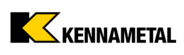

Catalog excerpts
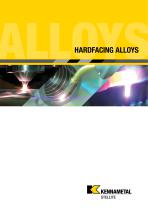
ALLOYS HARDFACING ALLOYS
Open the catalog to page 1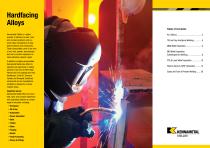
Kennametal Stellite is a global provider of solutions to wear, heat, and corrosion problems and is a world-class manufacturer of alloy-based materials and components. These consumables come in the form of rod, wire, powder, and electrode and can be custom engineered to meet individual customer needs. In addition to welding consumables, Kennametal Stellite also offers its expertise and experience in coating services in the form of HVOF (High-Velocity Oxy Fuel) coatings and weld hardfacings. In the UK, Germany, Canada, and Shanghai, hardfaced components can be manufactured complete to drawing...
Open the catalog to page 2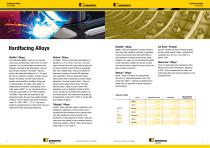
Hardfacing Alloys At a Glance Hardfacing Alloys At a Glance Hardfacing Alloys Nistelle Alloys Stellite Alloys Deloro Alloys The cobalt-based Stellite™ alloys are our most wellknown and successful alloys, with the best “all-round” properties. They combine excellent mechanical wear resistance, especially at high temperatures, with very good corrosion resistance. The Stellite™ alloys are mostly cobalt based with additions of Cr, C, W, and/or Mo. They are resistant to cavitation, corrosion, erosion, abrasion, and galling. The lower carbon alloys are generally recommended for cavitation, sliding...
Open the catalog to page 3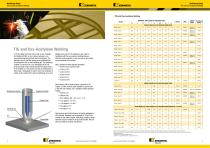
Hardfacing Alloys TIG and Oxy-Acetylene Welding TIG and Oxy-Acetylene Welding ■ TIG and Oxy-Acetylene Welding In TIG (Tungsten Inert Gas), also known as Gas Tungsten Arc Welding (GTAW), an arc is drawn between a nonconsumable tungsten electrode and the workpiece. The electrode, the arc, and the weld-pool are protected from the atmosphere with an inert shielding gas. The hardfacing material is in the form of a rod. Advantages of the TIG process include simple manual operation and good control of the welding arc. The process can also be mechanised, in which case a manipulator is used to move...
Open the catalog to page 4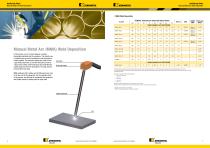
Hardfacing Alloys Manual Metal Arc Weld Deposition KENNAMETAL KENNAMETAL Hardfacing Alloys Manual Metal Arc Weld Deposition Manual Metal Arc (MMA) Weld Deposition In this process, an arc is drawn between a coated consumable electrode and the workpiece. The metallic core is melted by the arc and is transferred to the weld pool as molten droplets. The electrode coating also melts to form a gas shield around the arc and the weld pool as well as a slag on the surface of the weld pool, thus protecting the cooling weld-pool from the atmosphere. The slag must be removed after each layer. MMA...
Open the catalog to page 5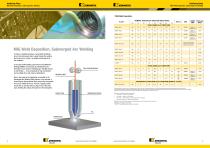
Hardfacing Alloys MIG Weld Deposition, Submerged Arc Welding Hardfacing Alloys MIG Weld Deposition, Submerged Arc Welding Hardfacing Wire MIG Weld Deposition, Submerged Arc Welding In these arc welding processes, consumable hardfacing wire is fed continuously from a spool through the welding torch into the arc, where it is melted and transferred to the workpiece. In the case of MIG welding, also known as Gas Metal Arc Welding (GMAW), the weld pool is protected from the atmosphere by a stream of shielding gas. The MIG process is very flexible — it can be partially or fully mechanised and is...
Open the catalog to page 6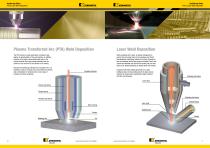
Hardfacing Alloys PTA & Laser Weld Deposition Hardfacing Alloys PTA & Laser Weld Deposition Plasma Transferred Arc (PTA) Weld Deposition Laser Weld Deposition The PTA process is easily automated, providing a high degree of reproducibility of the weld overlays. In addition, because of the highly concentrated heat source, this process benefits from high powder utilization and can achieve a very low level of iron dilution in the overlay. When overlaying with a laser, an optical arrangement is used to focus the laser beam on the workpiece and heat it. Simultaneously, hardfacing material in the...
Open the catalog to page 7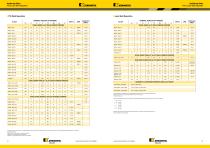
Hardfacing Alloys PTA & Laser Weld Deposition Hardfacing Alloys PTA & Laser Weld Deposition PTA Weld Deposition ALLOY Laser Weld Deposition NOMINAL ANALYSIS OF POWDER1 W COBALT-BASED TRIBALOY™ ALLOYS (GAS-ATOMIZED POWDERS) Tribaloy™ alloy T-400 NICKEL-BASED SUPERALLOYS (GAS-ATOMIZED POWDERS) Nistelle™ alloy “Super C” IRON-BASED HARDFACING ALLOYS (GAS-ATOMIZED POWDERS) Depends on 27 — 2.9 — — Bal. <1.0 0.5%Mn — treatment heat CARBIDES IN A CORROSION-RESISTANT HARD ALLOY MATRIX Super Stelcar™ alloy 9365 Super Stelcar™ alloy 50 plus WC in a Deloro™ 50 alloy matrix Super Stelcar™ alloy 60 plus...
