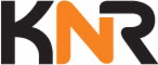
Catalog excerpts
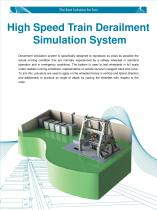
High Speed Train Derailment Simulation System Derailment simulation system is specifically designed to reproduce as close as possible the actual running condition that are normally experienced by a railway wheelset in standard operation and in emergency conditions. The system is used to test wheelsets in full scale under realistic running conditions, representative of vehicle service in tangent track and curve. To aim this, actuators are used to apply on the wheelset forces in vertical and lateral direction, and additionally to produce an angle of attack by yawing the wheelset with respect to the roller.
Open the catalog to page 1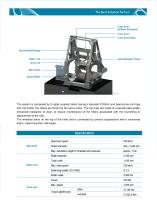
The Best Solution forTest Cross head Up/Down ScrewJack Cross head Cross head Clamp Latera Actuator Fixture Drive unit Main Frame Seismic Mass The system is composed by 2 rigidly coupled rollers having a diameter 2100mm and bearing two rail rings with rail profile; the rollers are driven by AC servo-motor. The rail rings are made of a special steel grade, enhanced resistance to wear, to reduce maintenance of the rollers associated with the re-profiling or replacement of the rails. The wheelset leans on the top of the roller and is connected by primary suspensions with a transverse beam,...
Open the catalog to page 2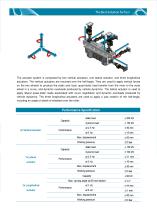
The actuator system is composed by two vertical actuators, one lateral actuator, and three longitudinal actuators. The vertical actuators are mounted over the half-bogie. They are used to apply vertical forces on the two wheels to produce the static axle load, quasi-static load transfer from the inner to the outer wheel in a curve, and dynamic overloads produced by vehicle dynamics. The lateral actuator is used to apply lateral quasi-static loads associated with curve negotiation and dynamic overloads produced by vehicle dynamics. The three longitudinal actuators are used to apply a yaw...
Open the catalog to page 3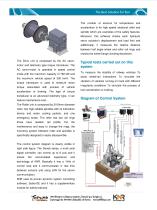
The Best Solution for Test The Drive unit is composed by the AC servomotor and telemetry type torque transducer. The AC servo-motor is operated in speed control mode with the maximum capacity of 762 kW and the maximum vehicle speed of 330 km/h. The torque transducer is used to measure motor torque associated with process of vehicle acceleration or braking. The type of torque transducer is an advanced telemetry type, it can reduce maintenance cost. The Roller unit is composed by 2100mm diameter roller, two high reliable spindles with oil lubrication device and water cooling jackets, and...
Open the catalog to page 4All KNR system catalogs and technical brochures
-
6 DOF shake table
5 Pages
-
Servo Valve
8 Pages
-
Multi Axes Shaking Table
5 Pages