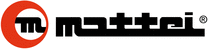

Catalog excerpts
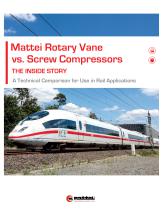
Mattei Rotary Vane vs. Screw Compressors THE INSIDE STORY A Technical Comparison for Use in Rail Applications
Open the catalog to page 1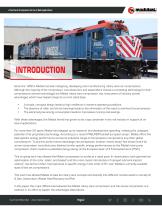
NN Since the 1950’s Mattei has been designing, developing and manufacturing rotary vane air compressors. Although the majority of the compressor manufacturers and assemblers choose a competing technology for their compressors, (screw technology), the Mattei rotary vane compressor has many years of industry proven advantages which have helped shape its current client base. • • • A simple, compact design leads to high resilience in extreme operating conditions. The absence of roller and thrust bearings leads to the elimination of the need to overhaul the compressor. The extremely low energy...
Open the catalog to page 2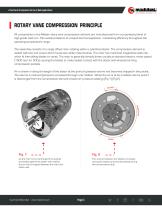
ROTARY VANE COMPRESSION PRINCIPLE All components in the Mattei rotary vane compression element are manufactured from a proprietary blend of high-grade cast iron. This avoids problems of unequal thermal expansion, maintaining efficiency throughout the operating temperature range. The assembly consists of a single offset rotor rotating within a cylindrical stator. The compression element is sealed with two end covers which house two white metal bushes. The rotor has machined longitudinal slots into which fit free sliding blades or vanes. The rotor is generally directly driven usually at...
Open the catalog to page 3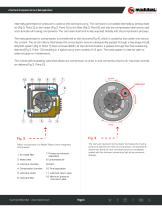
A Technical Comparison for Use in Rail Applications Internally generated air pressure is used as the lubricant pump. The lubricant is circulated internally by pressurised air [Fig 3, Point 3] to the cooler [Fig 3, Point 5], to the filter [Fig 3, Point 6] and into the compression element to seal and lubricate all moving components. The cool clean lubricant is also injected directly into the compression process. The heat generated in compression is transferred to the lubricant [Fig 4], which is cooled by the cooler and sent to the oil tank. The air-oil mixture that leaves the compression area...
Open the catalog to page 4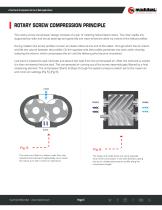
ROTARY SCREW COMPRESSION PRINCIPLE The rotary screw compressor design consists of a pair of meshing helical lobed rotors. The rotor shafts are supported by roller and thrust bearings and generally one rotor drives the other by means of the helical profiles. During rotation the screw profiles uncover an intake orifice at one end of the stator, through which the air enters and fills the volume between the profiles. On the opposite side the profiles penetrate into each other, thereby reducing the volume, which compresses the air until the delivery ports become uncovered. Lubricant is injected...
Open the catalog to page 5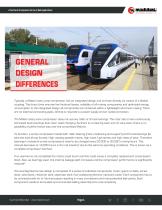
GENERAL DESIGN DIFFERENCES S Typically, a Mattei rotary vane compressor has an integrated design and is driven directly via means of a flexible coupling. The direct drive ensures low frictional losses, reliability of all moving components and optimised energy consumption. In the integrated design all components are contained within a lightweight aluminium casing. There are no external connecting pipes. All that is required is a power supply and air outlet connection. The Mattei rotary vane compressor does not use any roller or thrust bearings. The rotor sits on two continuously lubricated...
Open the catalog to page 6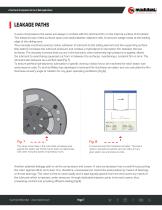
LEAKAGE PATHS In vane compressors the vanes are always in contact with the lubricant film on the internal surface of the stator. This keeps the two metal surfaces apart and seals between adjacent cells. A lubricant wedge exists at the leading edge of the sliding vane. The precisely machined vane tip radius, adhesion of lubricant to the sliding element and the supporting surface (the stator) increases the lubricant pressure and creates a hydrodynamic lubrication film between the two surfaces. The viscosity increase that occurs in the lubricant, when extremely high pressure is applied, allows...
