Catalog excerpts
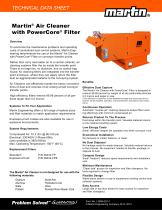
TECHNICAL DATA SHEET Martin® Air Cleaner with PowerCore® Filter Overview To overcome the maintenance problems and operating costs of centralized dust control systems, Martin Engineering recommends the use of the Martin® Air Cleaner with PowerCore® Filter on conveyor transfer points. Rather than carry dust-laden air to a central collector, air cleaning systems filter the air inside the transfer point. There is no large fan, no ductwork, and no central bag house. Air cleaning filters are integrated into the transfer point enclosure, where they can easily return the filter dust as agglomerated material to the conveying system. Air Cleaners can effectively handle the heavy concentrations of dust and volumes of air arising at belt conveyor transfer points. High efficiency filters remove 99.99 percent of all particles larger than 0.5 micron. Systems To Fit Your Application Martin Engineering offers a full range of system sizes and filter materials to match application requirements. Explosion-proof models are also available for use in explosive environments. Benefits Effective Dust Capture The Martin® Air Cleaner with PowerCore® Filter is designed to remove 99.99 percent by weight of all dry particulate particles 0.5 micron and larger in size. (This efficiency is based on a time-weighted average and assurances the air cleaner will be installed, operated, and maintained in accordance with instructions.) Continuous Operation Automatic “reverse jet” cleaning sequence keeps filters working effectively with minimum compressed air. Returns Product To The Process Dust stays within the transfer point. Valuable material returns to the material handling system. System Requirements Compressed Air: 10.2 cfm @ 90-100 psi Electrical: 230/460V 3-Phase 60Hz (also available in 380V/50Hz) Max. Operating Temperature: 150°F (66°C) Economical Installation Small, efficient integral fan operates only when conveyor runs. Replacement Filters Standard: Explosion-Proof: No ductwork to install, balance, or clean. No haulage costs for waste disposal. Valuable material returns to the process. No equipment needed to handle, package, or dispose of dust. Compact Design Small “footprint” reduces space requirements and installation cost. Minimum Maintenance The Martin Air Cleaner is not designed for use with the following materials: ® Gypsum Alumina Salts Potash Soda Ash Hydrated Lime Urea Powder River Basin Coal “Clean side” access for inspection and filter changeout. No tools required to change filter. Flexible Design Stand-alone system or use to supplement existing central dust collector systems. Easy Access Large side or top door allows for easy access for inspection and filter changeout. Form No. L3906-02/14 © Martin Engineering Company 2012, 2014
Open the catalog to page 1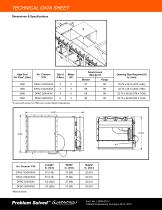
TECHNICAL DATA SHEET Dimensions & Specifications Opening Size Required (A) in. (mm) *If using with cement or PRB coal, contact Martin Engineering. *Without blower Form No. L8888-88/11 L3906-02/14 Form No. © Martin Engineering Company 1944, 2011 2012, 2014 © Martin Engineering Company
Open the catalog to page 2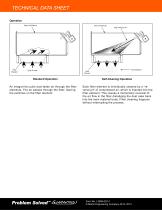
TECHNICAL DATA SHEET Operation Clean Air Plenum Clean Air Plenum High Pressure Air Filter Element Standard Operation An integral fan pulls dust-laden air through the filter elements. The air passes through the filter, leaving the particles on the filter element. Filter Element Dust Disposal Self-Cleaning Operation Each filter element is individually cleaned by a “reverse jet” of compressed air, which is injected into the filter element. This causes a momentary reversal of the air flow in the filter dislodging the dust cake back into the main material body. Filter cleaning happens without...
Open the catalog to page 3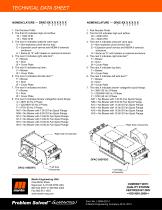
TECHNICAL DATA SHEET NOMENCLATURE — DFAC-XX X X X X X X 1. Part Number Prefix 2. The first XX indicates high end airflow: 10 = 1000 CFM 15 = 1500 CFM 3. The next X indicates solenoid valve type: S = Non-explosion proof service duty E = Explosion proof service and NEMA 9 solenoid enclosure H = Same as “E” with heaters in solenoid enclosure 4. The next X indicates right side item*: F = Blower D = Door Ø = Cover Plate 5. The next X indicates top item: F = Blower Ø = Cover Plate 6. The next X indicates left side item**: F = Blower D = Door Ø = Cover Plate 7. The next X indicates end item: F =...
Open the catalog to page 4All Martin Engineering catalogs and technical brochures
-
Cougar® Ring Vibrators
2 Pages
-
Martin® Return Reservoir
1 Pages
-
Martin® Removable Nozzle
1 Pages
-
Martin® QC1? Cleaner HD Max
2 Pages
-
Martin® Sonic Horns - 230Hz
2 Pages
-
Martin® Return Roller Basket
1 Pages
-
Martin® Return Roller Guard
1 Pages
-
Martin® Retractable Nozzle
2 Pages
-
EVO® Combination Cradle
2 Pages
-
Martin® Inspection Door HD
2 Pages
-
MARTIN® DUST BAGS
26 Pages
-
Hydraulic Screen Vibrator
2 Pages
-
MARTIN® MP3 Railcar Vibrator
18 Pages
-
MARTIN® Brush Cleaners
28 Pages
-
HAWG BONE® Secondary Cleaner
26 Pages
-
MARTIN® SHD Belt Cleaner
38 Pages