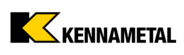

Catalog excerpts
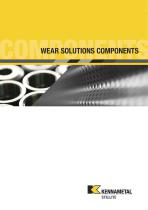
Wear Solutions Components Subheader COMPONENTS WEAR SOLUTIONS COMPONENTS
Open the catalog to page 1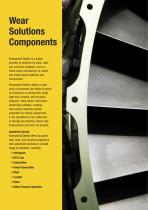
Kennametal Stellite is a global provider of solutions for wear, heat, and corrosion problems, and is a world-class manufacturer of cobalt-and nickel-based materials and components. Kennametal Stellite utilizes a wide array of processes and alloys to assist its customers in solving their tough high-heat, erosion, and corrosion problems. Solid cobalt- and nickel-based alloy castings, coatings, and overlay materials provide protection for critical components in the operations of our customers in virtually all industries where high temperatures and wear are present. Industries Served Kennametal...
Open the catalog to page 2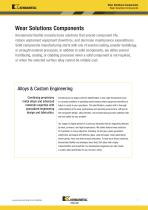
Wear Solutions Components Wear Solutions Components Wear Solutions Components Kennametal Stellite manufactures solutions that extend component life, reduce unplanned equipment downtime, and decrease maintenance expenditures. Solid components manufacturing starts with one of several casting, powder metallurgy, or wrought material processes. In addition to solid components, we utilize several hardfacing, coating, or cladding processes when a solid component is not required, or when the selected surface alloy cannot be reliably cast. Alloys & Custom Engineering Combining proprietary metal...
Open the catalog to page 3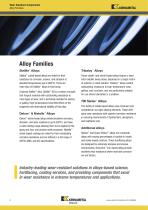
Wear Solutions Components Alloy Families Stellite™ Alloys Stellite™ cobalt-based alloys are noted for their resistance to corrosion, erosion, and abrasion at elevated temperatures (up to 800°C). There are more than 20 Stellite™ alloys in this family. A special Stellite™ alloy: Stellite™ 6B is a custom wrought (hot forged) material with outstanding resistance to most types of wear, and is extremely resistant to seizing or galling. High temperatures have little effect on the toughness and dimensional stability of this alloy. Deloro™ & Nistelle™ Alloys Deloro™ nickel-based alloys exhibit...
Open the catalog to page 4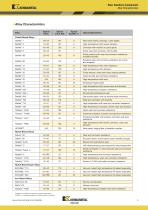
Wear Solutions Components Alloy Characteristics ULTIMET® is a registered trademark of Haynes International. ICONEL® is a registered trademark of Special Metals Corporation. KENNAMETAL
Open the catalog to page 5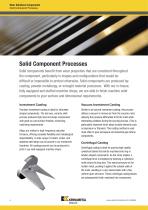
Wear Solutions Components Solid Component Processes Solid Component Processes Solid components benefit from wear properties that are consistent throughout the component, particularly in shapes and configurations that would be difficult or impossible to protect otherwise. Solid components are produced by: casting, powder metallurgy, or wrought material processes. With our in-house, fully equipped and staffed machine shops, we are able to finish machine solid components to your surface and dimensional requirements. Investment Casting Precision investment casting is ideal for...
Open the catalog to page 6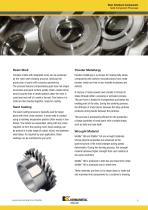
Wear Solutions Components Solid Component Processes Resin Shell Complex molds with integrated cores can be produced by the resin shell molding process, allowing the production of parts with complex geometries. The process features comparatively good near-net-shape accuracies and good surface quality. Resin-coated zircon sand is poured onto a heated pattern plate; the resin is cured and one half of a mold is formed. Two halves of a mold are then bonded together, ready for casting. Sand Casting The sand casting process is typically used for larger parts with thick cross sections. A sand mold...
Open the catalog to page 7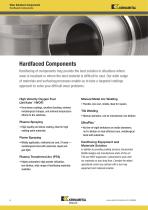
Wear Solutions Components Hardfaced Components Hardfaced Components Hardfacing of components may provide the best solution in situations where wear is localized or where the best material is difficult to cast. Our wide range of materials and surfacing processes enable us to take a targeted coatings approach to solve your difficult wear problems. High Velocity Oxygen Fuel (Jet Kote™ HVOF) • Very dense coatings, excellent bonding, minimal metallurgical changes, and minimal temperature effects to the substrate. Plasma Spraying • High-quality and dense coating, ideal for high melting-point...
Open the catalog to page 8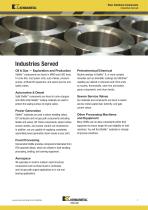
Wear Solutions Components Industries Served Industries Served Oil & Gas — Exploration and Production Stellite™ components are found in MWD and LWD tools, tri-cone bits, mud pulser units, auto chokes, pressure pumps, artificial lift equipment, and severe service and safety valves. Automotive & Diesel Solid Stellite™ components are found in turbo-chargers and EGRs while Stellite™ coating materials are used to protect the sealing surface of engine valves. Power Generation Stellite™ materials are used in steam handling valves, IGT combustor and hot gas path components (including blades and...