Open the catalog to page 8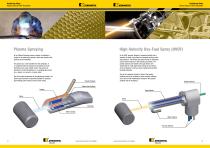
Hardfacing Alloys Plasma Spray & HVOF Deposition Hardfacing Alloys Plasma Spray & HVOF Deposition Plasma Spraying High-Velocity Oxy-Fuel Spray (HVOF) In the Plasma Spraying process, powder is softened or melted in the plasma gas stream, which also transfers the particles to the workpiece. In the HVOF process, powder is introduced axially into a chamber in which a gas flame is constantly burning under high pressure. The exhaust gas exits through an expansion nozzle which produces a high-velocity gas stream. The powder particles are heated in this gas stream and transferred by it with high...
Open the catalog to page 9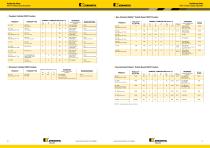
KENNAMETAL KENNAMETAL Hardfacing Alloys HVOF & Plasma Spray Deposition ■ Tungsten Carbide HVOF Powders ■ Gas-Atomized Stellite™ Cobalt-Based HVOF Powders ■ Chromium Carbide HVOF Powders ■ Gas-Atomized Tribaloy™ Cobalt-Based HVOF Powders *ULTIMET™ is a registered trademark of Haynes International. KKkennametal STELLITE www.kennametal.com/stellite www.kennametal.com/stellite KK KENNAMETAL STELLITE
Open the catalog to page 10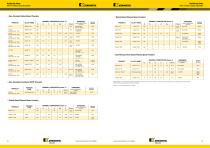
Hardfacing Alloys HVOF & Plasma Spray Deposition KENNAMETAL KENNAMETAL Hardfacing Alloys HVOF & Plasma Spray Deposition ■ Gas-Atomized Nickel-Based Powders ■ Nickel-Based Plasma Spray Powders PRODUCT ■ Cobalt Based Plasma Spray Powders PRODUCT KKkennametal STELLITE
Open the catalog to page 11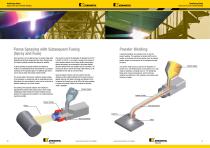
Hardfacing Alloys Spray and Fuse & Powder Welding Hardfacing Alloys Spray and Fuse & Powder Welding Flame Spraying with Subsequent Fusing (Spray and Fuse) Spray and fuse is a two-stage process, the powder alloy being deposited first by flame spraying and then fused. During fusing, the deposit is partially remelted and allowed to resolidify. In flame-spraying, the powder particles are softened or melted in an oxyacetylene flame and transferred to a prepared workpiece by the expanding gases. An additional gas stream can be used to assist with powder particle transfer. The second stage of the...
Open the catalog to page 12All Kennametal catalogs and technical brochures
-
CB11 Stack-On
2 Pages
-
Grinder Tips
16 Pages
-
Grader Blades
40 Pages
-
Road Rehabilitation • Road King
24 Pages
-
Underground Mining
182 Pages
-
ROCTEC ecoline
1 Pages
-
Conforma Clad X2™
2 Pages
-
INNOVATIONS 2020
84 Pages
-
INNOVATIONS 2019
156 Pages
-
Tooling Systems News 2018
60 Pages
-
Oilfield Radial Bearings
2 Pages
-
Cladding Formulas Oilfield
2 Pages
-
General Conveyance Equipment
4 Pages
-
Twin-Screw
2 Pages
-
EDM Blocks Brochure
8 Pages
-
KMT_Wear Solutions_Brochure
12 Pages
-
Alloys Brochure Direct
28 Pages
-
Composite Rods
1 Pages
-
Fluidized Bed Boiler Tubes
1 Pages
-
Mill Roll Brochure
8 Pages
-
Snowplow Blades
1 Pages
-
KenCast Wear Protection
20 Pages
-
7690VA09
3 Pages
-
Tool Selection
3 Pages
-
Indexable Milling Index
8 Pages
-
Milling geometries quick
9 Pages
-
Milling grades
4 Pages
-
Specialty Carbide Catalog
16 Pages
-
Tooling Systems 2013 Catalog Sections
1576 Pages
-
INNOVATIONS CATALOGUE 2015
260 Pages
-
Kennametal Innovations 2014
630 Pages
-
KMT KBH20 metric
18 Pages
-
Master Catalog 2013 Complete - metric
2122 Pages
-
Railroad Brochure
24 Pages
-
Abrasive Blast Nozzles Catalog
60 Pages
-
Surface Mining Catalog
42 Pages
-
Holemaking Taps (metric)
118 Pages
-
Threading
108 Pages
-
O.D. / I.D. Toolholders
162 Pages
-
PCD / PCBN Inserts
66 Pages
-
ISO / ANSI Inserts
132 Pages
-
Thread Mills
20 Pages
-
Copy Mills
118 Pages
-
Slotting Cutters
56 Pages
-
Shoulder Mills
96 Pages
-
Face Mills
138 Pages
-
Solid End Milling
118 Pages
-
Taps
194 Pages
-
Hole Finishing
214 Pages
-
Indexable Drills
108 Pages
-
Combination Tools
28 Pages
-
Modular Drills
62 Pages
-
Solid Carbide Drills
112 Pages