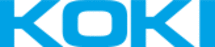

Catalog excerpts
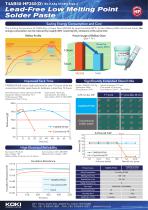
Lead-Free Low Melting Point Solder Paste Saving Energy Consumption and Cost The melting temperature of T4AB alloy is lower than SAC305 by approximately 80ºC. As the reflow profile can be set lower, the energy consumption can be reduced by roughly 40%, lowering CO2 emissions at the same time. Reflow Profile Power Usage of Reflow Oven (per 1 hr.) 240ºC Significantly Extended Stencil Idle Improved Tack Time T4AB58-HF360 retains high tackiness for over 72 hours while the conventional solder paste loses its tackiness in less than 72 hours. Stencil thickness: 0.2mm (aperture 6.5mmΦ) Equipment: Malcom tackimeter TK-1 Probe pressure: 50gf Measurement time: 0.2 sec. Probe speed: 10mm/sec. Test standard: JIS Z 3284-3 Test ambient: 25±1ºC, 50±10%RH Printer: YAMAHA YVP-Xg Squeegee: Metal Print pressure: 50 N Conventional solder paste T4AB58-HF360 High Electrical Reliability Test board: IPC-B-25 Bias voltage: 10V Reflow profile: As shown on the above Test chamber: 65ºC, 88.5%RH Measurement voltage: 100V Insulation Resistance Stencil thickness: 0.12 mm Print speed: 40 mm/sec. Test ambient: 25±1˚C, 50±10%RH Product name Alloy Composition Flux Type Halide Content (%) Flux Content (%)
Open the catalog to page 1All Koki Company Limited catalogs and technical brochures
-
S3X58-CF100-2
1 Pages
-
SB6N58-500SI
1 Pages
-
JM-20
1 Pages
-
JS series
1 Pages
-
SE/SS series
1 Pages