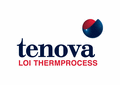
Catalog excerpts
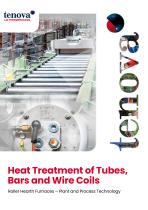
Heat Treatment of Tubes, Bars and Wire Coils Roller Hearth Furnaces – Plant and Process Technology
Open the catalog to page 1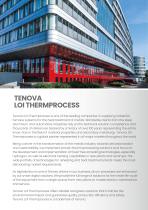
TENOVA LOI THERMPROCESS Tenova LOI Thermprocess is one of the leading companies in supplying industrial furnace systems for the heat treatment of metals. Worldwide clients from the steel, aluminium and automotive industries rely on the technical solution competence and thousands of references backed by a history of over 100 years representing the entire know-how in the field of material properties and secondary metallurgy. Tenova LOI Thermprocess is a global partner represented in all major markets throughout the world. Being a driver in the transformation of the metals industry towards...
Open the catalog to page 2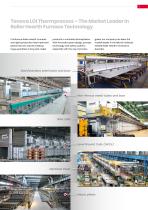
Tenova LOI Thermprocess – The Market Leader in Roller Hearth Furnace Technology Continuous Roller Hearth Furnaces products in controlled atmospheres. gases, our company has been the plants that are used for treating technology and safety systems, heated Roller Hearth Furnaces for are highly productive heat treatment large quantities of long and coiled With innovative plant design, process especially with the use of process market leader in the field of indirectly decades. Steel/stainless steel tubes and bars Non-ferrous metal tubes and bars Wire coils Level Wound Coils (LWCs) Electrical...
Open the catalog to page 3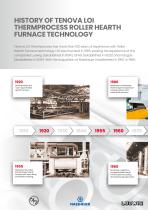
HISTORY OF TENOVA LOI THERMPROCESS ROLLER HEARTH FURNACE TECHNOLOGY Tenova LOI Thermprocess has more than 100 years of experience with Roller Hearth Furnace technology. LOI was founded in 1965, pooling the experience of the companies Ludwig (established in 1934), OFAG (established in 1920) and Indugas (established in 1928). With the acquisition of Nassheuer (established in 1910) in 1986, OFAG develops the “new” type of Roller Hearth Furnace. Nassheuer launches the first Roller Hearth Furnace with open firing and indirect heating. Nassheuer LOI develops the first high-temperature cooling...
Open the catalog to page 4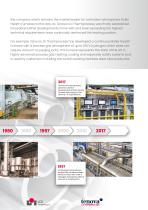
the company which remains the market leader for controlled-atmosphere Roller Hearth Furnaces to this day, as Tenova LOI Thermprocess, was finally established. Innovative further developments in line with and even exceeding the highest technical requirements have continually reinforced this leading position. For example, Tenova LOI Thermprocess has developed a continuous Roller Hearth Furnace with a process gas atmosphere of up to 100 % hydrogen which does not require vacuum or purging locks. This furnace represents the state of the art in highly advanced process gas, heating, cooling and...
Open the catalog to page 5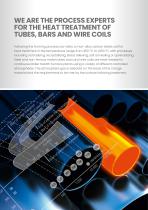
WE ARE THE PROCESS EXPERTS FOR THE HEAT TREATMENT OF TUBES, BARS AND WIRE COILS Following the forming process, low-alloy or non-alloy carbon steels call for heat treatment in the temperature range from 450 °C to 1,050 °C, with processes including normalizing, recrystallizing, stress relieving, soft annealing or spheroidizing. Steel and non-ferrous metal tubes, bars and wire coils are heat-treated in continuous Roller Hearth Furnace plants using a variety of different controlled atmospheres. The atmosphere gas is selected on the basis of the charge material and the requirements to be met by...
Open the catalog to page 6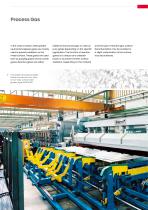
In the case of carbon steel grades, added to the process gas or used as and the type of reactive gas, surface used to prevent oxidation on the application. The function of reactive a slight carburization of the surface neutral atmosphere gases are mainly metal surface. These gases are used both as purging gases and as carrier gases. Reactive gases are either Controlled-atmosphere Roller Hearth Furnace for non-alloy or low-alloy carbon steel grades, type RoDR 6500 pure gases depending on the specific gases is to reduce any oxidation layers or to prevent further surface oxidation. Depending...
Open the catalog to page 7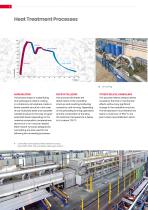
Heat Treatment Processes Slow cooling Final cooling STRESS RELIEVE ANNEALING and subsequent radiant cooling caused by thermal or mechanical The process steps of austenitizing in a stationary atmosphere create a ferrite-pearlite structure in the case of sub-eutectoid steels and a pearlite- carbide structure in the case of supereutectoid steels. Depending on the material composition, temperatures above Ac3 or Ac1 may be needed. This process eliminates the structure and resulting hardening caused by cold forming. Depending on the preceding forming operations and the composition of the alloy,...
Open the catalog to page 8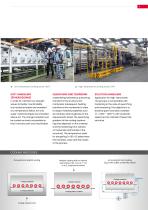
Low-temperature cooling section (NT) High-temperature cooling section (HT) SOFT ANNEALING (SPHEROIDIZING) SOLUTION ANNEALING values for better machinability, transforms the structure into martensite. Subsequent heating The process is comparable with In order to maintain low strength sub-eutectoid steels are annealed at a temperature below Ac1 and super-eutectoid steels are annealed above Ac1. The charge material must be cooled as slowly as possible so that it remains soft and machinable. Austenitizing followed by quenching transforms the martensite in order to adapt material properties...
Open the catalog to page 9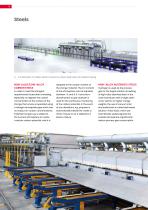
3-D illustration of a Roller Hearth Furnace for carbon steel tubes with radiant cooling NON-ALLOY/LOW-ALLOY CARBON STEELS adapted to the carbon content of HIGH-ALLOY AUSTENITIC STEELS requirements faced after annealing, of the atmosphere can be adjusted between 1 % and 6 %. A zirconium gas for the bright solution annealing In order to meet the stringent especially as regards the carbon charge, the furnace is operated using a nitrogen atmosphere gas which has no impact on carbon concentrations. Endothermal gas e.g. is added to the furnace atmosphere to create a certain carbon potential,...
Open the catalog to page 10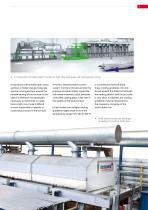
3-D illustration of a Roller Hearth Furnace for high-alloy steel tubes with hydrogen jet cooling For products with smaller open cross A PC/PLC-based process control In a continuous furnace plant, special moving curtains ensure the process and plant safety. Especially be achieved if the distance between sections or flatter charge materials, reliable sealing of the furnace. In this case it is therefore not absolutely necessary to install inlet or outlet locks which may make it difficult or even impossible to operate a continuous process in the furnace. system monitors and documents the with...
Open the catalog to page 11All LOI Thermprocess - Tenova Metals Division catalogs and technical brochures
-
HEAT TREATMENT LINES 2019
20 Pages
-
Aluminium Thermal Processes
32 Pages
-
Heat Treatment Lines 2023
20 Pages