
Group: Mecalux

Catalog excerpts
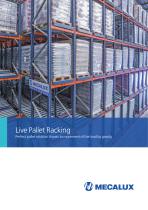
Live Pallet Racking Perfect pallet rotation thanks to movement of the load by gravity
Open the catalog to page 1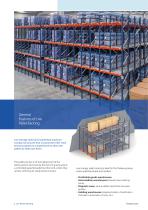
General Features of Live Pallet Racking Live storage racking for palletised loads are compact structures that incorporate roller track sections placed on a sloped lane to allow the pallets to slide over them. The pallets are put in at the highest part of the rolling section and move by the force of gravity and at a controlled speed towards the other end, where they remain until they are ready to be removed. Live storage pallet racking is ideal for the following areas, where palletised loads are handled: - Perishable goods warehouses. - Intermediate warehouses between two working zones. -...
Open the catalog to page 2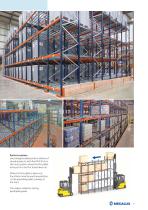
Perfect rotation Live storage enables perfect rotation of stored products, with the FIFO (First-in, First-out) system, where the first pallet to be put in is the first to be taken out. When the first pallet is taken out, the others move forward one position, so the preceding pallet is always at the front. This makes it ideal for storing perishable goods.
Open the catalog to page 3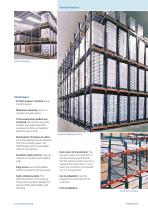
General Features Lubricant Industry Advantages - Perfect product rotation using the FIFO system. - Maximum capacity as this is a compact storage system. - Time saved when pallets are removed. All products are easily located, thus reducing forklift manoeuvring time, as travelling distances are minimal. Frozen bread/bakery sector - Elimination of clashes in aisles, since the loading aisles are separate from the unloading aisles. The forklifts place and remove pallets without interruptions. - Excellent stock control. Only one reference is stored in each loading aisle. - Easy access, as all the...
Open the catalog to page 4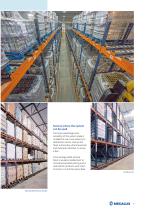
Sectors where the system can be used The many advantages and versatility of this system make it suitable for use in any industry or distribution sector, such as the food, automotive, pharmaceutical and chemical industries, to name a few. A live storage pallet racking block is usually installed next to conventional pallet racking and is reserved for products with a fast turnover, or a shorter expiry date. Food sector Chemical/Perfume Sector
Open the catalog to page 5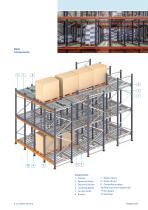
Basic Components Components 1. Frames 2. Dynamic Beam 3. Dynamic Profile 4. Levelling plates 5. Anchor bolts 6. Rollers 6 Live Pallet Racking 7. Brake rollers 8. Brake drums 9. Centralising strips 10. Pallet retainers (optional) 11. Exit beam 12. End stop
Open the catalog to page 6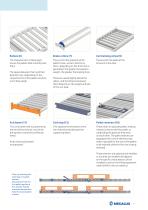
The characteristics of these parts ensure the pallets slide smoothly over them. They control the speed at which pallets move, and act directly on them, depending on the force that is generated. The greater the speed or weight, the greater the braking force. These center the pallet at the entrance to the aisle. The spaces between them and their diameter vary, depending on the characteristics of the pallets and how much they weigh. These are raised slightly above the rollers, and the distance between them depends on the weight and size of the unit load. This is the beam that is positioned at...
Open the catalog to page 7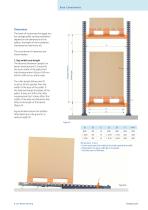
Basic Components The levels of clearances that apply to a live storage pallet racking installation depend on the dimensions of the pallets, the depth of the installation, maintenance machinery, etc. 1. Bay width and height The distance between uprights (or beam measurement E) is equal to the front width of the pallet with load (measurement A) plus 160 mm (which is 80 mm on either side). The usual levels of clearances are shown below. The roller length (dimension D) must be 30 mm greater than the width of the base of the pallet. If the load overhangs the edges of the pallet, it does not...
