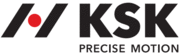

Operating Conditions for Transport, Handling, Assembly and Operation of Engineering Products of KSK Precise Motion, a.s.
1Pages
Catalog excerpts
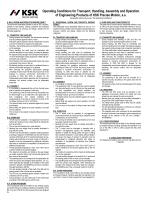
Operating Conditions for Transport, Handling, Assembly and Operation of Engineering Products of KSK Precise Motion, a.s. (hereinafter referred to only as “the Operating Conditions") A. BALL SCREW AND PRODUCTS DERIVED FROM IT The ball screw (hereinafter referred to only as “BS”) requires, similarly to ball bearing, working conditions and principles corresponding to its accuracy and design, divided into the following categories: A.I. TRANSPORT AND HANDLING • During transport and handling, the anticorrosive package must be protected against breach or wear • Protection against impacts must be provided (the nut body must not be strained by impacts and radial load) • Handling - the handling points are identified by pictograms on the packages • During handling, the shaft must be maintained with minimum bending from own weight; the distances between the supports during storage must correspond maximally to 1 /4 of the shaft length; vertical suspension of BSs with pretensioned nuts is allowed • Any inclination of non-pre-tensioned ball screws may cause unscrewing of the screw or the nut • BS stacking (putting on each other) in cardboard boxes or without solid wooden packages is not allowed • After removing the protective anticorrosive package consisting of Cortec VpCI-126 foil, the product must not be exposed to corrosive environment; environment C1 according to CSN ISO 9223 is allowed for the indispensable period before assembly into the equipment; otherwise, the product surface must be adequately preserved A.II. ASSEMBLY • It is forbidden to disassemble the nut from the ball screw shaft or interfere in the product in other way • The positioning of the Bs shaft axis must be parallel over the entire length in up to 0,02mm/m to the guide plain (in both longitudinal and vertical direction); the perpendicularity of the area of contact for the face of the nut flange must be up to 0,01 mm/100mm • The thread surface must be protected against dirt, liquids and damage • Before filling with grease and actual operation, the shaft must be cleaned • The nut must not be subject to impacts, tilting moment and radial load A.III. OPERATION • The BS must be operated in non-aggressive environment without dirt, liquids and dust, unless the BS is intended for such environment • The nut may be strained only in axial direction • Bending from own weight must be suitably eliminated in long and thin screws • The BS must be lubricated in operation (bearing greases according to degree 2 of DIN51825 and oils with minimum viscosity of 50mm2/s at 40°C); standard lubrication is lossmaking without filtration and reuse; losses of lubricant in operation must be compensated by additional lubrication with stress on verification of compatibility of lubricants from different manufacturers • The BS operating temperature is from -30 to +90°C and it is further limited by the lubricant applied • The maximum revolutions are limited by the gear design (so called revolution factor) and the lubricant applied and they must not be exceeded • The operating load must correspond to the specification for which the product was designed (load spectrum, Ca, Co), while respecting the strength of the material of the screw shaft (min. strength - Rm=600MPa) and of the nut condition (through-hardened to 60HRc) • The safe buckling strength of the shaft of the BS and the bearing power of the nut must not be exceeded • The BS must be protected against dynamic impacts and overloads over the Co value • During operation, only the useful path of the shaft thread according to ISO 3408 may be used for load A.IV. OTHER PROVISIONS The manufacturer shall not be liable for any damage caused by inexpert transport, handling, assembly and operation of the BS or by use of the BS for other purpose that it was designed for. B. TRAPEZOIDAL SCREW AND PRODUCTS DERIVED FROM IT The trapezoidal screw (hereinafter referred to only as “Tr”) requires working conditions and principles corresponding to its accuracy, function and design, divided into the following categories: B.I. TRANSPORT AND HANDLING • During transport and handling, the anticorrosive package must be protected against breach or wear • Protection against impacts must be provided for (the shaft and nut surfaces are soft) • Handling - the handling points are identified by pictograms on the packages • During handling, the shaft must be maintained with minimum bending from own weight; the distances between the supports during storage must correspond maximally to 1/4 of the shaft length; vertical suspension is allowed • Stacking (putting on each other) in cardboard boxes or without solid wooden packages is not allowed • After removing the protective anticorrosive package consisting of Cortec VpCI-126 foil, the product must not be exposed to corrosive environment; environment C1 according to CSN ISO 9223 is allowed for the indispensable period before assembly into the equipment; otherwise, the product surface must be adequately preserved B.II. ASSEMBLY • It is forbidden to interfere in the product • The positioning of the Tr screw shaft axis must be parallel over the entire length in up to 0,05mm/m to the guide plain (in both longitudinal and vertical direction); the perpendicularity of the area of contact for the face of the nut flange must be up to 0,02 mm/100mm • The thread surface must be protected against dirt, liquids and damage • Before filling with grease and actual operation, the shaft must be cleaned • The nut must not be subject to tilting moment and radial load B.III. OPERATION • The Tr screw must be operated in non-aggressive environment without dirt, liquids and dust, unless the screw is intended for such environment • The nut may be strained only in axial direction and it must be guided coaxially to the shaft • Bending from own weight must be suitably eliminated in long and thin screws • The Tr screw must be lubricated in operation with a lubricant non-aggressive against the materials used (greases or pastes for sliding guides and gear or sliding oils); standard lubrication is loss-making without filtration and reuse; the losses of lubricant in operation must be compensated by additional lubrication with stress on verification of compatibility of lubricants from different manufacturers • The operating temperature is from -30 to +90°C and it is further restricted by the lubricant applied and by the nut material • The maximum revolutions and the maximum sliding speed must not be exceeded • The safe buckling strength of the shaft of the T r screw and the bearing power of the nut must not be exceeded • The operating load must correspond to the specification for which the product was designed, while respecting the strength of the material of the screw shaft (min. strength -Rm=600MPa) and of the nut (usually CuSn8 or CuSn12) B.IV. OTHER PROVISIONS The manufacturer shall not be liable for any damage caused by inexpert transport, handling, assembly and operation or by use of the T r screw for other purpose that it was designed for. C. GUIDE RODS AND OTHER PRODUCTS The guide rods of circular section (hereinafter referred to only as “GR”) and other products (hereinafter referred to only as “OP”) require working conditions and principles corresponding to their accuracy, function and design, divided into the following categories: C.I. TRANSPORT AND HANDLING • During transport and handling of GRs and OPs, the package must be protected against breach or wear • During handling, the GRs must be maintained with minimum bending from own weight; the distances between the supports during storage must correspond maximally to 1/4 of the shaft length; vertical suspension is allowed • Stacking (putting on each other) in cardboard boxes or without solid wooden packages is not allowed • After removing the protective anticorrosive package consisting of Cortec VpCI-126 foil, the product must not be exposed to corrosive environment; environment C1 according to CSN ISO 9223 is allowed for the indispensable period before assembly into the equipment; otherwise, the product surface must be adequately preserved C.II. ASSEMBLY • It is forbidden to interfere in the product • The positioning of the GRs must be provided for in required accuracy according to the guide used and the relevant purpose • The product surface must be protected against dirt, liquids and damage C.III. OPERATION • The GRs and OPs screw must be operated in non-aggressive environment without dirt, liquids and dust, unless they are intended for such environment • Bending from own weight must be suitably eliminated in long and thin GRs (radial fixation of the rods) • The rolling friction guides used for GRs must be suitably lubricated during operation • The GR operating temperature is limited by the lubricant and the rolling friction guide used • The operating load must correspond to the specification for which the product was designed, while respecting the strength of the material of the GR (min. strength -Rm=600MPa) C.IV. OTHER PROVISIONS The manufacturer shall not be liable for any damage caused by inexpert transport, handling, assembly and operation or by use of the GRs or OPs for other purpose that they were designed for.
Open the catalog to page 1All KSK PRECISE MOTION catalogs and technical brochures
-
MINIATURE SALL SCREWS
12 Pages
-
Product catalogue
48 Pages