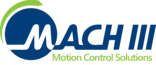
Catalog excerpts
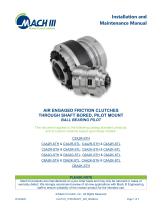
Installation and Maintenance Manual AIR ENGAGED FRICTION CLUTCHES THROUGH SHAFT BORED, PILOT MOUNT BALL BEARING PILOT This document applies to the following catalog standard products, and to custom versions based upon these models: C2A2R-STH C3A2R-STH & C3A2R-STL, C4A2R-STH & C4A2R-STL C5A2R-STH & C5A2R-STL, C5A2K-STH & C5A2K-STL C6A2G-STH & C6A2G-STL, C6A2K-STH & C6A2K-STL C8A2K-STH & C8A2K-STL, CAA2K-STH & CAA2K-STL CBA2K-STH PLEASE NOTE Mach III products are manufactured on a per order basis and may only be returned in cases of warranty defect. We strongly recommend review of all new applications with Mach III Engineering staff to ensure suitability of the chosen product for the intended use. © Mach III Clutch, Inc. All Rights Reserved 6/18/2020
Open the catalog to page 1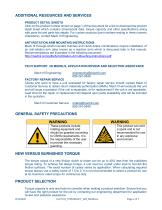
ADDITIONAL RESOURCES AND SERVICES PRODUCT DETAIL SHEETS Click on the product number shown on page 1 of this document for a link to download the product detail sheet which contains dimensional data, torque capacity and other specifications along with parts list and parts kits details. For custom products (part numbers ending in three numeric characters), contact Mach III Engineering. ANTI-ROTATION ARM MOUNTING INSTRUCTIONS Mach III through-shaft mounted clutches and clutch-brake combinations require installation of an anti-rotation arm (also known as a reaction arm) which is discussed later...
Open the catalog to page 2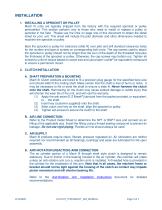
INSTALLATION 1. INSTALLING A SPROCKET OR PULLEY Mach III units are typically shipped from the factory with the required sprocket or pulley preinstalled. This section pertains only to those who need to install or replace a pulley or sprocket in the field. Please use the links on page one of this document to obtain the detail sheet for your unit. This sheet will include the pilot diameter and other dimensions needed to machine the sprocket or pulley. Bore the sprocket or pulley for clearance (slide fit) over pilot and drill standard clearance holes for the number and type of screws on...
Open the catalog to page 3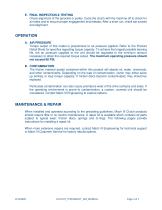
E. FINAL INSPECTION & TESTING Check alignment of the sprocket or pulley. Cycle the clutch with the machine off to check for air leaks and to ensure proper engagement and release. After a short run, check set screws and alignment. OPERATION A. AIR PRESSURE Torque output of this model is proportional to air pressure applied. Refer to the Product Detail Sheet for specifics regarding torque capacity. To achieve the longest possible bearing life, the air pressure supplied to the unit should be regulated to the minimum amount necessary to attain the required torque output. The maximum operating...
Open the catalog to page 4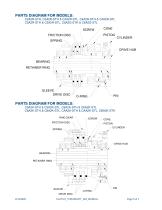
CONE PISTON FRICTION DISC BEARING RETAINER RING SLEEVE DRIVE DISC FRICTION DISC CONE PISTON CYLINDER BEARING RETAINER RING
Open the catalog to page 5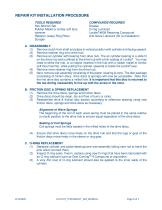
REPAIR KIT INSTALLATION PROCEDURE TOOLS REQUIRED Hex Wrench Set Rubber Mallet or similar soft face hammer Retainer (snap) Ring Pliers Scraper COMPOUNDS REQUIRED Grease O-ring Lubricant Loctite® #609 Retaining Compound Anti-Seize Lubricant (for re-installation) A. DISASSEMBLY (1) Remove clutch from shaft and place in vertical position with cylinder end facing upward. (2) Remove retainer ring from drive hub. (3) Remove air cylinder with bearing from drive hub. The air cylinder bearing is a slide fit on the drive hub and is affixed to the drive hub with a thin coating of Loctite®. You may need...
Open the catalog to page 6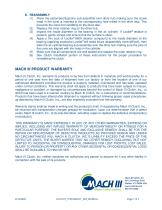
D. REASSEMBLY (1) Place the piston/bearing/cone sub-assembly over drive hub making sure the screw head in the cone is inserted in the corresponding hole milled in the drive disc. This prevents the cone from skidding on the drive disc. (2) Replace the inner retainer ring on the drive hub. (3) Inspect the inside diameter of the bearing in the air cylinder. If Loctite® residue is present, gently scrape and ensure that the surface is clean. (4) Apply a thin coat of Loctite® #609 retainer compound to the inside diameter of the bearing (applying excessive Loctite® will make future disassembly...
Open the catalog to page 7