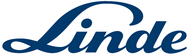

Catalog excerpts
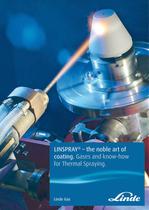
LINSPRAY® – the noble art of coating. Gases and know-how for Thermal Spraying. Linde Gas
Open the catalog to page 1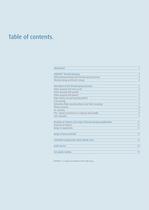
Introduction 3 LINSPRAY® Thermal Spraying 4 Differentiating between the thermal spray processes 4 Thermal energy and kinetic energy 4 Description of the thermal spray processes 5 Flame spraying with wire or rod 5 Flame spraying with powder 5 Flame spraying with plastics 6 High velocity oxy-fuel spraying (HVOF) 6 Cold spraying 7 Detonation flame spraying (shock-wave flame spraying) 7 Plasma spraying 8 Arc spraying 8 PTA – plasma transferred arc surfacing with powder 9 Laser spraying 9 Branches of industry and range of thermal spraying applications 11 Branches of industry 11 Range of...
Open the catalog to page 2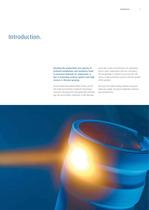
Introduction. Boosting the productivity and capacity of technical installations and machinery leads to increased demands on components. A key to protecting surfaces against such high stresses is thermal spraying. At the Linde International R&D Center, part of the Linde Gas Division in Munich (Germany), research, development and application technology are successfully combined. In the thermal spray lab, results and solutions are optimized, and in close cooperation with our customers, this knowledge is utilized to increase the efficiency of the production process and the quality of the...
Open the catalog to page 3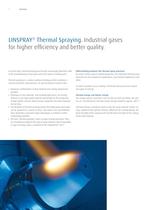
LINSPRAY® Thermal Spraying. Industrial gases for higher efficiency and better quality. Overview In recent years, thermal spraying has become increasingly important, both in the manufacturing of new parts and in the repair of existing parts. Thermal spraying is a surface coating technology which combines a variety of positive characteristics. Its special features testify to this: • Numerous combinations of base material and coating material are possible. • Shortages of raw materials, and resulting high prices, are forcing industry to use high-grade materials specifically for the production...
Open the catalog to page 4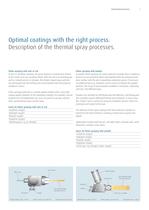
Thermal Spray Processes Optimal coatings with the right process. Description of the thermal spray processes. Flame spraying with wire or rod In wire or rod flame spraying, the spray material is continuously melted in the center of an oxy-acetylene flame. With the aid of an atomizing gas such as compressed air or nitrogen, the droplet-shaped spray particles are discharged from the melting zone and propelled onto the prepared workpiece surface. Flame spraying with wire is a widely applied method with a very high coating quality standard. In the automotive industry, for example, several...
Open the catalog to page 5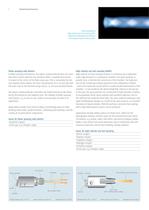
High velocity oxy-fuel spraying (HVOF) High velocity oxy-fuel spraying involves a continuous gas combustion under high pressure in a combustion chamber. The spray material, in powder form, is fed into the central axis of the chamber. The high pressure of the oxyfuel gas mixture produced in the combustion chamber – and in the expansion nozzle which is usually located downstream of the chamber – in turn produces the desired high flow velocity in the gas jet. In this way, the spray particles are accelerated to high velocities, leading to exceptionally dense spray coatings with excellent...
Open the catalog to page 6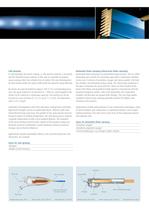
Cold spraying In cold spraying, the kinetic energy, i.e. the particle velocity, is increased and the thermal energy reduced. In this way it is possible to produce spray coatings which are virtually free of oxides. This new development became known under the name CGDM (Cold Gas Dynamic Spray Method). By means of a gas jet heated to approx. 600 °C at a corresponding pressure, the spray material is accelerated to > 1000 m/s and brought to the surface to be coated as a continuous spray jet. The particle jet can be focused on cross-sections of 1.5 x 2.5 up to 7 x 12 mm. The deposition rate is 3...
