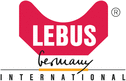

Catalog excerpts
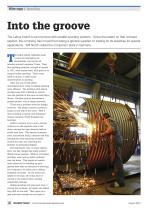
Wire rope | Spooling Into the groove The Lebus brand is synonymous with parallel spooling systems. Since the patent on that concept expired, the company has moved from being a general supplier, to trading on its expertise for special applications. Will North visited the company’s plant in Germany he LeBus family originally made a name for themselves as blacksmiths, serving the oil industry around Longview, Texas. Their first spooling products, brought to market in 1937, were square bars, with grooves to support helical spooling. These were fixed to drums, to make some improvements to spooling. After the war, Frank LeBus investigated new ways of making spooling more efficient. The problem with helical spooling was that it offered no control over the position of the rope on multi-layer drums. His first product introduced a parallel groove, with a single crossover. There was a problem with this design, however. The single crossover created a bump on one side of the drum. With a drum working at speed, that imbalance creates vibration which damages the bearings. LeBus’s solution was to add a second crossover on the opposite side of the drum, moving the rope along by half its width each time. This second crossover zone, and second bump, balanced the first, keeping the drum spinning smoothly around the axis, and removing the problem of mechanical fatigue. This innovation was, in many experts’ eyes, the key change that made modern lifting cranes possible. Without controlled spooling, rope ends up piled randomly over the drum. That might not matter much when you’re winding up your garden hose after an afternoon’s watering, but it matters a lot when you’re lifting hundreds of tonnes. As the layers are added to the rope, all of that force is carried to the layers below, causing irepparable damage. Helical spooling only goes part way to solving this problem. As layers are added, they drift to one side. That opens up a gap, and soon enough the top layer of CRANES TODAY | www.cranestodaymagazine.com
Open the catalog to page 1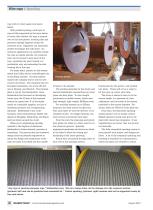
Wire rope | Spooling rope will cut down again into layers below. With parallel spooling, each layer of rope is fully supported by the layer below. At every half rotation, the rope is pushed over to the next groove, ensuring that any potential damage happens within the crossover zone. Engineers can accurately predict the fatigue this will cause. On intensive applications, by carefully cutting the rope at regular periods, the crossover zone can be moved to new parts of the rope, spreading the wear caused in a predictable way, and extending the safe working life of the rope. For many years,...
Open the catalog to page 2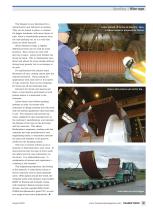
Spooling | Wire rope The flanges too are fabricated by a subcontractor and delivered as needed. They can be bolted in place, or welded. On bigger machines, with many layers of rope, there is considerable pressure from the rope pushing out, so it is vital that these are fitted securely. When demand is high, a slightly different process can be used for some products. Here, drums are cast with grooves in place. Lebus then finishes the drums by hand. This is, Seidenather says, faster and allows for more reliable delivery during busy periods, but is no cheaper to do well. For applications that...
Open the catalog to page 3