

Catalog excerpts
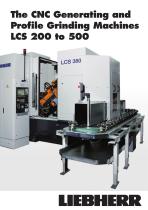
The CNC Generating and Profile Grinding Machines LCS 200 to 500
Open the catalog to page 1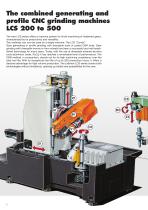
The combined generating and profile CNC grinding machines LCS 200 to 500 The new LCS series offers a machine system for finish machining of hardened gears, characterized by its productivity and versatility. Two methods can now be used on a single machine: The LCS “Combi” Gear generating or profile grinding with dressable tools or plated CBN tools. Gear grinding with dressable worms or form wheels has been a successful and well established technology for many years. Today, with the use of dressable sintered alumina tools (aluminum oxide, Al2O3) it has reached a remarkable level of...
Open the catalog to page 2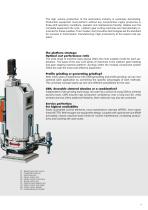
The high volume production of the automotive industry is extremely demanding. Production equipment must perform without any compromise: highly productive in three-shift operation conditions, operator and maintenance friendly, reliable over the complete equipment life cycle. Liebherr gear cutting machines are internationally renowned for these qualities. Their modern and innovative technologies set the standard for success in transmission manufacturing: High productivity at the lowest cost per piece. The platform strategy: Optimal cost performance ratio The wide range of machine sizes always...
Open the catalog to page 3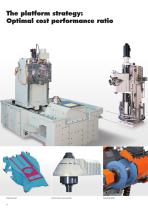
The platform strategy: Optimal cost performance ratio Direct drive work spindle Grinding head
Open the catalog to page 4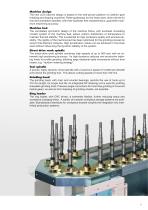
Machine design The new LCS machine design is based on the well-proven platform of Liebherr gear hobbing and shaping machines. Roller guideways for the linear axes, direct drives for tool and workpiece spindles, with their backlash free characteristics, guarantee maximum machining accuracy. Machine bed The completely symmetric design of the machine frame, with enclosed circulating coolant system of the machine bed, allows uniform distribution of temperature to maintain thermal stability. This is essential for high workpiece quality and process reliability. The rigidity of the machine bed has...
Open the catalog to page 5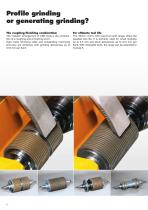
The roughing/finishing combination: The “classic” arrangement of CBN tools is the combination of a roughing and a finishing worm. High metal removing rates and outstanding machining accuracy are achieved, with grinding allowances up to 0.18 mm per flank For ultimate tool life The “Mono” worm, with maximum shift range, offers the greatest tool life. It is primarily used for small modules up to 2.5 mm and stock allowances up to 0.10 mm per flank. With dressable tools, the range can be extended to module 5.
Open the catalog to page 6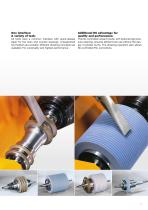
One interface: A variety of tools All tools have a common interface with quick-release taper for the main and counter bearings. Unsupported tool holders are avoided. Different dressing concepts are available: For universality and highest performance. Additional NC advantage for quality and performance: The NC controlled coolant nozzle, with optional high pressure cleaning, ensures efficient tool use without the danger of grinder burns. The dressing operation also allows NC controlled fHα corrections.
Open the catalog to page 7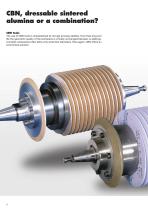
CBN, dressable sintered alumina or a combination? CBN tools The use of CBN tools is characterized by its high process stability. Over their long tool life the geometric quality of the workpiece is virtually unchanged between re-platings. Complex workpieces often allow only small tool diameters. Here again, CBN offers an economical solution.
Open the catalog to page 8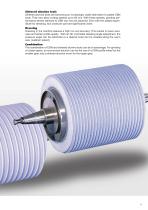
Sintered alumina tools Sintered alumina tools are becoming an increasingly viable alternative to plated CBN tools. They now allow cutting speeds up to 60 m/s. With these speeds, grinding performance almost identical to CBN can now be obtained. Even with the added expenditure for dressing, tool costs per part are significantly lower. Dressing Dressing in the machine assures a high run-out accuracy. This results in lower waviness and better profile quality. With an NC controlled dressing angle adjustment, the pressure angle can be optimized or a desired twist can be created along the worm...
