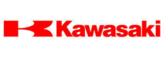

Catalog excerpts
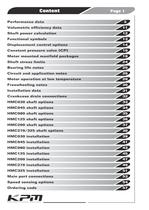
Performance data 3 Volumetric efficiency data 11Shaft power calculation 12 Functional symbols 13 Displacement control options 14 Constant pressure valve (CP) 16 Motor mounted manifold packages 19 Shaft stress limits 24 Bearing life notes 25 Circuit and application notes 26 Motor operation at low temperature 29 Freewheeling notes 30 Installation data 31 Crankcase drain connections 32 HMC030 shaft options 33 HMC045 shaft options 34 HMC080 shaft options 35 HMC125 shaft options 36 HMC200 shaft options 37HMC270/325 shaft options 38HMC030 installation 39 HMC045 installation 41 HMC080 installation...
Open the catalog to page 2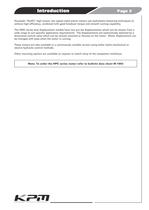
Kawasaki StaffaӔ high torque, low speed radial piston motors use hydrostatic balancing techniques to achieve high efficiency, combined with good breakout torque and smooth running capability.The HMC series dual displacement models have two pre-set displacements which can be chosen from a wide range to suit specific application requirements. The displacements are hydraulically selected by a directional control valve which can be remote mounted or directly on the motor. Motor displacement can be changed with ease when the motor is running.These motors are also available in a continuously...
Open the catalog to page 3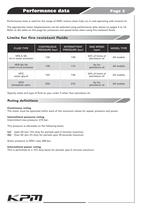
Performance data is valid for the range of HMC motors when fully run-in and operating with mineral oil. The appropriate motor displacements can be selected using performance data shown on pages 4 to 10. Refer to the table on this page for pressures and speed limits when using fire-resistant fluids. > FLUID TYPECONTINUOUS PRESSURE (bar)INTERMITTENTPRESSURE (bar)MAX SPEED(rpm)MODEL TYPE HFA 5/95 oil-in-water emulsion13013850% of limits of petroleum oilAll modelsHFB 60/40 water-in-oil emulsion138172As for petroleum oilAll modelsHFC water glycol10313850% of limits of petroleum oilAll modelsHFD...
Open the catalog to page 4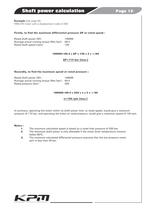
Example (see page 9) : HMC270 motor with a displacement code of 280: Firstly, to find the maximum differential pressure P at rated speed : Rated shaft power (W): 189000Average actual running torque (Nm/bar): 69.4 Rated shaft speed (rpm): 150 189000=69.4 x P x 150 x 2 x /60P=174 bar (max.)Secondly, to find the maximum speed at rated pressure : Rated shaft power (W) : 189000Average actual running torque (Nm/bar) : 69.4 Rated pressure (bar) : 250 189000=69.4 x 250 x n x 2 x /60n=104 rpm (max.) In summary, operating the motor within its shaft power limit, at rated speed, would give a maximum...
Open the catalog to page 13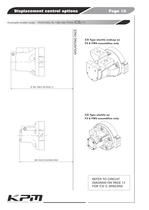
Example model code - HMC200/S/180/60/FM4/ > /71 CS Type shuttle endcap onF4 & FM4 assemblies only CS Type shuttle onF3 & FM3 assemblies only > MOUNTING FACE 'B' SEE TABLE ON PAGE 14 SEE VALVE HOUSING PAGE
Open the catalog to page 16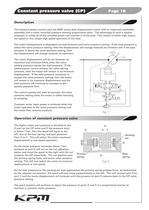
The constant power control uses the HMC series dual displacement motor with an improved crankshaft assembly and a motor mounted pressure sensing proportional valve. The advantage of such a system attempts to utilise all of the installed power and transfer it to the load. This results in either high torque low speed or low torque high speed operation of the load. The motor displacement is dependent on load pressure and valve pressure setting. If the load pressure is below the valve pressure setting, then the displacement will change towards its minimum and if the load pressure is above the...
