

Catalog excerpts
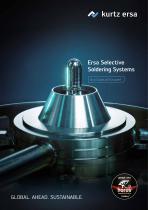
Ersa Selective Soldering Systems In a Class of its own! GLOBAL. AHEAD. SUSTAINABLE.
Open the catalog to page 1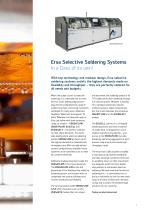
Ersa Selective Soldering Systems In a Class of its own! With top technology and modular design, Ersa selective soldering systems satisfy the highest demands made on flexibility and throughput – they are perfectly tailored for all needs and budgets. When the subject turns to selective soldering, it is impossible not to think of Ersa. Ersa’s leading edge technology and the comprehensive range of models have been convincing customers worldwide for many years. Maximum flexibility? Maximum throughput? Or both? Whatever the demands may be, Ersa can deliver with their extensive range of models –...
Open the catalog to page 3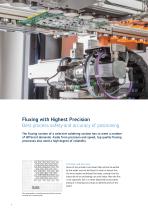
Fluxing with Highest Precision Best process safety and accuracy of positioning The fluxing system of a selective soldering system has to meet a number of different demands. Aside from precision and speed, top quality fluxing processes also need a high degree of reliability. Precision and Accuracy Areas of the printed circuit board that will not be wetted by the solder may not be fluxed. In order to ensure this, the most modern multidrop flux heads, coming from the industrial ink-jet technology, are used today. Here the flux is not vaporized, but it is rather deposited by accurately jetting...
Open the catalog to page 4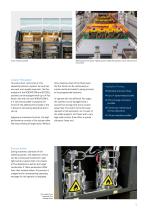
Multidrop precision fluxer: Highest process safety through flux volume measurement and control 2 flux modules possible Largest Throughput To ensure short cycle times in this sequential process, dynamic servo drives are used, and, equally important, the flux modules of the VERSAFLOW and ECOCELL systems can be equipped with up to 4 flux heads. And with the new VERSAFLOW 4, it is now also possible to program the moves of the additional flux heads in the Y-distance, eliminating downtime due to set-up. Applying an innovative function, the high performance controls of the system allow the exact...
Open the catalog to page 5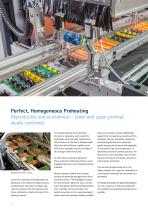
Perfect, Homogeneous Preheating Reproducible and economical – lower and upper preheat ideally combined For optimal wetting of the pad and the pins to take place, particularly for assemblies with high heat requirement, full activation of the flux is indispensable. Only then will sufficient capillarity and with that a complete rise of the solder in the through-hole be ensured. To meet these numerous demands, Ersa’s selective soldering systems can be equipped with up to five individual preheat modules. Segmented IR heater cassette Lead-free, multilayer and high power applications in the...
Open the catalog to page 6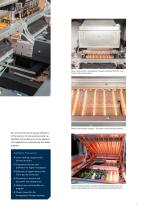
Power convection for a homogeneous through warming of the PCB – even for the most complex boards Bottom-side preheater cassette – IR emitters can be switched in groups Yet, and to improve the energy efficiency of the system, for processing smaller assemblies the heated area can be adapted. This adaptation is controlled by the solder program. Highlights Preheating: Lower heating cassette with infrared emitters Segmented bottom-side preheater for higher throughput Selection of upper heaters with full or partial convection P yrometer to monitor and document the temperature Heated area...
Open the catalog to page 7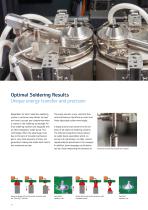
Optimal Soldering Results Unique energy transfer and precision Regardless for which selective soldering system a customer may decide, he does not have to accept any compromise when it comes to the soldering technology. All Ersa soldering systems are equipped with an electromagnetic solder pump. This technology offers the advantage, that, due to the lack of movable mechanical parts, very small amounts of dross are generated, making the solder bath itself a low-maintenance item. Improved break-off during nozzle retraction with the “Peel-Off” function The pump ensures a very constant flow rate...
Open the catalog to page 8
Visual process control – camera system shows real-time soldering process and assists in detecting defects the board, so that the correct positioning of the solder nozzle in relation to the underside of the board is ensured. So as to offer the largest possible flexibility together with the shortest cycle times, Ersa offers its customers the choice between a variety of solder bathand nozzle concepts, which are combinable in numerous ways. The innovative “Peel-Off” function enables to optimally form solder joints when soldering on a horizontal level, and the formation of solder shorts...
Open the catalog to page 9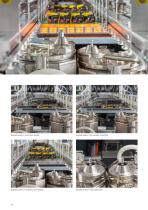
Dual pot system, Y- and Z axes variable Dual pot system, Y axis variable, Z axis fixed Dual pot system, Y axis fixed, Z axis variable Dual pot system, Y- and Z axes fixed
Open the catalog to page 10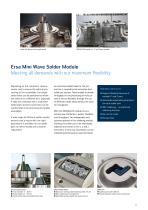
Single Pot System with single nozzle VERSAFLEX module, X-, Y- and Z axis variable Ersa Mini Wave Solder Module Meeting all demands with our maximum flexibility Depending on the customers’ requirements, and to ensure the optimal processing of the assemblies, the single solder baths can be positioned on either the same or on a different axis. Especially if they are combined with a multiwave solder bath, shortest cycle times can be reached also in the processing of complex assemblies. A wide range of different solder nozzles ensures that a nozzle with the right parameters is available for the...
Open the catalog to page 11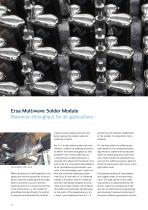
Ersa Multiwave Solder Module Maximum throughput for all applications Electromagnetic solder pump When the process is well-adapted to the application and the quantities to be produced, selective soldering will invariably lead to economic success. One very important factor in connection with this is the productivity, i.e. the number of assemblies moving through the system. In more and more production facilities classical wave soldering systems are being replaced by modern selective soldering systems. seconds can be realized, independent of the number of components to be soldered. But if, in a...
Open the catalog to page 12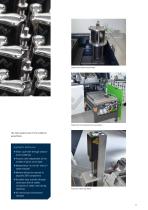
Solder wave height measurement Solder bath in maintenance/set-up position the high quality level of the soldered assemblies. Highlights Multiwave: Short cycle time through simultaneous soldering Process time independent of the number of joints to be made Maintenance “on the fly” (with 2nd solder module) M inimal distances required to adjacent SMT components E xcellent heat transfer through continuous flow of solder/ circulation of solder, even during soldering Automatic solder bar feeder
Open the catalog to page 13All Kurtz GmbH & Co. KG catalogs and technical brochures
-
Ersa wave soldering systems
16 Pages
-
KURTZ ERSA ALPHA 140
2 Pages
-
KUTZ PROTECTIVE SOLUTIONS
16 Pages
-
KURTZ CASTING SOLUTIONS
16 Pages
-
VERSAPRINT 2
12 Pages
-
Kurtz POWerBoard
6 Pages
-
Circular Foam
16 Pages
-
Revolutionary RF Technology
4 Pages
-
Kurtz Safety Audits
4 Pages
-
Kurtz Filling Systems
4 Pages
-
Catalogue Kurtz Foundry Machines
40 Pages
-
Kurtz FOAMER
12 Pages