M1
35 Pages
-
MPCIB396 P6
41 Pages
-
MPCIB20 M1
25 Pages
-
MPCT301 P6
53 Pages
-
MPCT300 P6
37 Pages
-
MPCT30 P6
36 Pages
-
MPCT20 M1
35 Pages
-
MP2200 M6
44 Pages
-
MP1200 P6
36 Pages
-
MPPV340 M6
40 Pages
-
MPO347 M6
40 Pages
-
MPP323 M6
42 Pages
-
MPPV010 P6
40 Pages
-
MP45 P6
18 Pages
-
MPM P6
34 Pages
-
MP30 P2
15 Pages
-
MP20 M1
35 Pages
-
MPNC030
12 Pages
-
TPLC005
28 Pages
-
MPNC020
13 Pages
-
TP1070
15 Pages
-
TP1057
15 Pages