
Catalog excerpts
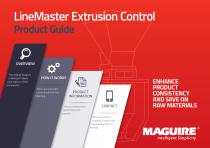
OVERVIEW The modular design of LineMaster™ allows easy selection of the components... HOW IT WORKS Start-up in automatic control mode from the beginning. PRODUCT INFORMATION View our full technical specification and payback. CONTACT ENHANCE PRODUCT CONSISTENCY AND SAVE ON RAW MATERIALS Find out your local contacts or where your regional head office is located. Intelligent Simplicity
Open the catalog to page 1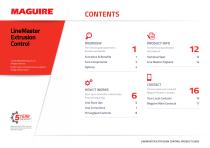
CONTENTS LineMaster Extrusion Control © 2016 MAGUIRE Products, Inc. All rights reserved. All information in this document is subject to change without notice. OVERVIEW The most popular gravimetric blenders worldwide. Functions & Benefits Core Components Options PRODUCT INFO Full technical specification and payback. Line Master Payback 14 o° HOW IT WORKS Start-up in automatic control mode from the beginning. Line Start Ups Line Corrections Throughput Controls □ CONTACT Find out where your nearest Maguire Partner is located. Your Local Contacts 16 Maguire Main Contacts 17 Maguire...
Open the catalog to page 2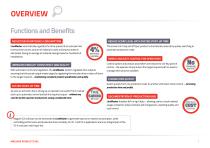
OVERVIEW Functions and Benefits REDUCTION IN MATERIALS CONSUMPTION LineMaster automatically regulates the drive speeds of an extrusion line to ensure the correct amount of material is used, and excess waste is eliminated. Giving an average 4% material savings based on hundreds of installations. REDUCE SCRAP LEVEL WITH FASTER START-UP TIME MATERIAL SAVINGS IMPROVED PRODUCT CONSISTENCY AND QUALITY With automatic control and regulation, the LineMaster system regulates drive outputs ensuring that the actual output meets target by regulating the extruder drive or take-off drive to the target...
Open the catalog to page 3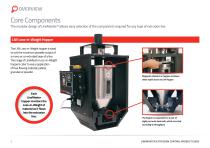
Core Components The modular design of LineMaster™ allows easy selection of the components required for any type of extrusion line. LIW Loss-in-Weight Hopper The LIW Loss-in-Weight hopper is sized to suit the maximum possible output of a mono or co‑extruded layer of a line. The range of LineMaster Loss-in-Weight hoppers cater to every application of free flowing material, pellets, granules or powder. Magnetic retainers on hopper enclosure allow rapid access to LIW Hopper. Each LineMaster hopper monitors the Loss‑in‑Weight of material as it flows into the extrusion line. The hopper is...
Open the catalog to page 4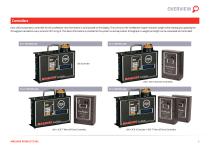
OVERVIEW Controllers Each LIW incorporates a controller for the LineMaster. Key information is summarized on the display. The control on the LineMaster hopper monitors weight while reading and updating the throughput calculation every second in lb/h or kg/h. This basic information is provided to the system so actual product throughput or weight per length can be calculated and controlled. LIW + XCD-X Extruder Controllers XC-2T CONTROLLER LIW + XCD-T Take-off Drive Controllers LIW + XCD-X Extruder + XCD-T Take-off Drive Controllers
Open the catalog to page 5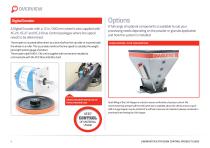
Digital Encoder A Digital Encoder with a 12 in./300 mm wheel is also supplied with XC‑2X, XC‑2T and XC‑3 Drive Control packages where line speed needs to be determined. The encoder is mounted either direct to a drive shaft on the nip roller or mounted with the wheel on a roller. This accurately monitors the line speed to calculate the weight per length and/or gauge of product. The encoder cable (100 ft./30.4m) is supplied with connectors installed to communicate with the XCD Drive Interface Card. DIGITAL ENCODER INSTALLED ON PIPE EXTRUSION LINE. A full range of optional components is...
