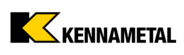

Catalog excerpts
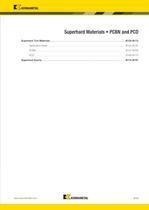
KM_Master12_Turning_B132_B133_Minch.qxp:Layout 1 3/2/12 3:16 PM Page B133 Superhard Materials • PCBN and PCD Superhard Tool Materials . . . . . . . . . . . . . . . . . . . . . . . . . . . . . . . . . . . . . . . . . . . . . . . . . . . . . . . . .B132–B173 Application Areas . . . . . . . . . . . . . . . . . . . . . . . . . . . . . . . . . . . . . . . . . . . . . . . . . . . . . . . . . . .B134–B135 PCBN . . . . . . . . . . . . . . . . . . . . . . . . . . . . . . . . . . . . . . . . . . . . . . . . . . . . . . . . . . . . . . . . . . . .B137–B163 PCD . . . . . . . . . . . . . . . . . . . . ....
Open the catalog to page 2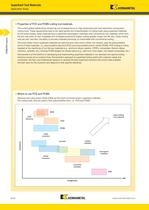
Superhard Tool Materials Application Areas ■ Properties of PCD and PCBN cutting tool materials The current global metalcutting climate has put increased focus on high productivity and cost reductions coming from cutting tools. These requirements lead to the rapid growth and implementation of cutting tools using superhard materials. As the name implies, these materials have a significant advantage in hardness over conventional tool materials, which from the end user point of view, translates into increased productivity (higher cutting speeds, longer tool life, etc.), lower tooling r cost per...
Open the catalog to page 3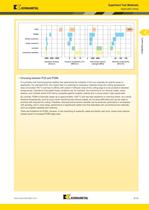
Superhard Tool Materials Application Areas nitride ceramics . oxide ceramics . cemented carbides . hardness Vickers transverse rupture thermal conductivity i Choosing between PCD and PCBN It is primarily their thermochemical stability that determines the suitability of the two materials for specific areas of application. For standard PCD, this means that it is restricted to workpiece materials where the cutting temperature does not exceed 700 °C and has no affinity with carbon if diffusion wear of the cutting edge is to be avoided at elevated temperatures. Operations that satisfy these...
Open the catalog to page 4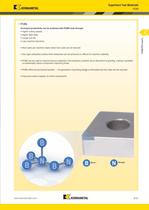
Superhard Tool Materials Increased productivity can be achieved with PCBN tools through: • Higher cutting speeds. • Higher feed rates. • Longer tool life. • Less machine downtime. • More parts per machine means direct tool costs can be reduced. • Very tight workpiece surface finish tolerances can be achieved on difficult-to-machine materials. • PCBN can be used to machine ferrous materials in the hardened condition as an alternative to grinding, making it possible to substantially reduce component machining times. • PCBN offers environmental benefits — the generation of grinding sludge is...
Open the catalog to page 6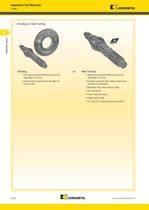
Superhard Tool Materials Grinding vs. Hard Turning • Size tolerance specifications beyond the • Surface finish requirements too tight for hard turning. • Size tolerance specifications beyond the • Complex geometry that makes single-point turning more practical. • Relatively high metal removal rates. • Faster machine setup. • Faster cycle times.
Open the catalog to page 7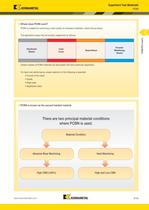
Superhard Tool Materials ■ Where does PCBN work? PCBN is suitable for machining a wide variety of workpiece materials, mainly ferrous alloys. The application areas may be broadly categorized as follows: Certain classes of PCBN materials are associated with each particular application. For best cost performance, proper selection of the following is essential: • Edge prep. • Application data. PCBN is known as the second hardest material There are two principal material conditions where PCBN is used. Material Condition Abrasive Wear Machining Hard Machining
Open the catalog to page 8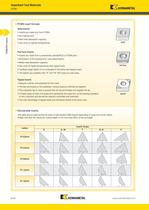
Superhard Tool Materials PCBN insert formats Solid Inserts • Inserts are made only from PCBN. r • Best heat absorption capacity. can work at highest temperatures. solid " Full-Face Inserts • Inserts are made from a presintered carbide/PCD or PCBN joint. • Elimination of the brazing joint. Less delamination. • Better heat absorption capacity. • Can work at higher temperatures than tipped tools. full-face • Facilitate larger depth of cut compared to the same size tipped insert. • The blanks are available with "A" and "W" ISO-style pin-lock holes. Tipped Inserts • Require a carrier and...
