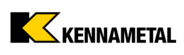

Catalog excerpts
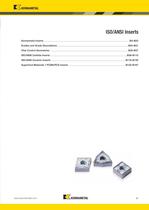
KM_Master12_Turning_B000_B001_Minch.qxp:Layout 1 3/2/12 2:50 PM Page B3 ISO/ANSI Inserts Kennametal Inserts . . . . . . . . . . . . . . . . . . . . . . . . . . . . . . . . . . . . . . . . . . . . . . . . . . . . . . . . . . . . . . . . .B2–B23 Grades and Grade Descriptions . . . . . . . . . . . . . . . . . . . . . . . . . . . . . . . . . . . . . . . . . . . . . . . . . . . . . .B24–B31 Chip Control Geometries . . . . . . . . . . . . . . . . . . . . . . . . . . . . . . . . . . . . . . . . . . . . . . . . . . . . . . . . . . .B32–B37 ISO/ANSI Carbide Inserts . . . . . . . . . . . . . . . . ....
Open the catalog to page 2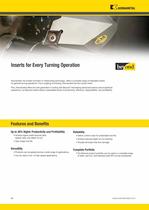
Inserts for Every Turning Operation fBPond Kennametal, the trusted innovator in metalcutting technology, offers a complete range of indexable inserts for general turning operations. From roughing to finishing, Kennametal has the correct insert. Plus, Kennametal offers the next generation in tooling with Beyond™ Harnessing advanced science and exceptional experience, our Beyond inserts deliver unparalleled levels of productivity, efficiency, dependability, and profitability. Up to 30% Higher Productivity and Profitability • Achieve higher metal removal rates (speed, feed, and depth of cut)....
Open the catalog to page 3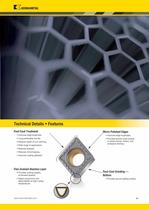
Technical Details • Features Post-Coat Treatment • Improves edge toughness. • Long predictable tool life. • Reduces depth-of-cut notching. • Wide range of applications. • Reduces stresses. • Reduces microchipping. • Improves coating adhesion. Fine-Grained Alumina Layer • Provides coating integrity dependability at high cutting Micro-Polished Edges • Improves edge toughness. • Provides smooth outer surface to reduce forces, friction, and workpiece sticking. ... Post-Coat Grinding — • Provides secure seating surface.
Open the catalog to page 4
Kennametal Inserts Catalog Numbering System How Do Catalog Numbers Work? Each character in our catalog number signifies a specific trait of that product. Use the following key columns and corresponding images to easily identify which attributes apply. Insert Shape Insert Clearance Tolerances apply prior to edge prep and coating corner angles requiring descriptions. the Insert Inscribed circle
Open the catalog to page 5
Kennametal Inserts Catalog Numbering System By referencing this easy-to-use guide, you can identify the correct product to meet your needs. Cutting Edge Fine Finishing Finishing Negative Medium Negative Roughing Negative Universal Medium Finishing Positive Medium Positive Roughing Positive Roughing Medium Roughing Heavy Finishing Wiper Medium Wiper Finishing Sharp Medium Sharp Roughing Wiper High Positive Universal Positive Chip Control Ultra-Fine Finishing Light Finishing Medium Finishing Hone Only Negative Land Negative Land Plus Hone Medium Positive Medium Positive
Open the catalog to page 6
Kennametal Inserts Grade Naming System A system of grades, geometries, and application guidelines to provide optimal solutions for your metalcutting needs. It's easy to determine which Kennametal chip-control cutting tool will work best in your specific workpiece materials and applications! Brand Insert Workpiece Material Workpiece Material Cast Iron Non-Ferrous Materials High-Temp Alloys Hardened Materials Blank = Carbide, uncoated fine finishing heaviest roughing NOTE: Application range does not apply to PCBN grades. Grade • Kenna Perfect" Material Group Wear Application Stainless Steel...
Open the catalog to page 7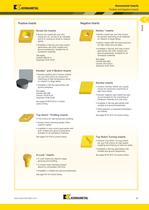
Kennametal Inserts Positive and Negative Inserts Positive Inserts Negative Inserts Screw-On Inserts • Screw-On inserts are your first choice for I.D. turning of all materials and O.D. turning on small to medium • Available in flat-top and chip-control geometries with both molded and ground peripheries. Suitable for all workpiece materials. Kendex" and V-Bottom Inserts • Kendex positive and V-bottom inserts are your first choice for productive machining of high-temperature alloys on medium to large lathes. • Available in flat-top geometries with ground periphery. product listing. Top Notch "...
Open the catalog to page 8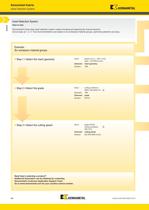
Kennametal Inserts Insert Selection System Insert Selection System Kennametal's three-step insert selection system makes choosing and applying the most productive tool as easy as 1,2,3. Tool recommendations are based on six workpiece material groups, optimizing selection accuracy. Six workpiece material groups i Step 1 • Select the insert geometry Given: dePths of cut = 040" (1 mm) Unknown: insert geometry Step 2 • Select the grade Given: cutting conditions: Unknown: grade ■ Step 3 • Select the cutting speed Given: srade KCP25 cutting conditions Unknown: cutting speed Need help in selecting...