Open the catalog to page 9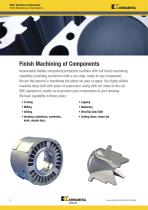
Wear Solutions Components Finish Machining of Components Finish Machining of Components Kennametal Stellite component production facilities offer full finish-machining capability, providing customers with a one-stop, ready-to-use component. We are the experts in machining the alloys we pour or apply. Our highly skilled machine shop staff with years of experience, along with our state-of-the-art CNC equipment, enable us to produce your components to your drawing. We have capability in these areas: • Turning • Milling • Grinding (cylindrical, centerless, knife, double disc) • Cutting (laser,...
Open the catalog to page 10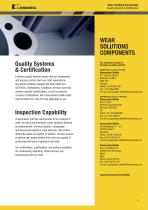
Wear Solutions Components Quality Systems & Certification WEAR SOLUTIONS COMPONENTS Quality Systems & Certification Extensive quality systems assure that our components and process control meet your high expectations. Our various facilities maintain ISO 9001:2008 and AS 9100:C certifications. In addition, we hold numerous industry-specific qualifications, as well as specific customer certifications. Ask a Kennametal Stellite sales representative for a list of those applicable to you. Inspection Capability In accordance with the requirements of our customer’s order, we verify and document a...
Open the catalog to page 11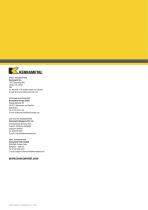
KENNAMETAL WORLD HEADQUARTERS Kennametal Inc. 1600 Technology Way Latrobe, PA 15650 USA Tel: 800.446.7738 (United States and Canada) E-mail: ftmill.service@kennametal.com EUROPEAN HEADQUARTERS Kennametal Europe GmbH Rheingoldstrasse 50 CH 8212 Neuhausen am Rheinfall Switzerland Tel: 41.52.6750.100 E-mail: neuhausen.info@kennametal.com ASIA-PACIFIC HEADQUARTERS Kennametal Singapore Pte. Ltd. 3A International Business Park Unit #01-02/03/05, ICON@IBP Singapore 609935 Tel: 65.6265.9222 E-mail: k-sg.sales@kennametal.com INDIA HEADQUARTERS Kennametal India Limited 8/9th Mile, Tumkur...
Open the catalog to page 12All Kennametal catalogs and technical brochures
-
CB11 Stack-On
2 Pages
-
Grinder Tips
16 Pages
-
Grader Blades
40 Pages
-
Road Rehabilitation • Road King
24 Pages
-
Underground Mining
182 Pages
-
ROCTEC ecoline
1 Pages
-
Conforma Clad X2™
2 Pages
-
INNOVATIONS 2020
84 Pages
-
INNOVATIONS 2019
156 Pages
-
Tooling Systems News 2018
60 Pages
-
Oilfield Radial Bearings
2 Pages
-
Cladding Formulas Oilfield
2 Pages
-
General Conveyance Equipment
4 Pages
-
Twin-Screw
2 Pages
-
EDM Blocks Brochure
8 Pages
-
Alloys Brochure Direct
28 Pages
-
Kennametal Stellite Alloys
15 Pages
-
Composite Rods
1 Pages
-
Fluidized Bed Boiler Tubes
1 Pages
-
Mill Roll Brochure
8 Pages
-
Snowplow Blades
1 Pages
-
KenCast Wear Protection
20 Pages
-
7690VA09
3 Pages
-
Tool Selection
3 Pages
-
Indexable Milling Index
8 Pages
-
Milling geometries quick
9 Pages
-
Milling grades
4 Pages
-
Specialty Carbide Catalog
16 Pages
-
Tooling Systems 2013 Catalog Sections
1576 Pages
-
INNOVATIONS CATALOGUE 2015
260 Pages
-
Kennametal Innovations 2014
630 Pages
-
KMT KBH20 metric
18 Pages
-
Master Catalog 2013 Complete - metric
2122 Pages
-
Railroad Brochure
24 Pages
-
Abrasive Blast Nozzles Catalog
60 Pages
-
Surface Mining Catalog
42 Pages
-
Holemaking Taps (metric)
118 Pages
-
Threading
108 Pages
-
O.D. / I.D. Toolholders
162 Pages
-
PCD / PCBN Inserts
66 Pages
-
ISO / ANSI Inserts
132 Pages
-
Thread Mills
20 Pages
-
Copy Mills
118 Pages
-
Slotting Cutters
56 Pages
-
Shoulder Mills
96 Pages
-
Face Mills
138 Pages
-
Solid End Milling
118 Pages
-
Taps
194 Pages
-
Hole Finishing
214 Pages
-
Indexable Drills
108 Pages
-
Combination Tools
28 Pages
-
Modular Drills
62 Pages
-
Solid Carbide Drills
112 Pages