

Catalog excerpts
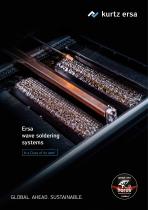
Ersa wave soldering systems In a Class of its own! GLOBAL. AHEAD. SUSTAINABLE.
Open the catalog to page 1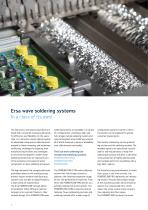
Ersa wave soldering systems In a class of its own! The electronics manufacturing industry is faced with constantly increasing demands for efficiency and flexibility. At the same time, its customers require highest quality at unbeatable cheap prices. Manufacturers respond to these increasing, and sometimes conflicting, challenges by adapting their manufacturing facilities and strategies. In this tense atmosphere, modern wave soldering systems are an important part of the economic processing of wired components in mass soldering processes. soldering systems are available in a variety of...
Open the catalog to page 2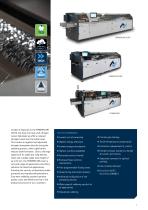
POWERFLOW ULTRA number of features as the POWERFLOW ULTRA, but does not have a full nitrogen tunnel. Optionally we offer a compact nitrogen tunnel over the solder wave. This creates a targeted and adjustable nitrogen atmosphere directly during the soldering process, which significantly reduces oxide formation. Due to the large capacity of its solder pot, long wetting times and a stable solder wave height of up to 16 mm, the POWERFLOW covers a very wide range of applications and offers solutions for almost all applications. Providing the security of absolutely stable processes and...
Open the catalog to page 3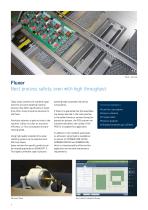
Fluxer Best process safety, even with high throughput Today, spray systems are standard equipment for any wave soldering machine, however they differ significantly in detail. Ersa offers many innovative solutions for the fluxer. Particular attention is paid not only to the systems’ safety, but also on economic efficiency, i.e. flux consumption and processing speed. Using high quality materials Ersa wave soldering sytems can be operated with VOC-free fluxes. Spray sections for specific products can be entered graphically on ERSASOFT 5. This highly convenient type of process Ultrasonic fluxer...
Open the catalog to page 4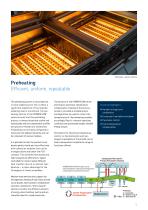
Preheating – dynamic emitters Preheating Efficient, uniform, repeatable The preheating process is very important in wave soldering since this is where a significant proportion of the required soldering heat is transferred. The preheating section of the POWERFLOW series ensures that the preheating process is always absolutely stable and reproducible and that temperature profiles and process windows are maintained. Preheating can be freely configured to meet even the highest demands and can be composed of various modules: It is possible to heat the printed circuit boards gently, evenly and...
Open the catalog to page 5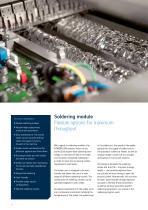
Technical highlights: Double soldering module Nozzle height adjustment (manual and automatic) Easy maintenance: The nozzle shaft can be removed without tools; the support stand is housed in the machine Solder nozzle combinations for different applications/Vario Wave E xchange solder pot with trolley and heat-up station Solder bar feeder with monitoring for all commercially available bar formats Sequential soldering User-friendly Flexible solder nozzle configuration Optimal soldering results Soldering module Flexible options for maximum throughput With regard to soldering modules, the...
Open the catalog to page 6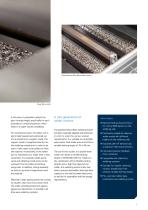
Combination of Vario Wave solder nozzles Power Wave nozzle In this way it is possible to adjust the pass-through height specifically for each assembly in a mixed production, which leads to a higher system availability. For maintenance work, the solder unit is electrically lowered and positioned out of the machine on a support stand. The support stand is integrated directly into the soldering module and, in order to be used, it only needs to be pulled out from the machine. Accessibility of the solder pot for maintenance or repair work is very convenient. For example, solder pump, canal and...
Open the catalog to page 7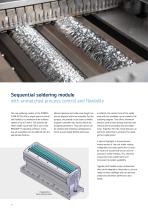
Sequential soldering module with unmatched process control and flexibility The new soldering module of the POWERFLOW ULTRA offers unique process control and flexibility. Its innovative drive achieves speeds of up to 5 mm/s. The distance between solder nozzle and PCB is set via the ERSASOFT 5 operating software. In this way, all assemblies can be soldered with the appropriate distance. Nozzle clearance and solder wave height can also be adjusted within an assembly. For this purpose, the printed circuit board is divided program-controlled into sectors which are assigned parameters. Thus each...
Open the catalog to page 8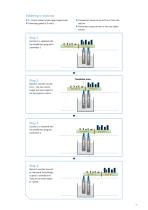
Soldering in sections 5 - 18 mm solder nozzle height adjustment POWERFLOW ULTRA FACELIFT Traversing speed of 5 mm/s Component clearance up to 18 mm from the bottom Permanent measurement of the real solder Sequential soldering Step 1: Section 1 is soldered with the predefined programm parameter 1 POWERFLOW ULTRA FACELIFT Sequential soldering Transition area Section1 is soldered with the program parameters Step 2: Nozzle 1 reaches section limit – the new nozzle height and wave speed is set by program control POWERFLOW ULTRA FACELIFT Sequential soldering Parameters for solder nozzle 1 are...
Open the catalog to page 9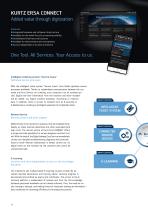
KURTZ ERSA CONNECT Added value through digitization Features Integrated hardware and software infrastructure Available for the whole Kurtz Ersa machine portfolio Standardized interfaces and systems Available for web browsers and smartphones Access independent of location and device One Tool. All Services. Your Access to us. Intelligent ticketing system "Service Cases" Optimized service processes With the intelligent ticket system "Service Cases", Ersa GmbH optimizes service processes worldwide. Thanks to standardized communication between the customer and Ersa Service via...
Open the catalog to page 10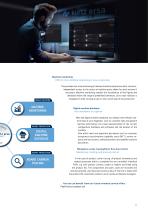
Machine monitoring KPIs for the condition monitoring of your production SMART MACHINE MACHINE MONITORING SMART PRODUCTION DIGITAL MACHINE DATABASE PP SMART PRODUCTION BOARD CARRIER TRACING This provides real-time monitoring of relevant machine and process data. Locationindependent access to the status of machine parts allows for quick actions if necessary. Machine monitoring enables the visualization of key figures and deviations within the range of predefined tolerances. Limit value violation is displayed in order to keep an eye on the control loop of the production. Digital machine...
Open the catalog to page 11All Kurtz GmbH & Co. KG catalogs and technical brochures
-
Ersa Selective Soldering Systems
28 Pages
-
KURTZ ERSA ALPHA 140
2 Pages
-
KUTZ PROTECTIVE SOLUTIONS
16 Pages
-
KURTZ CASTING SOLUTIONS
16 Pages
-
VERSAPRINT 2
12 Pages
-
Kurtz POWerBoard
6 Pages
-
Circular Foam
16 Pages
-
Revolutionary RF Technology
4 Pages
-
Kurtz Safety Audits
4 Pages
-
Kurtz Filling Systems
4 Pages
-
Catalogue Kurtz Foundry Machines
40 Pages
-
Kurtz FOAMER
12 Pages