Open the catalog to page 9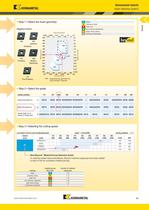
Kennametal Inserts Insert Selection System ■ Step 1 • Select the insert geometry Negative Inserts Fine Finishing feed rate (mm/rev) feed rate (in/rev) high-strength materials Stainless Steel Cast Iron Non-Ferrous Materials High-Temp Alloys Hardened Materials ■ Step 2 • Select the grade cutting condition casting, or forging skin Step 3 • Selecting the cutting speed Low-Carbon (<0,3% C) and Free-Machining Steel speed — m/min (SFM) starting conditions <£> New Beyond Material Group Selection Guide: To optimize speed recommendations, Beyond material subgroups have been added to each of the six...
Open the catalog to page 10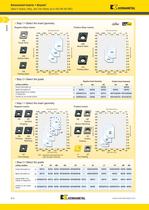
Kennametal Inserts • Beyond ™ Steel • Carbon, Alloy, and Tool Steels up to 450 HB (48 HRC) Step 1 • Select the insert geometry Negative Wiper Inserts Positive Wiper Inserts feed rate (mm/rev) Rough Wiper Medium Wiper Finishing Wiper ■ Step 2 • Select the grade cutting condition feed rate (in/rev) Medium Wiper Finishing Wiper feed rate (mm/rev) feed rate (in/rev) Negative Insert Geometry Positive Insert Geometry ■ Step 1 • Select the insert geometry Negative Inserts feed rate (mm/rev) Finishing Medium feed rate (in/rev) Fine Finishing high-strength materials i Step 2 • Select the grade...
Open the catalog to page 11
Kennametal Inserts • Beyond ™ Steel • Carbon, Alloy, and Tool Steels up to 450 HB (48 HRC) ■ Step 3 • Select the cutting speed Low-Carbon (<0.3% C) and Free-Machining Steel speed — m/min (SFM) starting conditions <X> Medium- and High-Carbon Steels (>0.3% C) speed — m/min (SFM) starting conditions <D> Alloy Steels and Tool Steels (£330 HB) (£35 HRC) speed — m/min (SFM) starting conditions <X> Alloy Steels and Tool Steels (340-450 HB) (36-48 HRC) speed — m/min (SFM) starting conditions <D> Ferritic, Martensitic, and PH Stainless Steels (£330 HB) (£35 HRC) speed — m/min (SFM) starting...
Open the catalog to page 12All Kennametal catalogs and technical brochures
-
CB11 Stack-On
2 Pages
-
Grinder Tips
16 Pages
-
Grader Blades
40 Pages
-
Road Rehabilitation • Road King
24 Pages
-
Underground Mining
182 Pages
-
ROCTEC ecoline
1 Pages
-
Conforma Clad X2™
2 Pages
-
INNOVATIONS 2020
84 Pages
-
INNOVATIONS 2019
156 Pages
-
Tooling Systems News 2018
60 Pages
-
Oilfield Radial Bearings
2 Pages
-
Cladding Formulas Oilfield
2 Pages
-
General Conveyance Equipment
4 Pages
-
Twin-Screw
2 Pages
-
EDM Blocks Brochure
8 Pages
-
KMT_Wear Solutions_Brochure
12 Pages
-
Alloys Brochure Direct
28 Pages
-
Kennametal Stellite Alloys
15 Pages
-
Composite Rods
1 Pages
-
Fluidized Bed Boiler Tubes
1 Pages
-
Mill Roll Brochure
8 Pages
-
Snowplow Blades
1 Pages
-
KenCast Wear Protection
20 Pages
-
7690VA09
3 Pages
-
Tool Selection
3 Pages
-
Indexable Milling Index
8 Pages
-
Milling geometries quick
9 Pages
-
Milling grades
4 Pages
-
Specialty Carbide Catalog
16 Pages
-
Tooling Systems 2013 Catalog Sections
1576 Pages
-
INNOVATIONS CATALOGUE 2015
260 Pages
-
Kennametal Innovations 2014
630 Pages
-
KMT KBH20 metric
18 Pages
-
Master Catalog 2013 Complete - metric
2122 Pages
-
Railroad Brochure
24 Pages
-
Abrasive Blast Nozzles Catalog
60 Pages
-
Surface Mining Catalog
42 Pages
-
Holemaking Taps (metric)
118 Pages
-
Threading
108 Pages
-
O.D. / I.D. Toolholders
162 Pages
-
PCD / PCBN Inserts
66 Pages
-
Thread Mills
20 Pages
-
Copy Mills
118 Pages
-
Slotting Cutters
56 Pages
-
Shoulder Mills
96 Pages
-
Face Mills
138 Pages
-
Solid End Milling
118 Pages
-
Taps
194 Pages
-
Hole Finishing
214 Pages
-
Indexable Drills
108 Pages
-
Combination Tools
28 Pages
-
Modular Drills
62 Pages
-
Solid Carbide Drills
112 Pages