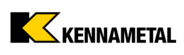

Catalog excerpts
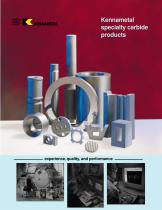
finding better ways Kennametal specialty carbide products experience, quality, and performance
Open the catalog to page 1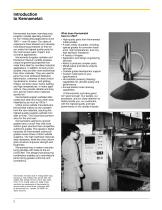
Kennametal has been manufacturing tungsten carbide specialty products for non-metalcutting applications since 1940 — over 50 years. Our years of experience have allowed us to develop manufacturing processes so that we can make the highest quality parts for the most severe wear, impact, and corrosive applications. Kennametal tungsten carbides and Kentanium titanium carbide possess unique engineering properties that make them ideal for countless industrial applications. In addition to being more durable, they are often more economical than other materials. They are used for parts that must...
Open the catalog to page 2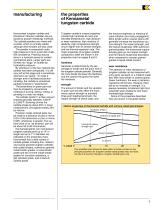
the properties of Kennametal tungsten carbide Kennametal tungsten carbide and Kentanium (titanium carbide) are produced by powder metallurgy methods. The carbide powders are mixed with a binder, which is normally cobalt, although other binders are also used. The powder is compacted under high pressure to form a part with chalklike consistency. Pressing may be done in a hydraulic press for smaller symmetrical parts. Larger parts are formed into “slugs’’ of carbide by hydrostatic pressure. By whichever of the two methods the carbide has been compacted, it is still very soft at this stage and...
Open the catalog to page 3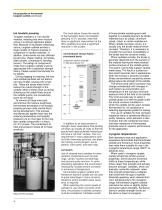
the properties of Kennametal tungsten carbide (continued) hot isostatic pressing Tungsten carbide is a “non-ductile’’ material, meaning that when fracture occurs it is without significant plastic flow. Because of its powder metallurgy nature, tungsten carbide exhibits a larger scatter of fracture stresses in comparison to ductile materials. In addition, stress levels are also affected by part size, shape, loading, and stress state (tensile, compressive, bending, torsion). The design of components made from tungsten carbide must be approached from a statistical strength theory. Please...
Open the catalog to page 4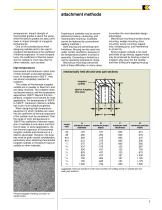
attachment methods temperatures. Impact strength of Kennametal grades is about the same, while Kentanium grades are about 20% lower in impact strength at cryogenic temperatures. One of the considerations when designing carbide parts to be used in cryogenic temperatures is the coefficient of thermal expansion. At room temperatures, the coefficient of thermal expansion for carbide is much less than for other materials, such as steel. high temperatures Kennametal and Kentanium retain most of their strength at elevated temperatures. At temperatures to 600°F., they are almost completely...
Open the catalog to page 5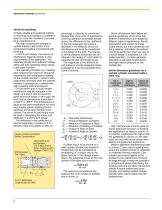
attachment methods (continued) shrink fit mounting A highly reliable and preferred method of mounting round sections of carbide in steel is to size the members to provide for an interference fit. The high compressive strength of carbide makes it well suited to the compressive loading encountered with shrinking. In shrink joint design, the amount of interference depends entirely on the requirements of the application. The assembly should have sufficient holding ability and safe operating stress values in the outer member. One operating condition (i.e., heading dies) requires the maximum...
Open the catalog to page 6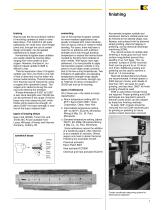
brazing Brazing was the first successful method of mounting carbides to steel or other base alloys. This method is still quite satisfactory for small-area, short-length joints and, through the use of certain design principles, can be applied satisfactorily to larger joints. Kennametal tungsten base carbides are readily wetted by brazing alloys ranging from silver solder to pure copper. However, Kentanium, our titanium based carbide K162B is difficult to wet. Thermal expansion rates of tungsten carbide vary from one-third to one-half of that of steel and must be taken into account when...
Open the catalog to page 7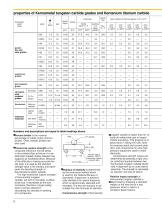
properties of Kennametal tungsten carbide grades and Kentanium titanium carbide Kennametal grade series specific heat mean coefficient of themal expansion x 10–6 in/in/°F density thermal Btu/hr • ft • °F specific weight electrical % of copper standard room room room temp temp temp to 400°F to 750°F to 1200°F titanium carbide carbon steel tool steel AISI T-series stainless steel punch, die, and wear grades submicron grades gall resistant grade corrosionwear resistant grades Kentanium reference materials Ni binder Cr-Co binder Numbers and descriptions are keyed to table headings above....