Open the catalog to page 9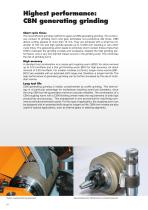
Highest performance: CBN generating grinding Short cycle times The most efficient grinding method for gears is CBN generating grinding. The continuous contact of grinding worm and gear eliminates non-productive idle times. CBN allows cutting speeds of more than 70 m/s. They are achieved with a small tool diameter of 140 mm and high spindle speeds up to 12,000 rpm resulting in very short cycle times. The generating action leads to extremely short contact times of less than 0.003 s between the grinding crystals and workpiece. Despite the high grinding performance, only a very low thermal...
Open the catalog to page 10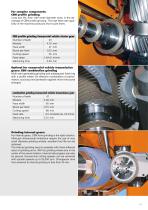
For complex components: CBN profile grinding Long tool life, even with small diameter tools, is the advantage of CBN profile grinding. The high feed rate capability of the machine produces short cycle times. Grinding internal gears: For internal gears, CBN form grinding is the right solution. Although dimensional limitations require the use of very small diameter grinding wheels, excellent tool life can be obtained. The internal grinding head is available with three different sizes of grinding arms. With its grinding wheel axis in the center of the swivel rotation, internal helical gears...
Open the catalog to page 11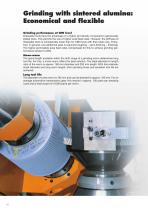
Grinding with sintered alumina: Economical and flexible Grinding performance at CBN level Dressable tools have the advantage of a higher grit density compared to galvanically plated tools. This permits the use of higher axial feed rates. However, the stiffness of dressable tools is considerably lower than for CBN tools with their steel core. Therefore, in general, one additional pass is required (roughing – semi-finishing – finishing). The higher permissible axial feed rates compensate for this to achieve grinding performance similar to CBN. Mono-worm The spiral length available within the...
Open the catalog to page 12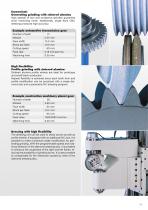
Economical: Generating grinding with sintered alumina High speeds of tool and workpiece spindles guarantee short machining times. Additionally, single flank CNC dressing produces high accuracy. Dressing with high flexibility The dressing unit can be used to dress worms as well as profile wheels. If equipped with an additional NC axis, it is possible to make a pressure angle modification for generating grinding. With the programmable speed and rotational direction of the diamond dressing disc, it is possible to influence the roughness of the right and left flanks, reducing the possibility of...
Open the catalog to page 13All Liebherr Mischtechnik catalogs and technical brochures
-
Timber handling
36 Pages
-
Opening up New Horizons
32 Pages
-
The Compactmix 1.0
12 Pages
-
HTM 1205 T / LTB 12+4
2 Pages
-
LTB
12 Pages
-
Ring-pan mixer
8 Pages
-
50 M5 XXT
4 Pages
-
47 M5 XXT
4 Pages
-
42 M5 XXT
4 Pages
-
37 Z4 XXT
4 Pages
-
32 Z5 XXT
4 Pages
-
Control Systems from Liebherr
12 Pages
-
Mobile twin shaft Mixer
2 Pages
-
Optimum Conveyance of Concrete
16 Pages
-
LTM 1090-4.2
30 Pages
-
LTM 1230-5.1
24 Pages
-
Process monitoring ARTIS
4 Pages
-
Gear shaping machine LS 180
4 Pages
-
The ChamferCut process
4 Pages
-
Flyer Betomat sectional view
1 Pages
-
Jobreport Betomat
2 Pages
-
Brochure mixersystems
12 Pages
-
Brochure truckmixer HTM 905
8 Pages
-
DW 1.25 - 6.0
4 Pages
-
Mobilmix 2.5
2 Pages
-
Stationary Concrete Pumps
20 Pages
-
Raupen- betonpumpe
4 Pages
-
37 R4 ST
4 Pages