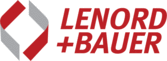

Catalog excerpts

f\ LENORD / +BAUER ... automates motion. SENSORS AND CONTROL SYSTEMS iN WiND TURBiNES
Open the catalog to page 1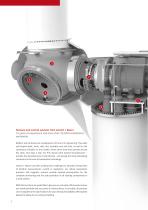
Sensors and control systems from Lenord + Bauer 15 years of experience and more than 30,000 installations worldwide Modern wind turbines are masterpieces of the art of engineering. They defy sub-tropical heat, arctic cold, dirt, humidity and salt mist, as well as the continuous vibration in the nacelle. At the same time they operate around the clock, 365 days a year. For this reason wind turbine manufacturers – just like the manufacturers of rail vehicles – are among the most demanding customers in the area of automation technology. Lenord + Bauer has been tackling this challenge for...
Open the catalog to page 2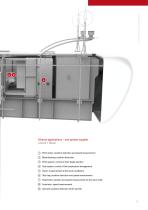
Source: Wind-to-Energy GmbH, Rostock Diverse applications – one system supplier Lenord + Bauer 1 Pitch motor: position detection and speed measurement 2 Blade bearing: position detection 3 Pitch system: control of rotor blade position 4 Sub-system: control of the temperature management 5 Tower: measurement of the tower oscillation 6 Slip ring: position detection and speed measurement 7 Powertrain: position and speed measurement on the main shaft 8 Generator: speed measurement 9 Azimuth: position detection of the nacelle
Open the catalog to page 3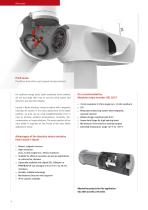
Source: Wind-to-Energy GmbH, Rostock Pitch motor Pitch motor Position detection and speed measurement For optimal energy yield, pitch-controlled wind turbines do not just align their hub to suit the wind speed and direction, but also their blades. Lenord + Bauer absolute rotary encoders with integrated bearings are proven in the exact adjustment of the blade position, as they can be used straightforwardly even in case of extreme ambient temperatures, humidity, dirt, condensation or heavy vibration. The exact position of the rotor blade is acquired on the B-side of the rotor blade adjustment...
Open the catalog to page 4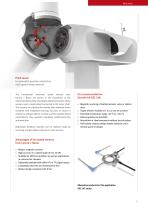
Source: Wind-to-Energy GmbH, Rostock Pitch motor Pitch motor Incremental position detection and speed measurement The incremental rotational speed sensors from Lenord + Bauer are proven in the acquisition of the rotational speed of the rotor blade adjustment motor; these sensors scan a target wheel connected to the motor shaft. The sensors are significantly smaller than absolute rotary encoders with integrated bearings, but just as robust in relation to ambient effects. As they scan the toothed wheel contactlessly, they operate completely maintenance-free and wear-free. Redundant feedback...
Open the catalog to page 5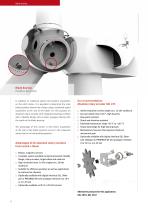
Blade bearing Source: Wind-to-Energy GmbH, Rostock Blade bearing Position detection In addition to rotational speed and position acquisition on the pitch motor, it is possible to determine the rotor blade position almost free of play using a rotational speed acquisition at the root of the blade. For this purpose an absolute rotary encoder with integrated bearings is fitted with a flexible flange; this encoder engages directly with the teeth on the blade bearing. The advantage of this variant is that direct acquisition at the root of the blade prevents errors in the measured values due to an...
Open the catalog to page 6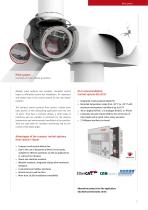
Pitch system Source: Wind-to-Energy GmbH, Rostock Pitch system Control of rotor blade position Modern wind turbines use complex, cascaded control loops to efficiently control the installation. An important sub-system here is the control system for the rotor blade position. The compact control systems from Lenord + Bauer have been proven in this demanding application over the last 15 years. They have a compact design, a wide range of interfaces and are suitable in particular for the adverse temperature and environmental conditions in the nacelles. They are used both for condition monitoring...
Open the catalog to page 7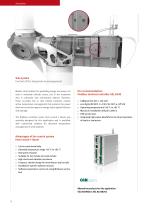
Source: Wind-to-Energy GmbH, Rostock Sub-system Control of the temperature management Modern wind turbines for generating energy are proven not only in moderate climatic zones, but in the meantime also in sub-polar and sub-tropical regions. However, these so-called hot or cold climate locations require active temperature management that protects the power electronics and also gears or energy stores against failures and damage. The fieldbus controller series from Lenord + Bauer was specially designed for this application and is available with customised software for decentral temperature...
Open the catalog to page 8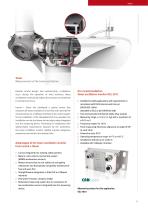
Source: Wind-to-Energy GmbH, Rostock Tower Measurement of the tower oscillation Despite careful design and workmanship, oscillations occur during the operation of wind turbines; these oscillations continuously subject the structure and materials to mechanical stress. Lenord + Bauer has developed a special sensor that measures the tower oscillations in real time and transmits the measurements via a CANopen interface to the control system for the installation. If the stipulated limits are exceeded, the installation can be shut down via two safety relays integrated into the measuring device....
Open the catalog to page 9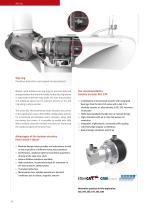
Source: Wind-to-Energy GmbH, Rostock Slip ring Slip ring Position detection and speed measurement Modern wind turbines use slip rings to transmit data and energy between the hub and nacelle. As the slip ring rotates in synchronism with the rotor shaft, the rotor hub position and rotational speed can be acquired directly on the slip ring using a rotary encoder. The series GEL 290 incremental rotary encoders are proven in this application. Due to the flexible configuration options for incremental and absolute rotary encoders, along with the various bus covers, it is possible to realise with...
Open the catalog to page 10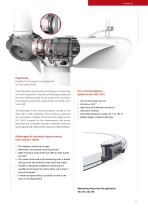
Source: Wind-to-Energy GmbH, Rostock Powertrain Position and speed measurement on the main shaft As an alternative to drive train monitoring on the slip ring, the rotor hub position, the rotor pin locking position and the rotor rotational speed can be acquired by scanning a ferro-magnetic slotted disc permanently connected to the rotor shaft. The advantage of this mounting position directly on the drive train is that acquisition errors cannot be caused by an intermediate coupling. The incremental speed sensor GEL 2495 is proven for the measurement; this sensor generates two completely...
Open the catalog to page 11All LENORD + BAUER catalogs and technical brochures
-
SeGMo-Positioning GEL 6109
16 Pages
-
SeGMo-Motion GEL 6108
8 Pages
-
SeGMo-Box GEL 6505 A/B
20 Pages
-
Service
12 Pages
-
PowerDRIVE-System
20 Pages
-
Sensors for rail vehicles
20 Pages
-
MiniCODER
20 Pages
-
Product overview
44 Pages
-
Wind Power
2 Pages
-
Flyer Odometer
2 Pages
-
Railway brochure
2 Pages