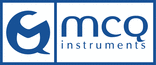

Catalog excerpts
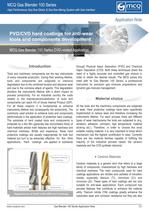
MCQ Gas Blender 100 Sries High Performance Gas flow Dilutor & Gas flow Mixing System with User Interface e mcQ instruments Application Note 9t PVD/CVD hard coatings for anti-wear \ tools and components development o -<mH--, MCQ Gas Blender 100 S闩ries CVD-related Application Introduction through Physical Vapor Deposition (PVD) and Chemical Vapor Deposition (CVD). Both these techniques share the need of a highly accurate and controlled gas mixture in order to obtain the desired results. The MCQ solves this need with its Gas Blender 100 Series, a professional instrument for precision gas mixtures preparations and dynamic gas mixtures management. Tools and machinery components are the key instruments of every industrial production. During their working lifetime, tools and components are subjected to intensive degradation due to the combined erosive and abrasive wear and due to the corrosive attack of agents. This degradation shortens the instruments lifetime with a direct impact on process productivity. For an industrial country the costs related to the maintenance/substitution of tools and components can reach 4% of Gross Internal Product (GIP). For all these reasons it is fundamental to enhance instruments lifetime and consequently the productivity. The commonly used solution to enhance tools and components performances is the application of protective hard coatings. The substrate of hard coated tools and components is protected by a thin film (generally few micrometers thick) of hard materials whose main features are high hardness and chemical inertness. Brittle and expensive, these hard protective coatings are usually inappropriate for bulk tool material but turn to be extremely effective for thin films applications. Hard coatings are applied to substares Material choice All the tools and the machinery components are subjected to wear. Hard protective coatings have been specifically implemented to reduce wear and therefore increasing the instruments lifetime. For each process there are different types of wear mechanisms the tools are subjected to (e.g. abrasion, adhesion, corrosion, high temperature, material sticking etc.). Therefore, in order to choose the most suitable coating material, it is very important to know which mechanism has the highest contribution to wear. Currently there are two material families capable of fulfilling the majority of the industrial process needs: the ceramic materials and the CVD synthetic diamond. c CVD Diamond Coating Ceramic Materials Ceramic materials is a generic term that refers to a large family of compounds, characterized by high hardness and chemical inertness. The main compounds used for hard coatings applications are nitrides and carbides of transition metals, especially titanium (Ti), chromium (Cr) and zirconium (Zr). These types of hard coatings are not only suitable for anti-wear applications. Each compound has peculiar features that contribute to enhance the material utility. Titanium nitride(TiN) coatingsgreatly enhance the substrateswear and corrosionresistancebut they are also Titanium Nitride Coating C Substrate Substrate Appearance of drills with diffթrent coating www.mcqinst.com Gas Blender 100 Series Application Note 1/3
Open the catalog to page 1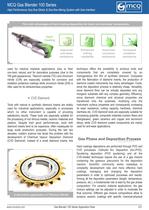
MCQ Gas Blender 100 Sries High Performance Gas flow Dilutor & Gas flow Mixing System with User Interface e mcQ instruments The main a avantages ofhard coating dposition fortools and anti-wear components. Hard Coating Enhanced cutting capability Improved corrosion resistance I Increased oxidation resistance Improved anti-wear r驩sistance used for mdical implants applications (due to their non-toxic nature) and for decorative purposes (due to the TiN gold appearance). Titanium carbide (TiC) and chromium nitride (CrN) are especially suitable for corrosion and oxidation protective coatings while...
Open the catalog to page 2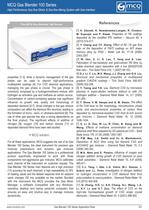
MCQ Gas Blender 100 Sries High Performance Gas flow Dilutor & Gas flow Mixing System with User Interface e mcQ instruments Rf驩rences [I] K. Zdunek, K. Nowakowska-Langier, R. Chodun, M. Kupczyk and P. Siwak, Properties of TiN coatings deposited by the modified IPD method - Vacuum 85, 4 (2010) 514-517. [2] Y. Cheng and Y.F. Zheng, Effect of N2 /Ar gas flow ratio on the deposition of TiN/Ti coatings on NiTi shape memory alloy by PIIID - Mater Lett 60, 17-18 (2006) 2243-2247. [3] W. Uen, Z. Li, S. Lan, T. Yang and S. Liao, Fabrication of low-resistivity and gold-colored TiN films by halide...
Open the catalog to page 3All MCQ Instruments catalogs and technical brochures
-
GB 15k
2 Pages
-
GB 4000
4 Pages
-
GB 2000
4 Pages
-
GB 3000
4 Pages
-
GB 6000
4 Pages
-
GB 100
4 Pages
-
GB 100 PLUS
4 Pages
-
Products Overview
2 Pages
-
MCQ Gas Blender 100 Series
7 Pages
-
Sensor module
7 Pages
Archived catalogs
-
Gas Blender 6000
4 Pages
-
Gas Blender 106 Series
4 Pages
-
Flow Monitor Software
2 Pages
-
flow board
4 Pages
-
data acquisition board
4 Pages