Open the catalog to page 7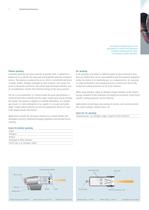
Thermal Spray Processes Plasma spraying In plasma spraying, the spray material, in powder form, is melted by a plasma jet in or outside the spray gun and propelled onto the workpiece surface. The plasma is produced by an arc which is constricted and burns in argon, helium, nitrogen, hydrogen or their mixtures. This causes the gases to dissociate and ionize; they attain high discharge velocities and, on recombination, transfer their thermal energy to the spray particles. The arc is not transferred, i.e. it burns inside the spray gun between a centered electrode (cathode) and the water-cooled...
Open the catalog to page 8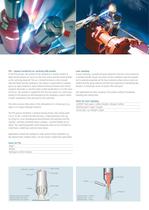
PTA – plasma transferred arc surfacing with powder In the PTA process, the surface of the workpiece is surface melted. A high-density plasma arc serves as the heat source and the metal powder as the surfacing material. The arc is formed between a non-consumable electrode and the workpiece. The plasma is generated in a plasma gas (e.g. argon, helium or argon-helium mixtures) between the central tungsten electrode (-) and the water-cooled anode block (+) in the transferred arc. The powder is supplied to the torch by means of a carrier gas, heated in the plasma jet and deposited on the...
Open the catalog to page 9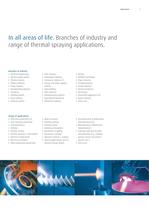
Applications 11 In all areas of life. Branches of industry and range of thermal spraying applications. Branches of industry • Medical engineering • Nuclear power plants • Chemical plants • Plastics industry • Pump industry • Metalworking industry • Foundries • Smelting plants • Steel industry • Extrusion plants • Wire industry • Automotive industry • Aerospace industry (1) • Energy and water supply / utilities • Ship building • Glass industry • Manufacturing industry • Agricultural machinery • Petroleum industry • Mining • Offshore technique • Paper industry • Printing industry • Textile...
Open the catalog to page 11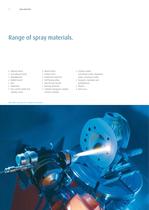
12 Spray Materials • Alloyed steels • Low-alloyed steels • Molybdenum • Babbitt metal • Zinc • Aluminum • Iron, nickel cobalt and stainless steel • Monel metal • Carbon steel • Exothermic material • Self-fluxing alloys • Non-ferrous metals • Brazing materials • Carbides (tungsten-carbide, chrome-carbide) • Ceramic oxides (chromium-oxide, aluminumoxide, zirconium-oxide) • Tungsten, tantalum and molybdenum • Plastics • And so on… Wire flame spraying of a cylinder head surface. Range of spray materials.
Open the catalog to page 12All Linde Gas catalogs and technical brochures
-
Overview of Shielding Gases
12 Pages
-
propane
1 Pages
-
lindoflamm_flame_solutions
2 Pages
-
hydrogen
2 Pages
-
acetylene
2 Pages
-
ETO
3 Pages
-
DA
2 Pages
-
Cl2
3 Pages
-
NH3
3 Pages
-
C2H6
3 Pages
-
CO
2 Pages
-
D2
2 Pages
-
Ar
2 Pages
-
Air
2 Pages
-
Liquid Helium - He
2 Pages
-
Carbon Dioxide -CO2
3 Pages
-
Liquid Argon - Ar
2 Pages
-
linde annual 2009
96 Pages
-
AXENIS Water Treatment
8 Pages
-
LINDOFLAMM Brochure
12 Pages
-
Acetylene Brochure
9 Pages
-
Bottom Injection systems
2 Pages