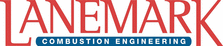
Catalog excerpts
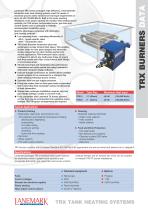
Lanemark TRX series packaged, high efficiency, small diameter immersion tube tank heating systems meet the needs of industrial process tanks which have heat input requirements of up to 45 kW (150,000 Btu/h). Built to the same exacting standards as the larger capacity TX modular tank heating burner systems, the TRX burner incorporates burner, gas train and control system and is packaged to simplify/ minimise plant installation work. Specific advantages compared with alternative tank heating methods – l ow operating costs – operating efficiencies of L ≥80% gross calorific value ≥90% net calorific value l RX small diameter immersion tube heat T exchangers occupy minimal tank space. This enables smaller tanks for new plant designs and allows the simple replacement of other heating systems for retrofit applications.TRX immersion tubes can be configured in almost any multi-pass shape to ensure that they remain well clear of any internal tank fittings or processing areas. l ll tank heat input and immersion tube performance A calculations are easily carried out using Lanemark’s dedicated computer design software. l nduced draught combustion air system allows multiple I burner systems to be connected to a common flue while retaining individual burner control. l perates with low gas supply pressures. O l iring into rubber lined or fibre glass tanks is permitted F due to low initial heat exchanger surface temperatures at tank connection. l imple heat exchanger installation requires only two S Model pipe flange drillings, usually in one tank wall. TRX15 l ully compatible with Lanemark TX burner systems F so that they may be incorporated into schemes where TRX20 multiple TRX/TX burner arrangements are required. Tube Size Maximum Heat Input l Product finishing (metal parts, steel strip, wire products, etc.) – re-treatment and treatment processes including: P alkali/caustic degreasing phosphating hot water rinsing aluminium etching anodising borax and lime coatings – ip tanks D – pray systems S – ot water supply systems H l Cleaning (industrial washing machines) – lastic crate washers P arts washers –P – ottle washers B l Food and Drink Production – ot water tanks H – ini brewery wort coppers M – leaning in place (CIP) tanks C – nimal scalders A – lanchers B TRX burners conform with European Standard EN 746 Part 2 as appropriate and are pre-wired and tested prior to despatch. Specifications Lanemark packaged TRX immersion tube burner systems are assembled within a splash-proof enclosure and incorporate the burner, gas valve train and burner controls, exhaust damper and an exhaust fan which can be coupled to multiple TRX/TX burner installations. Fuels Control voltages Exhaust fan electrical supplies Flame sensing Heat output control options 4 atural gas N 4 30V 2 4 00V/3ph/50Hz 4 4 lame electrode F 4 n/off or High/low O TRX TANK HEATING SYSTEMS Typical Applications
Open the catalog to page 1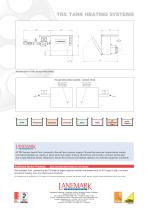
TRX TANK HEATING SYSTEMS 385 Alkali Cleaners All dimensions in mm, except where stated. Two gas inlet positions available - customer choice Right Hand Burner With Right Hand Heat Exchanger Left Hand Burner With Left Hand Heat Exchanger Demineralised Water Alkali Cleaners All TRX burners benefit from Lanemark’s BurnerCare customer support. BurnerCare services include burner system commissioning/start-up, supply of spare parts and system training. BurnerCare will provide a contract service plan and a rapid response facility, designed to ensure the continued and reliable operation of Lanemark...
Open the catalog to page 2All LANEMARK COMBUSTION ENGINEERING LTD catalogs and technical brochures
-
TRX Series Burners
2 Pages
-
Duct Burners (DB Series)
2 Pages
-
TX Series Burners
2 Pages
-
KS Burners
6 Pages
-
FORCED DRAUGHT HC BURNERS
4 Pages
-
Lanemark DB Duct Burners
2 Pages
-
Lanemark Midco Burners
2 Pages
-
TX Tank Heating System
2 Pages
-
FD-E Burners
2 Pages
-
FD-C Burners
2 Pages
-
MTX Series Burners
2 Pages
-
KS SERIES Product Range
1 Pages
-
HC burner series
4 Pages
-
FD-C (GA) Burners
2 Pages
-
FD-E (GA) Burners
2 Pages