Open the catalog to page 8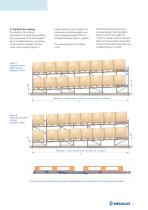
2. Depth of the racking The depth of the racking (dimension X) is obtained by adding the measurements of all the pallets plus a variable tolerance, according to the number of pallets and the construction system (figure 7). If pallet retainers are installed, the measurement will be greater, as a space of approximately 300 mm is needed between the two pallets. The usual gradient of the slope is 4%. The following drawings show two examples of racking depth, both of which have pallets of 1,200 mm deep. The first example does not have a pallet retainer but the second example does have one...
Open the catalog to page 9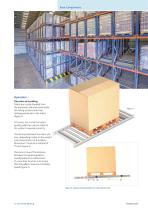
Basic Components Operation Direction of handling Pallets are usually handled from the narrowest side and move inside the rolling sections with their skidsperpendicular to the rollers (figure 1). Of course, it is crucial that good quality pallets are used in order for the system to operate correctly. The distance between the rollers can vary, depending mainly on the weight and characteristics of the pallets. Dimension Y must be a multiple of 75 mm (figure 2). The same is true of the distance between the speed regulators, usually brake drums (dimension X), since their function is to ensure...
Open the catalog to page 10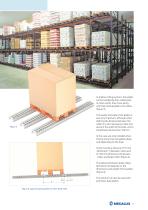
In shallow rolling sections, the pallets can be handled by their widest part. In other words, they move along with their skids parallel to the rollers (figure 3). The quality and state of the pallets is also very important, although when defining the distance between the rollers it is also necessary to take into account the width of the skids, which shouldnever be less than 100 mm. In this case, are only installed when storing more than two pallets deep, and depending on the load. There must be a distance of 75 mm (dimension Y) between rollers and of 100 mm (dimension Z) between rollers and...
Open the catalog to page 11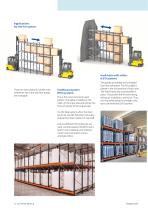
Applications for the live system Push-back with rollers (LIFO system) There are two solutions, whose main difference lies in the way that goods are managed: Traditional system (FIFO system) This is the most commonly used system. The pallet is loaded on the rollers in the input side and rolls by the force of gravity to the output side. The goods are loaded and unloaded from the same aisle. The first pallet is placed in the first position of each aisle. The forklift puts the second pallet in place. This pushes the first one along, taking up its position, and so on. Thus, the first pallet...
Open the catalog to page 12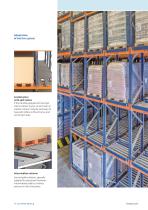
Adaptation of the live system Combination with split rollers If the handling equipment has rigid masts (stacker trucks, turret trucks or stacker cranes) it may be necessary to have split rollers at the entrance and exit of each aisle. Intermediate retainer Second pallet retainer, specially adapted for placement between intermediate pallets to reduce pressure in very long aisles. 14 Live Pallet Racking
Open the catalog to page 14All MECALUX catalogs and technical brochures
-
Conveyor systems for boxes
48 Pages
-
Pallet conveyor systems
64 Pages
-
Automated warehouses
120 Pages
-
Wire mesh partitions & cages
8 Pages
-
Mezzanines
20 Pages
-
Cantilever Racking
24 Pages
-
Metal Point Boltless Shelving
24 Pages
-
Racking for Live Picking
36 Pages
-
M3 Shelving for picking
36 Pages
-
M7 Longspan shelving
31 Pages
-
Push-back pallet racking
12 Pages
-
Pallet Shuttle
36 Pages
-
Movirack Mobile Pallet Racking
20 Pages
-
Drive-in Pallet Racking
32 Pages
-
Conventional Pallet Racking
44 Pages