Open the catalog to page 8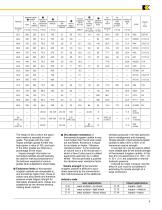
transverse rupture 2 strength 7 fracture endurance 4 modulus of abrasion toughness 5 elasticity compressive Poisson’s limit resistance ASTM 90% (resonance strength ratio relative (rotating mean reliability method) factor B771-87 (resonance impact beam) method) resistance 1 x 103 psi x 103 psi x 103 psi x 106 psi x 103 psi MPa! m (108 cycles) vol loss w hot hot hardness compressive modulus of at yield rigidity 1400°F strength psi at 1600°F Rockwell A AISI T-series The height of fall at which the specimen breaks is recorded for each grade. The grade with the most impact strength (grade K3109)...
Open the catalog to page 9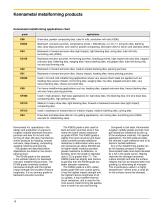
Kennametal metalforming products Kennametal metalforming applications chart grade Draw dies, powder compacting dies, tube fin rolls, sendzimer mill rolls (KZ96). Backward extrusion punches, compressive stress > 300,000 psi, or L:D>7:1, extrusion dies, blanking dies, draw wipe punches, core rods for powder compacting, lamination dies for silicon and stainless steels. Backward or forward extrusion dies (light impact), light blanking dies, sizing dies, tube mill rolls, burnishing rolls (KZ94). Backward extrusion punches, hot forming punches, heading punches, high impact extrusion dies, trapped...
Open the catalog to page 10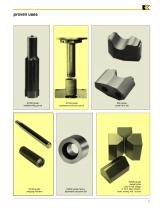
proven uses K3109 grade metalforming punch K3109 grade swaging mandrel K3109 grade backward extrusion punch K3520 grade heavy backward extrusion die K3520 grade swaging die used to hot swage or form steel chisels, tools, tubing, rod...to size
Open the catalog to page 11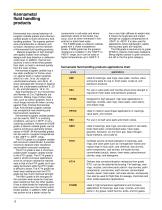
Kennametal fluid handling products Kennametal has a broad selection of tungsten carbide grades and a titanium carbide grade to solve almost any fluid handling problem. The superior performance characteristics in abrasion and corrosion resistance are the hallmark of Kennametal fluid handling products. Material properties of high strength and rigidity enable more compact designs with less distortion or deflection under load. In addition, thermal conductivity is two to three times greater than steel, so heat is removed quickly from the wear surface. Kennametal tungsten carbide has a low static...
Open the catalog to page 12All Kennametal catalogs and technical brochures
-
CB11 Stack-On
2 Pages
-
Grinder Tips
16 Pages
-
Grader Blades
40 Pages
-
Road Rehabilitation • Road King
24 Pages
-
Underground Mining
182 Pages
-
ROCTEC ecoline
1 Pages
-
Conforma Clad X2™
2 Pages
-
INNOVATIONS 2020
84 Pages
-
INNOVATIONS 2019
156 Pages
-
Tooling Systems News 2018
60 Pages
-
Oilfield Radial Bearings
2 Pages
-
Cladding Formulas Oilfield
2 Pages
-
General Conveyance Equipment
4 Pages
-
Twin-Screw
2 Pages
-
EDM Blocks Brochure
8 Pages
-
KMT_Wear Solutions_Brochure
12 Pages
-
Alloys Brochure Direct
28 Pages
-
Kennametal Stellite Alloys
15 Pages
-
Composite Rods
1 Pages
-
Fluidized Bed Boiler Tubes
1 Pages
-
Mill Roll Brochure
8 Pages
-
Snowplow Blades
1 Pages
-
KenCast Wear Protection
20 Pages
-
7690VA09
3 Pages
-
Tool Selection
3 Pages
-
Indexable Milling Index
8 Pages
-
Milling geometries quick
9 Pages
-
Milling grades
4 Pages
-
Tooling Systems 2013 Catalog Sections
1576 Pages
-
INNOVATIONS CATALOGUE 2015
260 Pages
-
Kennametal Innovations 2014
630 Pages
-
KMT KBH20 metric
18 Pages
-
Master Catalog 2013 Complete - metric
2122 Pages
-
Railroad Brochure
24 Pages
-
Abrasive Blast Nozzles Catalog
60 Pages
-
Surface Mining Catalog
42 Pages
-
Holemaking Taps (metric)
118 Pages
-
Threading
108 Pages
-
O.D. / I.D. Toolholders
162 Pages
-
PCD / PCBN Inserts
66 Pages
-
ISO / ANSI Inserts
132 Pages
-
Thread Mills
20 Pages
-
Copy Mills
118 Pages
-
Slotting Cutters
56 Pages
-
Shoulder Mills
96 Pages
-
Face Mills
138 Pages
-
Solid End Milling
118 Pages
-
Taps
194 Pages
-
Hole Finishing
214 Pages
-
Indexable Drills
108 Pages
-
Combination Tools
28 Pages
-
Modular Drills
62 Pages
-
Solid Carbide Drills
112 Pages