Open the catalog to page 17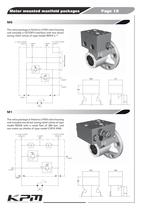
1" SAE FLANGE CODE 61 1ܼ" SAE FLANGE CODE 61 T " BSPP ܼ" BSPP P GA GB B B 1" BSPP > 1" SAE FLANGE CODE 61 1ܼ" SAE FLANGE CODE 61 " BSPP A MU B GB " BSPP GA " BSPP >
Open the catalog to page 20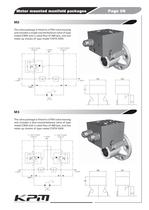
1" SAE FLANGE CODE 61 1ܼ" SAE FLANGE CODE 61 " BSPP A MU B GB GA > " BSPP " BSPP PORT 1 > 1ܼ" SAE FLANGE CODE 61 1" SAE FLANGE CODE 61 ܾ" BSPP A MU B GB GA > " BSPP ܼ" BSPP PORT 1 >
Open the catalog to page 21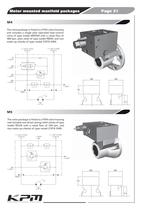
1" SAE FLANGE CODE 61 1ܼ" SAE FLANGE CODE 61 A B GB PI " BSPP ܼ" BSPP GA " BSPP > MU ܾ" BSPP " BSPP PORT 1 DR > 1ܽ" SAE FLANGE CODE 62 1" SAE FLANGE CODE 62 ݾ" BSPP A MU B GB " BSPP GA ܼ" BSPP >
Open the catalog to page 22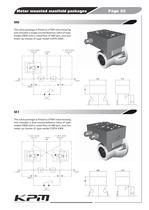
1" SAE FLANGE CODE 62 1ݽ" SAE FLANGE CODE 62 " BSPP A MU B GB GA > " BSPP " BSPP PORT 1 > 1ܼ" SAE FLANGE CODE 62 1" SAE FLANGE CODE 62 ܾ" BSPP A MU B GB GA > " BSPP ܼ" BSPP PORT 1 >
Open the catalog to page 23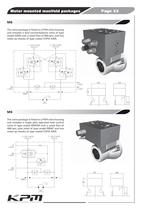
1" SAE FLANGE CODE 62 1ݽ" SAE FLANGE CODE 62 A B PORT 1GA MU > 275279172 " BSP P GB " BSP " BSPP P > 1ܽ" SAE FLANGE CODE 62 1" SAE FLANGE CODE 62 A BPI ݼ" BSPP " BSPP MU ܾ" BSPP >
Open the catalog to page 24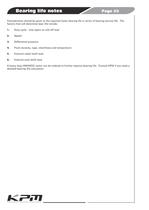
1. 2. Duty cycle - time spent on and off load Speed Consideration should be given to the required motor bearing life in terms of bearing service life. The factors that will determine bear life include: 3. Differential pressure 4. Fluid viscosity, type, cleanliness and temperature 5. External radial shaft load 6. External axial shaft loadA heavy duty HM(HD)C motor can be ordered to further improve bearing life. Consult KPM if you need a detailed bearing life calculation. >
Open the catalog to page 26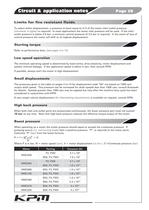
To select either displacement, a pressure at least equal to 2/3 of the motor inlet/outlet pressure (whichever is higher) is required. In most applications the motor inlet pressure will be used. If the inlet/outlet pressure is below 3.5 bar, a minimum control pressure of 3.5 bar is required. In the event of loss of control pressure the motor will shift to its highest displacement. > Refer to performance data, (see pages 4 to 10). > The minimum operating speed is determined by load inertia, drive elasticity, motor displacement and system internal leakage. If the application speed is below 3...
Open the catalog to page 27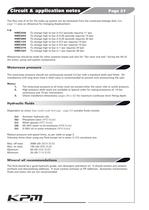
The flow rate of oil for the make-up system can be estimated from the crankcase leakage data (see page 11) plus an allowance for changing displacement: e.g. HMC030 To change high to low in 0.2 seconds requires 11 lpm HMC045 To change high to low in 0.25 seconds requires 15 lpm HMC080 To change high to low in 0.25 seconds requires 32 lpm HMC125 To change high to low in 0.5 sec requires 15 lpm HMC200 To change high to low in 0.5 sec requires 15 lpm HMC270 To change high to low in 1 sec requires 24 lpm HMC325 To change high to low in 1 sec requires 20 lpmAllowances should be made for other...
Open the catalog to page 28All Kawasaki Precision Machinery catalogs and technical brochures
-
HPB Series
76 Pages
-
M3X/M3B
35 Pages
-
HMC Series
43 Pages
-
K3V/K5V/K7V
8 Pages
-
HMB Series
92 Pages
-
PV series
2 Pages
-
M7V / M7X Series
64 Pages
-
HPC Series
37 Pages
-
KPM-PV
2 Pages
-
KDRDE KWE series
2 Pages
-
KTEM/ KTMS series
2 Pages
-
K3VL Series
72 Pages
-
HMF Series
72 Pages
-
KMP series
2 Pages
-
ERU series
2 Pages
-
K7VG
32 Pages
-
K8V
36 Pages
-
K3VLS
36 Pages
-
KLSV 18
24 Pages
-
KPES
2 Pages
-
HPC400
4 Pages
-
hydraulic industriel vehicle
20 Pages
-
B - Brake Valve
24 Pages
-
M-Motor
35 Pages
-
CBD - Counterbalance Valve
6 Pages
-
M2X/M5X - Slewing motor
19 Pages
-
Axial Piston Pump Series K3VG
34 Pages
-
K3VG Series
34 Pages
-
HMC-capability-brochure
6 Pages
-
High-Power-HPC-Series-Datasheet
44 Pages
Archived catalogs
-
HMB
70 Pages
-
HMC CATALOGUE
60 Pages
-
Rotary Actuator HR Series
8 Pages
-
B-motor-catalog-
70 Pages
-
Datasheet - K3VL B Series
53 Pages
-
THE K3VLB-SERIES
6 Pages
-
High Power HPC Series
40 Pages
-
Axial piston hydraulic motors
35 Pages