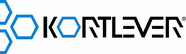
Catalog excerpts
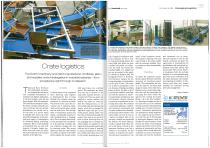
The Dutch machinery and plant manufacturer, Kortlever, plans and supplies crate intralogistics in industrial bakeries - from acceptance right through to dispatch. Technisch Buro Kortlever run business that has grown into a reputable manufacturer of machines and logistic applications in the food industry over the last three decades. With 85 employees, 30 in technical development alone, the Dutch company primarily ope- rates in Europe, but also abroad. its own staff, as is service which diversified programme is the plan- ning and supply of intralogistics in industrial baking technology companies. This is a real challenge as production lines can only work properly if doughs, bakery pro- ducts, trays and crates are availa- quantity at the right time. A central aspect to be considered when planning crate logistics is optimising the flow of crates through the company using the minimum of resources possible. The priority in this case is the eco- nomical use of operating equip- ment and resources, space, energy and the work force. The develop- ment of automation systems has meant a considerable reduction in staff, including those in intralogi- stics. This is an aspect that Kortle- ver has also taken into considerati- on in its planning. Generally, just one employee manages the line for receiving crates. This person makes sure that the crates stacked on trolleys are placed in the buffer which supplies the onward system with used crates over a defined period. The containers are taken stack when required and fed to a conveyor belt. These are swept and emptied to remove residues and prepare the crates for cleaning. After the rinsing process, a com- puter-aided requirements planning system, which has an integrated, regulated supply and jam moni- toring system, decides which way the crates will proceed through the system. One route is via conveyor belts to those receiving them on the packaging line in production, where baskets are supplied on the signal from the product and loaded with the aid of robots. If supplied in excess, the baskets are directed into a buffer where they are stored in the smallest stacking space pos- Company profile Packaging/Logistics [11 To place the opening of the Broban crates in the right position, Kortlever has installed a 180 degree turning device in the machines. [2] Stacked crates are conveyed to the next station by means of 90 degree transfer. [3] The Dutch machi- nery and plant manufacturer has also developed the right applications for more complex requirements, such as a sorting a. id rinsing system for three types of crates. sible. If supply is insufficient, addi- tional containers are fed in from the crate stack storage system. The c ates filled with goods are then r-istacked and placed on trolleys. Cnce the stack has reached the s jecified height, it is singled out ble vehicles by dispatch staff. The Managing Director of Kortlever, lowing advantages of intralogistics f om his point of view: „The custo- core business of baking and selling l akery products. We take on all of t le processes needed in crate logi- stics with the systems we install - from planning to maintenance and staff training - thereby relieving forming these tasks. We construct £ customised application suited to the space available from standardi- sed tried and tested modules. This means pallets can also be used as i means of transport that can be (onveyed, stacked and unstacked like trolleys. For many bakeries, i product change from whole loa- ves to half loaves of bread is also important. Kortlever even has a . olution in its portfolio for this situation. If required, the machi- nery and plant manufacturer can install visual inspection points. This includes checking if the clip seals the bag, or the crates comply with the necessary standard. Faul- ty products are then automatically To ensure the customers receive the best advice Kortlever staff first document all important project details. This information will ser- ve as the basis for an initial draft design or layout. Upon order entry, Korlever puts a project team toge- ther that will be responsible for executing the order within the agreed term. During all project phases - up to the final installati- her team will act as the mediator between customer and engineering making sure of smooth communi- cation. Customised applications are developed by design engineers in tool engineering and electro- nics with the aid of 3D drawings or electronics diagrams, based on Siemens S7 control systems. In the process, the option of wet cleaning is given top priority in terms of the selection of components and type of design. Before being delivered, customers can come to the factory and make sure that the machines ded and properly on site. In this respect, customers are given the opportunity of checking that all pulations have been upheld. This documented FAT process (Facto- ry Acceptance Test) also includes creation of a recommended spare parts list, proper evaluation of all the topics discussed, and installa- tion planning. In addition to this, Service and Sales also remain available for customers during after-sales management. Gregor Vogelpohl your innovating partner in food processing equipment and logistics Technisch Buro Year founded: Managing Director: Company site:
Open the catalog to page 1All Kortlever (Technisch Buro Kortlever B.V.) catalogs and technical brochures
-
Rheon Twin Divider
1 Pages