Open the catalog to page 6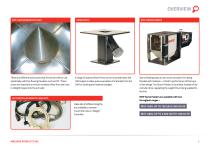
OVERVIEW FMC FLOW MODERATOR CONES These are different sized cones that fit into the LIW for use specifically with free flowing Powders such as PVC. These cones are important to ensure consistent flow from the Lossin-Weight hopper into the extruder. DRAIN PORTS A range of optional Drain Ports can be mounted below the LIW hopper to allow quick evacuation of materials from the LIW for cleaning and material changes. Starve feeding stops a twin screw extruder from being flooded with material – critical to performance of this type of line design. The Starve Feeder is controlled, instead of the...
Open the catalog to page 7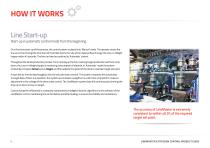
HOW IT WORKS Line Start-up Start-up in automatic control mode from the beginning. On a first time start-up of the process, the control system is placed into ‘Manual’ mode. The operator starts the line as normal. During this time the LIW Controller learns the rate of the material flow through the Loss-in-Weight hopper within 45 seconds. The line can then be switched to ‘Automatic’ control. Throughout the whole production process, from ramping up the line, reaching target production and then ramp down, the Loss‑in‑Weight hopper is monitoring consumption of material. In ‘Automatic’ mode the...
Open the catalog to page 8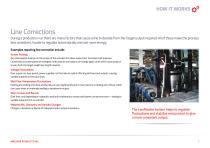
Line Corrections During a production run there are many factors that cause a line to deviate from the Target output required. All of these make the process less consistent, harder to regulate automatically and use more energy. Examples requiring line correction include: Screen Packing As contaminates build up on the screen of the extruder this slows output and increases melt pressure. Conversely, as screen packs are changed, melt pressure and output can change again, all of which cause product to vary from the target weight per length required. Voltage Fluctuations Over a given 24-hour...
Open the catalog to page 9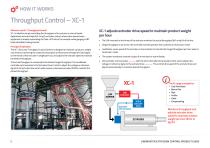
Where to use XC-1 Throughput Control? XC-1 is ideal for simply controlling the throughput of an extruder or starve feeder. Applications include simple lb/h or kg/h extruder control, where other downstream equipment is already automating the Take-off Control, for example online gauging or IBC (Internal Bubble Cooling) control. Principal of Operation The XC-1 Extrusion Throughput Control System is designed to maintain a product's weight over time by monitoring the material consumption of the process through the LIW hopper on the throat of the extruder in weight per hour, and adjusts the...
Open the catalog to page 10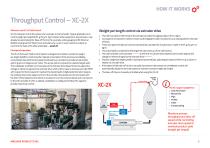
Throughput Control – XC-2X Where to use XC-2X Yield Control XC-2X is ideal to control the output of an extruder or starve feeder. Typical application is to control weight per length (lb/ft, g/ft, g/m, kg/m) where other equipment, downstream, may already be automating the Take-off Control, for example, online gauging or IBC (Internal Bubble Cooling) control. Most mono extruders are run at, or near maximum output so control of the take-off is often preferable – see XC-2T. Principal of Operation The XC-2X Extrusion Yield Control System is designed to maintain a product’s weight per length...
Open the catalog to page 11All Maguire Products Inc. catalogs and technical brochures
-
Sweeper Evacuation System
8 Pages
-
MGF-ST Series
8 Pages
-
Purging Recovery System
8 Pages
-
MS4 PeriStep Pump
4 Pages
-
MCF Concentrate Auger Feeder
28 Pages
-
GVL Self-Contained Motor Loader
11 Pages
-
MPL / ML Venturi Loaders
23 Pages
-
Model MLS - Clear VU
32 Pages
-
VBD 1000 Series Dryers
47 Pages
-
LPD 1000 Series Dryers
91 Pages
-
WSB 1860
2 Pages
-
WSB 1850
2 Pages
-
WSB 1840
2 Pages
-
WSB 960
2 Pages
-
WSB 950
2 Pages
-
WSB 940
2 Pages
-
WSB 460
2 Pages
-
WSB 440R
2 Pages
-
WSB 440
2 Pages
-
WSB 420
2 Pages
-
WSB 260
2 Pages
-
WSB 240R
2 Pages
-
WSB 240
2 Pages
-
WSB 220
2 Pages
-
WSB 160
2 Pages
-
WSB 140R
2 Pages
-
WSB 140
2 Pages
-
MicroPlus
2 Pages
-
MicroBlender?
2 Pages