Open the catalog to page 7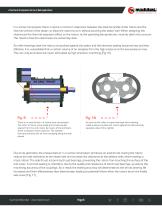
In a screw compressor there must be a minimum clearance between the external profile of the rotors and the internal surface of the stator, to allow the rotors to turn without touching the stator wall. When designing the clearances the thermal expansion effect on the rotors, at the operating temperatures, must be taken into account. The result is that the clearances are extremely close. As roller bearings wear the rotors are pushed against the stator and the lubricant sealing becomes less and less effective. It is unavoidable that a certain volume of air escapes from the high pressure to the...
Open the catalog to page 8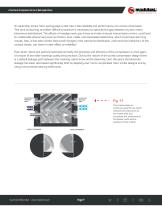
A Technical Comparison for Use in Rail Applications On assembly, screw rotor pairing plays a vital role in the reliability and performance of a screw compressor. This time consuming and often difficult procedure is necessary to optimise the gap between any two rotors (clearance distribution). The effects of misalignment, gas forces and rotor-induced transmission errors, could lead to undesirable phenomena such as friction, buzz, rattle, and associated distortions, which could have alarming results. Also, it has been shown that small changes in the clearance distribution, and hence the...
Open the catalog to page 9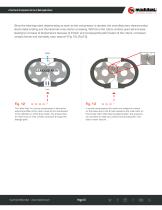
A Technical Comparison for Use in Rail Applications Since the bearings start deteriorating as soon as the compressor is started, the manufacturers clearance also starts deteriorating and the blow-hole area starts increasing. With time the rotors contact point will increase leading to increase of temperature because of friction and consequently deformation of the rotors, increased contact forces and ultimately rotor seizure8 [Fig 1 2], [Fig 13]. I I Fig. 12 -----' The “blow hole" in a screw compressor is where the external profiles of the rotors meet at the intersection of the cylinders in...
Open the catalog to page 10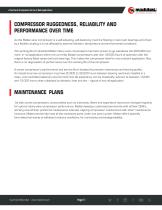
COMPRESSOR RUGGEDNESS, RELIABILITY AND PERFORMANCE OVER TIME As the Mattei vane compressor is a self-adjusting, self-balancing machine floating on two bush bearings and driven by a flexible coupling, it is not affected by external vibration, temperature and environmental conditions. The working life of industrial Mattei rotary vane compressors has been proven to go well above the 200,000 hour mark. In rail applications there are currently Mattei compressors with over 35,000 hours of operation with the original factory fitted vanes and bush bearings. This makes the compressor ideal for any...
Open the catalog to page 11All MATTEI catalogs and technical brochures
-
RVD 30÷55 i
8 Pages
-
RVD 30÷55
8 Pages
-
RVX Series
8 Pages
-
RVX 45-55-75 Ultra Performance
12 Pages
-
GAS APPLICATIONS
12 Pages
-
OEM
12 Pages
-
Classic series
6 Pages
-
ENERGY SAVING
24 Pages
-
AIR TREATMENT
20 Pages
-
AIR CENTRE SERIES
16 Pages
-
ERC
6 Pages
-
RAILWAY APPLICATIONS
12 Pages
-
AIR CENTRE 110 - 132 kW
6 Pages
-
HIGH-EFFICIENCY SERIES
8 Pages
-
Compressors
4 Pages
-
VARIABLE SPEED SERIES
8 Pages
-
RVXi 55-75-90 Series
12 Pages
-
CONTROL SYSTEMS
8 Pages
-
AIR CENTRE 30 - 45 kW
6 Pages
-
CONCERTO System
8 Pages
-
BLADE Series
8 Pages
-
BLADE 4 - 5 - 7 - 11
8 Pages
-
BLADE i 8 - 12
8 Pages
-
BLADE 15 - 18 - 22
8 Pages
-
BLADE i 15 - 18 - 22
8 Pages
-
BLADE 1-2-3
8 Pages
-
Blade 1-3
8 Pages
-
Air treatment
20 Pages
-
FM
6 Pages
-
Maxima series
8 Pages
-
Series MBL
8 Pages
-
AIR COMPRESSORS
16 Pages
-
CONDENSATE TREATMENT
2 Pages
-
OIL-WATER SEPARATORS
8 Pages
-
Blowers SERIES SM - SMR - SMT
16 Pages
Archived catalogs
-
CLASSIC SERIES
16 Pages
-
AC 55-75-9O
8 Pages