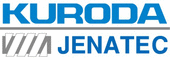
Catalog excerpts
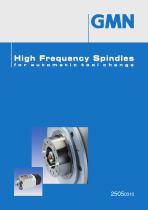
Machining Spindles Grinding Milling Drilling Threading Mill-Turning Measuring Optical Scanning Churning Mixing Driving Pumping High Frequency Spindles f o r GMN Paul Müller Industrie GmbH & Co. KG Äußere Bayreuther Straße 230 D - 90411 Nürnberg Telefon: +49 (0) 9 11 - 56 91 - 2 40 Telefax: +49 (0) 9 11 - 56 91 - 6 99 E-Mail: vertrieb.spi@gmn.de Internet: www.gmn.de
Open the catalog to page 1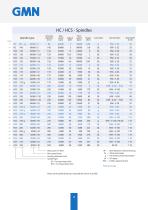
HC / HCS - Spindles Spindle type Page Tool interface Max. power S1 [kW] Max. speed [rpm] Housing diameter [mm] Spindle type HC = for open-loop drive HCS = for closed-loop drive Please ask if spindle drawing is required. We send it as dxf file. Bore diameter of front bearings Oil/air lubrication Permanent grease lubricatiion ISO taper Hollow tapered shank Preference type
Open the catalog to page 3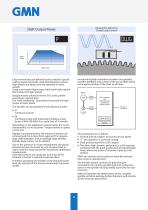
Integral Encoders For Closed Loop Control Shaft Output Power Incorporating high resolution encoders into spindles, provides feedback and control of the actual shaft speed, and angular position of the shaft, at all times. Chip removal rates are defined by the material's specific cutting speeds. Generally small tool diameters require high speeds and larger tools are operated at lower speeds. Large tools require high torque while small tools require less torque, but higer speeds. Integral motors utilized in the HC/HCS style spindle meet these requirements. The "field weakening" characteristics...
Open the catalog to page 4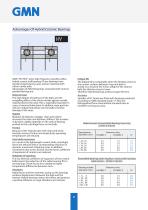
Advantages Of Hybrid Ceramic Bearings GMN "HC/HCS" series high frequency spindles utilize hybrid ceramic ball bearings. These bearings have standard steel bearing races and are matched with silicon nitride balls. Advantages of Hybrid bearings compared with normal spindle bearings are: Reduced wear The high degree of hardness of the balls, and the nongalling effect of the silicon nitride against metallic material lessens the wear. This is especially important in cases of minimal lubrication. In addition, wear particles will not embed themselves into the balls to further damage of the races....
Open the catalog to page 5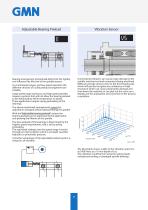
Adjustable Bearing Preload Vibration Sensor Bearing arrangement and preload determine the rigidity, and influence the life time of the spindle system. For small speed ranges, and low speed operation the different versions of a solid preload arrangement are suitable. Large speed range variances, and high speed spindles, require a systems that will not allow the bearing preload to be influenced by either temperature or speed. These applications require spring preloading of the bearings. The above mentioned arrangements cannot be adjusted or changed, without disassembling the spindle. With...
Open the catalog to page 6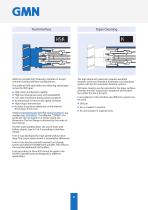
Tool Interface Taper Cleaning GMN can provide high frequency spindles to accept common tooling interface configurations. The high demand to precision requires excellent cleaness at the tool interface. Automatic tool changing system call also for automatic cleaning systems. The prefered HSK style offers the following advantages versus the ISO taper: u u u u u u ISO taper cleaning can be operated at the taper surfaces whereas the HSK request also treatment of the plane face when the size it accepts. High static and dynamic rigidity High tool change accuracy and repeatability Low axial...
