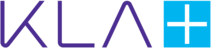

Catalog excerpts
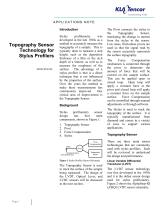
encor Accelerating Yield APPLICATIONS NOTE Topography Sensor Technology for Stylus Profilers Attila Sirovita Introduction Stylus profilometry was developed in the late 1920s as a method to accurately measure the topography of a sample. This is typically done to measure a step height, such as the deposition thickness of a film or the etch depth of a feature, as well as to measure the roughness of the surface. The advantage of a stylus profiler is that is a direct technique that is not influenced by the properties of the surface. Over the years the method to make these measurements has continuously improved. One critical area of improvement is the Topography Sensor. Background Stylus profilometry sensor design has four main components, shown in Figure 1: The Topography Sensor is used to track the surface of the sample being measured. The design of the LVDT, Optical Lever, and LVDC sensors will be discussed in the next section. The Pivot connects the stylus to the Topography Sensor, translating the change in motion from the stylus to the sensor. Low mass, frictionless pivots are used so that the signal read by the sensor accurately represents the surface topography. The Force Compensation mechanism is connected through the pivot to determine the amount of force that will be exerted on the sample surface. This can be applied open or closed loop. Open loop will apply a constant force at the pivot and closed loop will apply a constant force on the sample surface. Force Compensation can be controlled through manual adjustments or through software. The Stylus is used to track the topography of the surface. It is typically manufactured from diamond and comes in a variety of sizes to support various applications. Topography Sensor There are three main sensor technologies that are commonly used with stylus profilers. Each will be reviewed to understand the design and performance. Linear Variable Differential Transducer (LVDT) The LVDT sensor technology was first developed in the 1930s and it is the oldest sensor design used for stylus profilometry. Figure 2 shows the AlphaStep-IQ (ASIQ) LVDT sensor schematic.
Open the catalog to page 1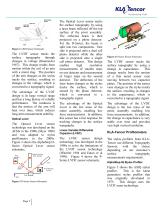
Accelerating Yield The LVDT sensor tracks the surface topography through changes in voltage (Baumeister 1967). This change results from motion within the coil of an arm with a metal slug. The position of the arm changes as the stylus tracks the surface, resulting in changes in the voltage, which is converted to a topography signal. The advantage of the LVDT design is its large vertical range and has a long history of reliable performance. The weakness is that the motion of the arm will heat over time, which reduces long-term measurement stability. Optical Lever The Optical Lever...
Open the catalog to page 2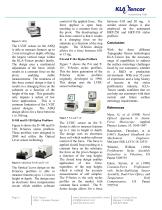
Accelerating Yield Figure 5 ASIQ The LVDT sensor on the ASIQ is able to measure features up to 2 mm in height or depth, offering the largest vertical range within the KLA-Tencor product family. The design uses a mechanical adjustment of the force, which results in a constant force on the pivot, enabling stable measurements. The weakness of this force control design is that it results in a changing force on the substrate as a function of the height of the step. This generally only impacts a subset of low force applications. This is a common limitation of the LVDT sensor designs. The...
Open the catalog to page 3All KLA Corporation catalogs and technical brochures
-
2935
1 Pages
-
2950 EP
1 Pages
-
2965
1 Pages
-
8930
1 Pages
-
Axion® T2000
1 Pages
-
Surfscan® SP7XP
4 Pages
-
P-7 Stylus Profiler
2 Pages
-
ICOS™ T3/T7
4 Pages
-
ICOS™ T890
4 Pages
-
SensArray
8 Pages
-
P-17 Stylus Profiler
2 Pages
-
Archer 100
2 Pages
-
MicroXAM - 800
4 Pages