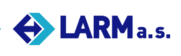
Catalog excerpts
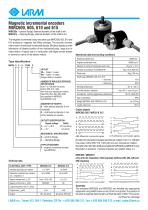
Magnetic incremental encoders MIRC600, 605, 610 and 615 MIRC60x – synchro flange, external diameter of the shaft 6 mm MIRC61x – clamping flange, external diameter of the shaft 6 mm The magnetic incremental rotary encoders type MIRC600, 605, 610 and 615 working on magnetic Hall Effect principle. The encoder converts rotary motion to electrical incremental signals. Electrical signals provide information of bilateral position of two mechanical parts, angle turn or rotary motion. A typical use is in conjunction with digital control system or drivers for control of the electric motors. Mechanical data and working conditions Rotational speed max. Angular acceleration max. Type identification MIRC6 X X – X / XXXX X Moment of inertia of mechanical parts max. OUTLET PA – Cable 1 m axial PB – Cable 1 m radial (longer cable on request) Number of impulses (periods) per rotation from 1 to 128 after one pulse, further 256, 512, 1024 with one zero impulse per rotation. Next 200, 250, 400, 500, 2048 are possible for MIRC605 and MIRC615 only DIAMETER OF SHAFTS 6 – shaft external diameter 6 mm (standard) 4 – shaft external diameter 4 mm (other diameter on request) OUTLETS IDENTIFICATION Supply voltage Outlet 0 – +10 ÷ +30 V HTL line driver 5 – + 5 V line driver Shaft loads MIRC600, 605, 610, 615 – axial max. Working temperature Humidity relative / absolute Atmosphere (without aggressive substances) Type of protection Weight MIRC600, 605 / MIRC610, 615 Length cable max. MECHANICAL SPECIFICATION 0 – synchro flange 1 – clamping flange TYPE OF ENCODER 6 – magnetic incremental encoder type MIRC6xx Next 200, 250, 400, 500, 2048 are possible for MIRC605 and MIRC615 only. MIRC305 MIRC315 MIRC325 only and into resolution (lines) x 4. Resolution in/ positions/ = Number impulses per rotation 1024 impulses Number of incremental impulses (periods) per rotation: from 1 to 128 after one pulse, further 200, 250, 256, 400, 500, 512, 1024, 2048 with one zero impulse per rotation. MIRC605 / MIRC615 Resolution in positions = Number impulses per rotation (lines) x 4. only and into resolution 1024 impulses (without 200, 250, 400 and MIRC305 / MIRC315 / MIRC325 only and into resolution 1024 impulses 500 impulses) Technical data ELECTRICAL DATE / TYPE Number of incremental impulses (periods) per rotation: 1 to 128 after one Number of incremental impulses (periods) per rotation: fromfrom 1 to 128 after pulse, further 200, 250, 256, 400, 500,512, 1024, 2048 with one zero impulse per rotation. one pulse, further 256, 512, 1024 with one zero impulse per rotation. Resolution in positions = Number impulses per rotation (lines) x 4. Impulses (periods) per rotation Resolution (positions per revolution) = impulses x 4 Output frequency max. FO (kHz) Output max. IO (mA) Output ASSEMBLY The MIRC30x encoder is installed into appropriate equipment using 3xM4 screws or a groove. The position of the shaft is explicitly determined by a fitted diameter of 50h7 mm. The MIRC31x encoders are installed using 3xM3 screws and the position of the shaft is explicitly determined by a diameter of 36f8. It is recommended to use appropriate Assembly homokinetic connections (see the catalogue sheet „Accessories“). The MIRC32x encoders ASSEMBLY are mounted on the shaft of the respective device and 2 imbus M4 screws. After the encoder The The encoders MIRC600 and MIRC605 are installed into appropriate a MIRC30x encoder is installed into appropriate equipment using 3xM4 screws or groove. The position required position and determined of the fixed plate connection are is to be turned to the of the shaft is explicitly4xM3 screwsby a fitted diameter of 50h7 mm. to The equipment using 4xM3 screws on 3xM3 mmas to groove. The of the shaft MIRC31x encoders are installed be designed so or a avoid exceeding the maximum be tightened. The connection has to usingdia. 26screws and the position position of is explicitly shaft is or axial load applied to by a fitted diameter of 33h7.use appropriate the determined by a diameter of 36f8. It is it is necessary The encodadmissible radial explicitly determinedthe shaft and recommended to keep the connection homokinetic cable of the MIRC3xx encoder must be fastened so as MIRC32x encoders aligned. Theconnections (see the catalogue sheet „Accessories“). The to avoid stress on the continued on next water are mounted is own weight. respective device and with running or splashing page it encoder by on the shaft of theIn wet environments 2 imbus M4 screws. After the encoder is is to be turned not to position the MIRC3xx encoders with the fixed pointing upwards. recommended to the required position and 4xM3 screws of the shaft plate connection are to be tightened. the electrostatic sensitive components used it is recommended Considering The connection has to be designed so as to avoid exceeding the maximum to admissible radial or axial without power supply and to follow the work rules connect the encoder load applied to the shaft and it is necessary to keep the connection for aligned. The sensitive MIRC3xx electrostaticcable of thedevices. encoder must be fastened so as to avoid stress on the encoder by is own weight. In wet environments with running or splashing water it is
Open the catalog to page 1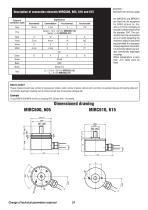
Assembly -continued from previous page Colors of connection cable ers MIRC610 and MIRC615 are fixed into the equipment by 2xM3 screws on dia. 22,0 ± 0,15 mm. Centering of encoder is determined by mat fits diameter 15h7. The connection has to be constructed so as to avoid exceeding the maximum radial or axial shaft load permitted. It is necessary to keep alignment connection. It is recommended to use suitable homokinetic diaphragm couplings. When temperature is less then -5°C cable must be fixed. How to order? Please indicate encoder type, number of impulses per rotation, outlet, number of...
Open the catalog to page 2All LARM a.s. catalogs and technical brochures
-
DRAW-WIRE ENCODER LS501
2 Pages
-
Encoders
7 Pages
-
JIGS & FIXTURES
3 Pages
-
Company presentation
14 Pages