
Group: Mecalux

Catalog excerpts
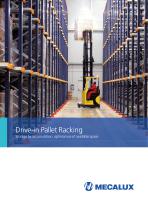
Drive-in Pallet Racking Storage by accumulation: optimal use of available space
Open the catalog to page 1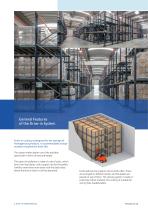
General Features of the Drive-in System Drive-in racking is designed for the storage of homogenous products. It accommodates a large number of pallets for each SKU. This system makes better use of the available space both in terms of area and height. This type of installation is made of a set of racks, which form inner load lanes, with support rails for the pallets. Forklifts enter these inner lanes with the load raised above the level at which it will be deposited. 2 Drive-in Pallet Racking Each load lane has support rails on both sides. These are arranged on different levels, and the...
Open the catalog to page 2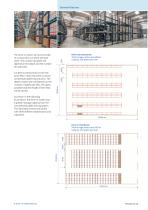
General features Pallet rack distribution Total storage surface area: 858 m2 Capacity: 306 pallets per level It is best to store products with the same SKU in each load lane, to avoid unnecessary pallet manoeuvres. The depth of each lane will depend on the number of pallets per SKU, the space available and the length of time they will be stored. The drive-in system can accommodate as many SKU’s as there are load lanes. The number of pallets will depend on the depth and the number of load levels. As shown in the following illustrations, the drive-in system has a greater storage capacity than...
Open the catalog to page 4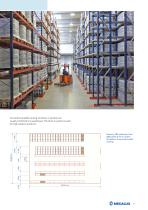
Conventional pallet racking and drive-in systems are usually combined in a warehouse. The drive-in system is used for high rotation products. Capacity: 383 pallets per level (200 pallets drive-in system, 183 pallets conventional pallet racking)
Open the catalog to page 5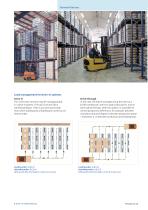
General features Load management for drive-in systems Drive-in This is the most common way of managing loads in a drive-in system. The racks function like a warehouse depot. There is just one access aisle, from which loading and unloading are carried out in reverse order. Loading order: A,B,C,D Unloading order: D,C,B,A LIFO system (the first load in is the last one out) 6 Drive-in Pallet Racking Drive-through In this case, the load is managed using the racks as a buffer warehouse, with two load access points, one on each side of the bays. With this system, it is possible to control...
Open the catalog to page 6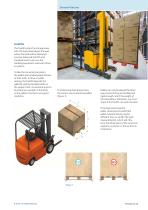
General features Forklifts The forklift enters the storage lanes with the load raised above the level where the load will be deposited. Counter-balanced forklifts and standard reach trucks are the handling equipment used with drivein systems. Unlike the conventional system, the pallets are handled perpendicular to their skids. In drive-in pallet racking, the forklift deposits the pallet by resting the pallet skids on the support rails. An extreme amount of pressure is exerted on the skids, so the pallets must be in very good condition. The following illustrations show the correct way to...
Open the catalog to page 8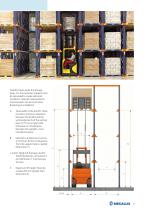
Forklifts travel inside the storage lanes. So, the necessary margins must be calculated to create safe work conditions. Specific measurements must be taken into account when designing an installation: Operator’s protective structure. A minimum 50 mm of clearance from the support rails is needed (dimension Y). Total width of the forklift. There must be a minimum clearance between the forklift and the vertical elements of the racking bays of 75 mm on each side. Dimension X, the distance between the uprights, must include this space. Maximum lift height. Must be at least 200 mm greater than...
Open the catalog to page 9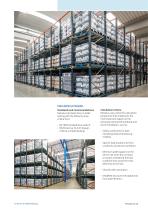
Calculation principles Standards and recommendations Mecalux calculates drive-in pallet racking with the following main criteria from: - EN 1993 standard (Eurocode 3) - FEM Directive 10.2.07 (Design of Drive-in Pallet Racking) Calculation criteria Mecalux uses a powerful calculation programme that implements the most important aspects of the previously mentioned standards and recommendations, such as: - Safety coefficients for both increasing loads and reducing material. - Specific load situations for limit conditions and service conditions. - Minimum pallet support on the 20 mm rail when...
Open the catalog to page 10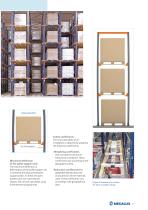
Displaced pallet Maximum deflection of the pallet support rails The maximum deflection or deformation of the pallet support rail is limited to the distance between supports/200. As these are open profiles with non-symmetrical shapes, the rails are calculated using finite element programmes. Safety coefficients The structural safety of an installation is obtained by adopting the following coefficients: -Weighting coefficients that increase the actions or loads to be considered. These coefficients vary according to the geographical area. -Reduction coefficients for material that decrease the...
Open the catalog to page 11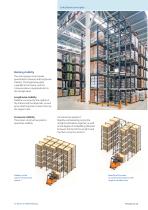
Calculation principles Racking stability The racking bays must provide guaranteed crosswise and lengthwise stability. The lengthwise plane is parallel to the frame, and the crosswise plane is perpendicular to the storage lanes. Lengthwise stability Stability is ensured by the rigidity of the frames and the diagonals, as well as by attaching them to each other by the support rails. Crosswise stability Three basic constructive systems guarantee stability. Stability of the racks in constructive system 1 12 Drive-in Pallet Racking Constructive system 1 Rigidity is obtained by joining the...
Open the catalog to page 12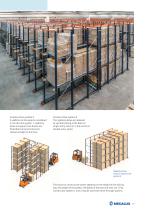
Constructive system 2 In addition to the aspects considered in constructive system 1, rigidising lanes and upper cross braces are fitted that transmit horizontal stresses straight to the floor. Constructive system 3 The rigidising lanes are replaced by vertical bracing at the back (in single-entry racks) or in the centre (in double-entry racks). Stability of the racks in constructive system 3 The choice of constructive system depends on the height of the racking bay, the weight of the pallets, the depth of the lane and their use. Only constructive systems 1 and 2 may be used with...
Open the catalog to page 13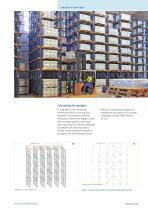
Calculation principles Calculating the uprights The upright is one of the main elements of drive-in racking and, therefore, must be very carefully calculated. Unlike what happens with other storage systems, with these racks the upright is not only subjected to compressive forces but also to flexion, requiring that the upright is provided with the necessary inertia. Mecalux's calculation programme implements the aspects of Eurocode 3 standard and the FEM Directive 10.2.07. NOMINAL LOAD – LOADS CONSIDERED NOMINAL LOAD --- FINITE ELEMENT MESH 14 Drive-in Pallet Racking Figure 7. Load...
Open the catalog to page 14All MECALUX catalogs and technical brochures
-
Conveyor systems for boxes
48 Pages
-
Pallet conveyor systems
64 Pages
-
Automated warehouses
120 Pages
-
Wire mesh partitions & cages
8 Pages
-
Mezzanines
20 Pages
-
Cantilever Racking
24 Pages
-
Metal Point Boltless Shelving
24 Pages
-
Racking for Live Picking
36 Pages
-
M3 Shelving for picking
36 Pages
-
M7 Longspan shelving
31 Pages
-
Push-back pallet racking
12 Pages
-
Live Pallet Racking
28 Pages
-
Pallet Shuttle
36 Pages
-
Movirack Mobile Pallet Racking
20 Pages
-
Conventional Pallet Racking
44 Pages