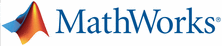
Catalog excerpts

Simulink Design Optimization Estimate and optimize Simulink model parameters Simulink Design Optimization™ lets you improve designs by estimating and tuning model parameters using numerical optimization. You can increase model accuracy by using test data to calibrate physical parameters, such as mass or resistance. You can then improve system performance, reduce system cost, and meet other objectives by automatically tuning design parameters in your Simulink® model. For example, you can use design optimization techniques to optimize controller gains to meet rise-time and overshoot constraints, or jointly optimize physical and algorithmic parameters to maximize overall system performance. Key Features ▪ Model parameter estimation from test data ▪ Simultaneous optimization of time-domain and frequency-domain responses of Simulink models (with Simulink Control Design™) ▪ Graphical specification of response requirements and visual monitoring of the optimization progress ▪ Optimization of parameters to meet requirements specified by Model Verification blocks ▪ Custom constraints and cost functions for response optimization ▪ Scripting interface for programmatic specification of design optimization problems ▪ Robust design optimization, accounting for parameter variation or uncertainty
Open the catalog to page 1
File Edit View Display Diagram Simulation Analysis Code Tools Help Pare m eter_Esti rnati on Idle Speed Engine Model Nonlinearities Linear Dynamics Engine Speed Q Sirnu"a1ed Measured Before Esf.imatfcn file Edit View hsert Toots Desktop Window HetD Si wulaleid and MeaiuiKj Respoime™ Caloie Estimation D Simulated *s. Measured After Estimation File Edil View Insert Tools Desktoo Window Help SimuUtetl and Measured Respurtses Alter Estimation Tima (seconds) Using Simulink Design Optimization with measured data for parameter estimation of Transfer Fen and Mean Speed blocks (top, red). You can...
Open the catalog to page 2
ft Data Preprocessing Tool (or Dataset: Engine 1A Modify data from ...tion/Engine Speed T Write results lo: Data Editing! existing dataset |Engine 1A w\ (0>) new dataset Datasetl Exclusion Rules Detrend/filiering FlrttMtiid Manually excluded Exdude Graphically Window length: Missing Data Handling ■1 Remove rows v;h D Select Poinrs for Pnepiocessirg Rule JUSing interpolation method ZOh * Man jallv eHduSeS '^^o^Exctuded by rule Dialog box for preprocessing data in Simulink Design Optimization to remove outliers and unwanted trends. You can exclude outliers and unwanted trends graphically...
Open the catalog to page 3
Use Value as Initial Guess Reset to Default Settings Save as Default Settings Configure your estimation here. Control and Estimation Tools Manager for configuring, manipulating, and running parameter estimations in Simulink Design Optimization. Parameters with check marks have been selected for estimation. Comparing and Validating Estimation Results Simulink Design Optimization can generate comparative plots of estimation results to help you determine which model parameter values result in the best model and measured data fit. Plots include views of parameter sensitivity, measured versus...
Open the catalog to page 4
Optimizing Time-Domain and Frequency-Domain Responses of Simulink Models With Simulink Design Optimization, you can tune Simulink model parameters to meet time-domain requirements, frequency-domain requirements, or both simultaneously. Using the Design Optimization tool in Simulink Design Optimization, you can add and edit design requirements graphically or by entering tabular data, and then run the optimization. The graphical tool also lets you monitor optimization progress. It shows plots for each requirement as well as the optimization status in a single view. As with parameter...
Open the catalog to page 5
File Edit View Display Diagram Simulation Analysis Code Toots Help Nonlinear model (top) for which parameters are optimized using the Design Optimization tool (bottom) to meet several time-domain objectives (orange box) simultaneously. Optimization minimizes the cross-sectional area (design variable AC), while satisfying constraints on pressure and piston position. Tuning Simulink Model Parameters to Meet Frequency-Domain Requirements For frequency-domain optimization, you can use Simulink Design Optimization with Simulink Control Design to linearize a Simulink model and use the resulting...
