
Catalog excerpts
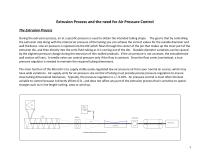
Extrusion Process and the need for Air Pressure Control The Extrusion Process During the extrusion process, air at a specific pressure is used to obtain the intended tubing shape. The goal is that by controlling the extrusion rate along with the internal air pressure of the tubing you can achieve the correct values for the outside diameter and wall thickness. Low air pressure is injected into the DIE which flows through the center of the pin that makes up the inner part of the extrusion die, and then directly into the semi-fluid tubing as it is coming out of the die. Sizeable diameter variations can be caused by the slightest pressure change during the extrusion of thin-walled products. If the air pressure is not constant, the extruded tube wall section will vary. A needle valve can control pressure only if the flow is constant. Since the flow varies (see below), a true pressure regulator is needed to maintain the required tubing dimensions. The main function of the MicroAir is to supply stable easily-regulated low air pressure air from your normal air source, which may have wide variations. Air-supply units for air-pressure size control of tubing must provide precise pressure regulation to ensure close tubing dimensional tolerances. Typically, the pressure regulation is +/- 0.01%. Air pressure control is most often the best variable to control because it directly affects O.D., and does not affect any part of the extrusion process that is sensitive to speed changes such as in line length-cutting, saws or wind-up. Dryer MicroAir Air Pressure Regulator Extruder Melt Pump Diameter Gauge DIE Cutter or winder Cooling Tank A Typical medical tubing extrusion line
Open the catalog to page 1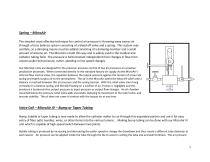
Spring – MicroAir The simplest most effective technique for control air pressure is throwing away excess air through a force balance system consisting of a bleed off valve and a spring. This system may oscillate, so a damping means must be added consisting of a damping member and a small amount of silicone oil. The MicroAir is built this way and is widely used in the medical and catheter tubing field. The pressure is held constant independent from changes in flow from uneven puller belt pressure, cutter, spooling or line speed changes. Our MicroAir units are designed for the precision...
Open the catalog to page 2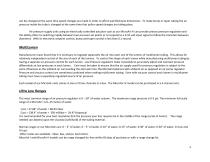
can be changed at the same time speed changes are made in order to affect wall thickness dimensions. To make bump or taper tubing the air pressure inside the tube is changed at the same time that puller-speed changes are taking place. Air pressure supply units using an electrically controlled actuator such as our MicroAir IV can provide precise pressure regulation and the ability either to switching rapidly between two pressure set points or to respond to a 0-10 volt input signal to follow the transition between diameters. With its electronic setpoint control, bump and taper control is less...
Open the catalog to page 3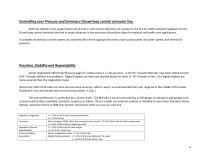
With the addition of an output option (0-10 volt or 4-20 ma) the MicroAir can connect to the PLC for 100% complete feedback control. Closed-loop control methods have led to major advances in the extrusion of precision tubes for medical and health-care applications. A complete closed loop control system can automatically set the appropriate screw or gear pump speed, the puller speed, and internal air pressure. Precision, Stability and Repeatability Dwyer magnehelic differential Pressure gage (4") meters have a +/-2% accuracy. A 0-0.25" of water MicroAir I has been tested to hold 0.05" of...
Open the catalog to page 4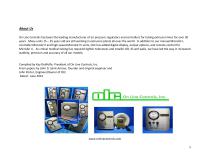
About Us On Line Controls has been the leading manufacturer of air pressure regulators and controllers for tubing extrusion lines for over 30 years. Many units 15 – 25 years old are still working in extrusion plants all over the world. In addition to our manual MicroAir I, controller MicroAir II and high-speed MicroAir IV units, OLC has added digital display, output options, and remote control for MicroAir II. As critical medical tubing has required tighter tolerances and smaller OD, ID and walls, we have led the way in increased stability, precision and accuracy of all our models. Compiled...
Open the catalog to page 5All On Line Controls catalogs and technical brochures
-
Micro Air
2 Pages
-
DC Motorpot 2020
2 Pages
-
AC Motor 2020
2 Pages
-
Motorized Rheostats
1 Pages
-
MicroAir Statistics
2 Pages
-
Motorized Potentiometer AC
2 Pages
-
Motorized Potentiometer DC
2 Pages
-
Dials
1 Pages