Open the catalog to page 7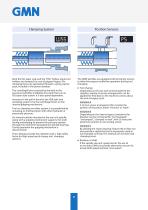
Clamping System Position Sensors Both the ISO taper style and the "HSK" hollow shank tool holders are clamped via a set of gripper fingers. The clamping forces are generated through a spring washer pack, included in the power drawbar. The GMN spindles are equipped with proximity sensors to allow for proper, trouble free operation during tool changing. u The centrifugal forces exerted by the balls in the pressure intensifier, multiplies the pull in force on an ISO taper style system. It is also speed dependent. Increases in the pull in force for the HSK style tool clamping system is by the...
Open the catalog to page 8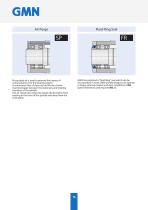
Fluid-Ring Seal GMN has patented a Fluid Ring seal which can be incorporated in most GMN spindle designs, can operate in heavy external coolant and dust conditions, is NO speed limitations, and requires NO air. Pressurized air is used to prevent the ingress of contamination into the bearing system. A continuous flow of clean dry air fills the closely machined gaps between the stationary and rotating members of the spindle. The air stream also stops the spent oil lubrication from existing at the front of the spindle and away from the work piece.
Open the catalog to page 9
Coolant Through Shaft Coolant Through Spindle Housing For cooling of tool and workpiece the medium is supplied through spindle housings and nozzels to the cutting surfaces. The internal coolant supply provides cooling directly to the cutting edge also at difficult form of workpieces. In accordance to the interface size and dependent on the maximum operating speed different systems can be used: Compressed air, cooling lubricant/air mixture or cooling lubricant can be used. The representation below is with cooling lubricant as medium. Only air u Air or coolant in one line u Air and coolant in...
Open the catalog to page 10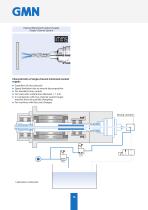
Internal Minimized Coolant Supply Single-Channel System Characteristics of single-channel minimized coolant supply: Superfine oil mist (aerosol) Speed limitation due to aerosol decomposition For standard rotary unions For tools with coolant bore diameter > 1 mm In comparison with two-channel system longer reaction times at quantity changings u For machines with less tool changes u u u u u Mixing chamber Lubrication schematic
Open the catalog to page 11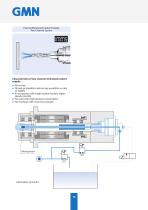
Internal Minimized Coolant Supply Two-Channel System Characteristics of two-channel minimized coolant supply: No oil mist Oil and air mixable in almost any quantities or only air supply u In comparison with single-channel system higher speeds possible u For tools with high lubricant consumption u For machines with more tool changes u u Mixing head Lubrication schematic
Open the catalog to page 12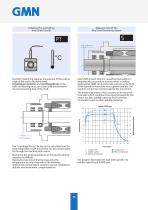
A Method For Controlling Axial Shaft Growth Measurement Of The Axial Shaft Growth By Sensor axial movement °C Axial shaft growth which is caused by fluctuations in temperature, can produce process errors in milling applications. GMN can incorporate a sensor at the front of the spindle to record the exact growth and the CNC machine control can compensate for the movement. The measuring system which consists of an electronic controller which conditions the signal provided by the sensor has data storage capacity which provides immediate response after spindle exchange. Precision machining...
Open the catalog to page 13All Kuroda Jena Tec Holdings Ltd catalogs and technical brochures
-
Ballscrew: Full Catalogue
23 Pages
-
End Support Catalogue
8 Pages
-
SPM – Special Purpose Spindles
99 Pages
-
Multi Head Spindle Catalogue
4 Pages
-
Linear Stages
138 Pages
-
Rotary Table Catalogue
4 Pages
-
Linear Actuators Catalogue
17 Pages
-
Main Precision Gauge Catalogue
48 Pages
-
SBG Standard Linear Rail System
13 Pages
-
SBI High-load Linear Rail System
11 Pages
-
Spindle
99 Pages
-
Support Units Catalog
8 Pages