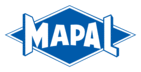
Catalog excerpts
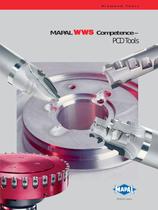
Diamond Tools MAPAL WWS Competence – PCD Tools A Review of MAPAL’s Competence Reaming and Fine Boring From the wide range of single and twin-bladed reamers with guide pads, together with fine boring tools with guide pads and WP or HX blades, to the HPR High Performance Reamers combined with the MAPAL HFS® Head Fitting System for exact concentricity and accurate changeover – to give you a general view of our complete knowledge and experience in precision machining bores. PCD Tools For pre-machining and finish machining, MAPAL also offers an extensive programme of precision tools with fixed PCD (polycrystalline diamond) blades. This includes precision gun boring tools plus circular and end milling tools. The programme of face milling heads from the PowerMill and EcoMill series is characterised by simple, sturdy design and rapid, accurate blade setting. ISO Tools This aspect of MAPAL competence is made up of special tools with ISO elements for gun boring and milling. This includes precision ground blades in the widest variety of cutting materials and coatings. The use of MAPAL's tried and tested adjustment system ensures that the blades are accurately matched to the task. MAPAL offers particular knowledge and experience in tangential technology. Drilling Yet another area is the product programme for drilling. MAPAL offers the right tool concept for every task, whether for machining aluminium, steel or cast iron, hard machining or dry machining or for use in HSC areas. Specially developed coatings and PCD blades complete the broad-based drilling programme. Clamping Systems MAPAL's modern clamping systems, in conjunction with MAPAL's tried and tested reaming and fine boring tools, guarantee maximum productivity and economy. Whether HSK, ISO or HFS®, these high-precision connections and interfaces provide the concentricity and changeover accuracy essential to modern production. Customer Services Project planning, maintenance, management and optimisation – the complete CTS® service package from MAPAL will accompany you from process design to permanent process optimisation and will ensure optimum and cost-saving use of your tools with the best possible results. PKD-E-01/10-020-0807-WD Printed in Germany/Right of technical modifications reserved. Generating Slide Tools Generating slide tools offer a high potential for rationalisation and optimisation on special machines and machining centres. In addition to the conventional facing heads, MAPAL also supplies EAT and LAT performance-enhanced actuating systems for generating slide tools. MAPAL TOOLTRONIC® tools with their extraordinary range of functions are the latest development. MAPAL MAPAL Präzisionswerkzeuge Dr. Kress KG MAPAL WWS Werner Stief GmbH
Open the catalog to page 1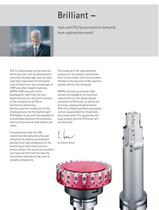
Brilliant – tools with PCD (polycrystalline diamond) have captured the world! In combination with the HSK connection the manufacturing and utilisation of rotating tools became possible with high complexity for the machining of aluminium and nonferrous metals. The results are excellent tool lives and with that the basis for the rational manufacturing, even of complex components. The handling of the tools generally produced in monoblock construction form is very simple. Care must be taken thereby of the precision of the machine spindle and the tool clamping. MAPAL has built up a world-wide...
Open the catalog to page 2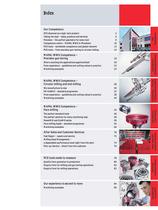
Who’s counting the applications opportunities? From experience – guidelines and cutting values in practice Machining examples MAPAL WWS Competence – Circular milling and end milling We manufacture to size HP-EndMill – standard programme From experience – guidelines and cutting values in practice Machining examples MAPAL WWS Competence – Face milling The perfect standard tools The perfect solution for every machining task PowerMill and EcoMill series Face milling heads – standard programme Machining examples PCD tools made to measure Quality from quotation to production Enquiry form for...
Open the catalog to page 3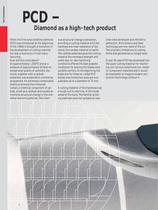
Diamond as a high-tech product When the first polycristalline diamond (PCD) was introduced at the beginning of the 1980s it brought a revolution in the development of cutting material but also a revolution in tool manufacturing. How did this come about? At approximately 1,500°C and at a pressure of approximately 60 kbar an exceptional quality of synthetic diamond, together with a carbide substrate, was subjected to a sintering programme. An extremely complicated chemical process then followed. Cobalt, a chemical component of carbide, acted as a catalyst and caused an intensive structural...
Open the catalog to page 4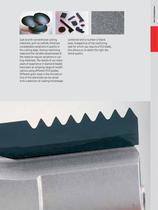
Just as with conventional cutting materials, such as carbide, there are considerable variations in quality in the cutting edge. Various machining tasks and the variable abrasiveness of the material require variations in cutting materials. The results of our many years of experience in diamond blades have been an amazing range of modifications using different PCD grades. Different grain sizes in the microstructure of the diamonds can be varied with a selection of coating thicknesses combined with a number of blank sizes. Irrespective of the machining task for which you require a PCD blade,...
Open the catalog to page 5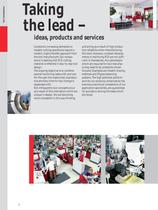
Taking the lead – ideas, products and services Constantly increasing demands on modern cutting operations require a modern, highly flexible approach from the tool manufacturer. Our competence in dealing with PCD cutting material is reflected in day-to-day tool design. The ongoing objective is to combine several machining tasks with one tool. For the user this means that unproductive ancillary time for tool change is dispensed with. Not infrequently tool concepts occur as a result of this motivation which are unique in design. We are becoming more competent in this way thinking and acting as...
Open the catalog to page 6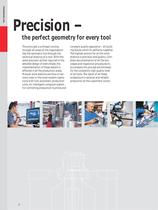
Precision – the perfect geometry for every tool This principle is a thread running through all areas of the organisation like the symmetry line through the technical drawing of a tool. With the same precision as that required in the detailed design of every blade, the implementation of these details is effected in all the production areas. Manual work stations are thus in harmony even in the most modern operations with fully automatic production units. An intelligent computer system for controlling production routines and constant quality assurance – all building blocks which fit perfectly...
Open the catalog to page 8All MAPAL catalogs and technical brochures
-
MAPAL Innovations 2021
28 Pages
-
Countersinks
2 Pages
-
Insert drill QTD
24 Pages
-
MAPAL TOOLTRONIC®-S
4 Pages
-
MAPAL Competence Clamping technology
464 Pages
-
UNIBASE-M
2 Pages
-
QTD insert drill
24 Pages
-
MAPAL UNISET-P
4 Pages
-
Innovations 2014
20 Pages
-
MAPAL EasyAdjust-System
12 Pages
-
MAPAL VersaCut
16 Pages
-
MAPAL TOOLTRONIC®
16 Pages
-
MAPAL Competence Actuating Tools
36 Pages
-
MAPAL Competence Solid carbide tools
266 Pages
Archived catalogs
-
MAPAL Actuating Tools
36 Pages
-
MAPAL Competence ISO Tools
72 Pages
-
MAPAL Competence drilling
166 Pages
-
News broschure
32 Pages
-
MAPAL News
32 Pages