Open the catalog to page 9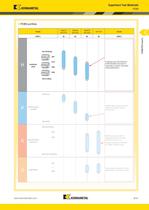
Superhard Tool Materials PCBN portfolio fine finishing hard milling Toughness and wear behaviors moderately to heavily interrupted cutting applications. sintered irons KB5630 offers extreme abrasion resistance for highly alloyed sintered irons. cast irons general machining toughness behavior for rough machining of cast irons. for chilled, hardened Irons. These grades compliment turning applications In superalloy turning.
Open the catalog to page 10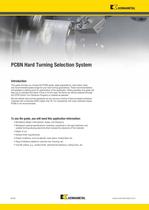
PCBN Hard Turning Selection System This guide will help you choose the PCBN grade, edge preparations, nose radius, feed, and recommended speed range for your hard turning applications. These recommendations will establish a starting point for optimization of the application. Where possible, this guide will lead you to standard line items. If this is not the case, the items can still be obtained through the QTSP (Quick-Turn Solutions Program) or ordered as specials. We will classify hard turning operations as any turning or boring of ferrous-based workpiece materials with a hardness (HRC)...
Open the catalog to page 11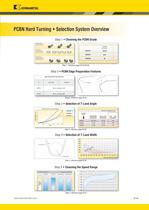
PCBN Hard Turning • Selection System Overview Step 1 • Choosing the PCBN Grade Step 1, reference pages B144-B145. Step 2 • PCBN Edge Preparation Features Step 2, reference page B145. Step 3 • Selection of T-Land Angle Step 3, reference page B145. Step 4 • Selection of T-Land Width Step 4, reference page B146. Step 5 • Choosing the Speed Range Step 5, reference page B147.
Open the catalog to page 12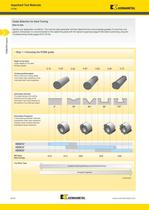
Superhard Tool Materials Grade Selection for Hard Turning Identify your application conditions. The most far right parameter will then determine the recommended grade(s). If more than one grade is intersected, it is recommended to first select the grade with the highest toughness (page B139) before optimizing using the Troubleshooting Guide (pages B142-B143). Step 1 • Choosing the PCBN grade Larger depths of cut need stronger grades. More continuous cutting needs more crater wear resistance; more interrupts need more toughness. Interruption Severity The angle between the cutting the...
Open the catalog to page 13All Kennametal catalogs and technical brochures
-
CB11 Stack-On
2 Pages
-
Grinder Tips
16 Pages
-
Grader Blades
40 Pages
-
Road Rehabilitation • Road King
24 Pages
-
Underground Mining
182 Pages
-
ROCTEC ecoline
1 Pages
-
Conforma Clad X2™
2 Pages
-
INNOVATIONS 2020
84 Pages
-
INNOVATIONS 2019
156 Pages
-
Tooling Systems News 2018
60 Pages
-
Oilfield Radial Bearings
2 Pages
-
Cladding Formulas Oilfield
2 Pages
-
General Conveyance Equipment
4 Pages
-
Twin-Screw
2 Pages
-
EDM Blocks Brochure
8 Pages
-
KMT_Wear Solutions_Brochure
12 Pages
-
Alloys Brochure Direct
28 Pages
-
Kennametal Stellite Alloys
15 Pages
-
Composite Rods
1 Pages
-
Fluidized Bed Boiler Tubes
1 Pages
-
Mill Roll Brochure
8 Pages
-
Snowplow Blades
1 Pages
-
KenCast Wear Protection
20 Pages
-
7690VA09
3 Pages
-
Tool Selection
3 Pages
-
Indexable Milling Index
8 Pages
-
Milling geometries quick
9 Pages
-
Milling grades
4 Pages
-
Specialty Carbide Catalog
16 Pages
-
Tooling Systems 2013 Catalog Sections
1576 Pages
-
INNOVATIONS CATALOGUE 2015
260 Pages
-
Kennametal Innovations 2014
630 Pages
-
KMT KBH20 metric
18 Pages
-
Master Catalog 2013 Complete - metric
2122 Pages
-
Railroad Brochure
24 Pages
-
Abrasive Blast Nozzles Catalog
60 Pages
-
Surface Mining Catalog
42 Pages
-
Holemaking Taps (metric)
118 Pages
-
Threading
108 Pages
-
O.D. / I.D. Toolholders
162 Pages
-
ISO / ANSI Inserts
132 Pages
-
Thread Mills
20 Pages
-
Copy Mills
118 Pages
-
Slotting Cutters
56 Pages
-
Shoulder Mills
96 Pages
-
Face Mills
138 Pages
-
Solid End Milling
118 Pages
-
Taps
194 Pages
-
Hole Finishing
214 Pages
-
Indexable Drills
108 Pages
-
Combination Tools
28 Pages
-
Modular Drills
62 Pages
-
Solid Carbide Drills
112 Pages