Open the catalog to page 6
Dupiiy Diagram Simuiaiion Anaiyvi Code Too if Help Recdfiec Rectifier Filer Frter Design Requirements T SJMULDNK Worfcsp »« (sdofl«tifi«f) T Design Optimiialion Workspace I sdoR«tifnrr/Fi Iter Oiion R«juircmmli ■ ] Simulink model with a rectifier filter (top, red block), for which parameters R (resistance), L (inductance), and C (capacitance) are optimized using the graphical tool (bottom) to meet frequency-domain requirements. Optimizing Time-Domain and Frequency-Domain Responses Simultaneously Simulink Design Optimization lets you manage tradeoffs among requirements, such as stability,...
Open the catalog to page 7
Library sdolib/Model Verification File Edit View Display Diagram Analysis Help Model Verifjcalion Check Custom Sound & Check Step Response Check gainst ReFerence *i Library sIclrlblks/Model Verification Fire Edit View Display Diagram Analyse Help Model Verification Check Pols-Zero Cnaraden iics ciwct Ncticts Check Sit aular Value Check Linear Slap Response CHecK Gaftarrd Phase Margns Model Verification block libraries in Simulink Design Optimization (top) and Simulink Control Design (bottom). Using Custom Constraints and Cost Functions Simulink Design Optimization lets you specify custom...
Open the catalog to page 8
Optimizing Suspension System Performance 6:41 Use custom objectives and frequency-domain optimization to optimize the ride quality of a suspension system. Programmatically Specifying Response Optimization Problems In addition to providing a graphical tool for setting up and solving parameter optimization problems, Simulink Design Optimization lets you formulate and solve optimization problems programmatically. Using this approach, ■ Specify the model parameters to be optimized ■ Specify the model signals to be logged from simulations ■ Specify standard objectives (such as step response...
Open the catalog to page 9All The MathWorks catalogs and technical brochures
-
MATLAB Production Server
6 Pages
-
Database Toolbox
4 Pages
-
MATLAB Report Generator
4 Pages
-
Stateflow
8 Pages
-
SimEvents
7 Pages
-
SimDriveline
7 Pages
-
SimHydraulics
7 Pages
-
SimPowerSystems
8 Pages
-
Simulink Control Design
5 Pages
-
Aerospace Blockset
5 Pages
-
SimRF
6 Pages
-
Simulink Coder
6 Pages
-
Embedded Coder
8 Pages
-
Simulink PLC Coder
4 Pages
-
Fixed-Point Designer
9 Pages
-
MATLAB Coder
5 Pages
-
Simulink 3D Animation
10 Pages
-
Gauges Blockset
2 Pages
-
Simulink Report Generator
3 Pages
-
Polyspace Bug Finder
6 Pages
-
global-optimization-toolbox
10 Pages
-
Phased Array System Toolbox
9 Pages
-
OPC Toolbox
5 Pages
-
Simulink Design Verifier
7 Pages
-
Filter Design HDL Coder
5 Pages
-
Bioinformatics Toolbox
9 Pages
-
SimBiology
6 Pages
-
Computer Vision System Toolbox
10 Pages
-
DSP System Toolbox
11 Pages
-
Fuzzy Logic Toolbox
5 Pages
-
Polyspace Client for C/C++
5 Pages
-
xPC Target
5 Pages
-
SimMechanics
7 Pages
-
Simscape
7 Pages
-
Simulink
6 Pages
-
Data Acquisition Toolbox
8 Pages
-
Image Processing Toolbox
7 Pages
-
Signal Processing Toolbox
10 Pages
-
Control System Toolbox
6 Pages
-
Symbolic Math Toolbox?
6 Pages
-
Parallel Computing Toolbox?
7 Pages
-
MATLAB®
6 Pages
-
Mapping Toolbox 3.2
7 Pages
-
Instrument Control Toolbox
7 Pages
-
Optimization Toolbox 6.0
14 Pages
Archived catalogs
-
MATLAB Release Notes
505 Pages
-
C and Fortran API Reference
263 Pages
-
External Interfaces
649 Pages
-
Function Reference: Volume 3 (P-Z)
1696 Pages
-
Function Reference: Volume 2 (F-O)
1568 Pages
-
Function Reference: Volume 1 (A-E)
1298 Pages
-
Creating Graphical User Interfaces
520 Pages
-
3-D Visualization
212 Pages
-
Graphics
667 Pages
-
MATLAB Programming Tips
66 Pages
-
Programming Fundamentals
840 Pages
-
Data Analysis
220 Pages
-
Mathematics
316 Pages
-
MATLAB® Getting Started Guide
250 Pages