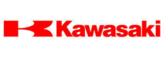

Catalog excerpts
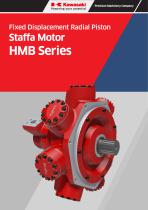
Precision Machinery Company Fixed Displacement Radial Piston Staffa Motor
Open the catalog to page 1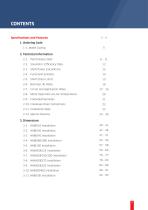
CONTENTS Specifications and Features 1. Ordering Code 1-1. odel Coding M 2-2. Volumetric Efficiency Data 2-3. Shaft Power Calculations 2-5. Shaft Stress Limits 2-6. Bearing Life Notes 2-7. Circuit and Application Notes 2-8. Motor Operation at Low Temperatures 2-10. Crankcase Drain Connections
Open the catalog to page 2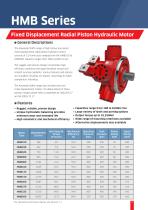
HMB Series Fixed Displacement Radial Piston Hydraulic Motor General Descriptions The Kawasaki Staffa range of high torque low speed fixed displacement radial piston hydraulic motors consists of 13 frame sizes ranging from the HMB010 to HMB500. Capacity ranges from 188 to 8,000 cc/rev. The rugged, well proven design incorporates high efficiency combined with good breakout torque and smooth running capability. Various features and options are available including, on request, mountings to match competitors’ interfaces. The Kawasaki Staffa range also includes dual and triple displacement...
Open the catalog to page 3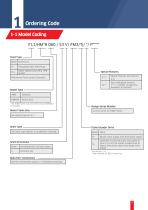
Ordering Code 1-1 Model Coding F11/HM*B 060 / S3 V/ FM3/Tj/ */ P***** Fluid Type Blank Phosphate ester (HFD fluid) Water based fluids (HFA, HFB & HFC) Special features (see Section 2-1) Alternative fluids contact Kawasaki Non-catalogued features, (*****) = number assigned by Kawasaki as required Heavy duty * For B400 frame size, only Heavy Duty (HMHDB ) is available. Motor Frame Size Design Series Number Current series for HMB motors Shaft Type See shaft type options in installation drawings Tacho Encoder Drive Horizontal and vertically down Shaft Orientation Square wave output with...
Open the catalog to page 4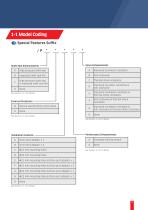
1-1 Model Coding Special Features Suffix Shaft Seal Enhancements Valve Enhancements High pressure shaft seal Improved cavitation resistance Improved shaft seal life High pressure shaft seal & improved shaft seal life Thermal shock resistance Improved caviation resistance & anti-clockwise Improved cavitation resistance & thermal shock resistance External Protection Anti-clockwise & thermal shock resistance Improved cavitation resistance & anti-clockwise & thermal shock resistance Marine-specification primer paint Installation Features Performance Enhancements Drain port adaptor x 1 Increased...
Open the catalog to page 5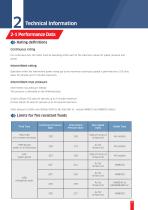
Technical Information 2-1 Performance Data Rating definitions Continuous rating For continuous duty the motor must be operating within each of the maximum values for speed, pressure and power. Intermittent rating Operation within the intermittent power rating (up to the maximum continuous speed) is permitted on a 15% duty basis, for periods up to 5 minutes maximum. Intermittent max pressure Intermittent max pressure: 300bar. This pressure is allowable on the following basis: a) Up to 50rpm 15% duty for periods up to 5 minutes maximum. b) Over 50rpm 2% duty for periods up to 30 seconds...
Open the catalog to page 6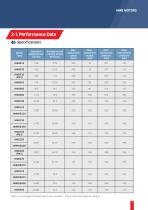
2-1 Performance Data Specifications Motor Type Geometric displacement (cc/rev) Average actual running torque (Nm/bar) Other non standard displacements are possible - check with Kawasaki for details. 7
Open the catalog to page 7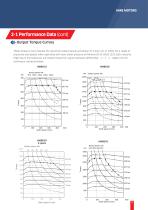
2-1 Performance Data (cont) Output Torque Curves These torque curves indicate the maximum output torque and power of a fully run-in motor for a range of pressures and speeds when operating with zero outlet pressure on Mineral Oil of 50cSt (232 SUS) viscosity. High return line pressures will reduce torque for a given pressure differential. - x - x - x - Upper limit of continuous rating envelope. HMB010 200 300 Shaft speed (r/min) 200 300 Shaft speed (r/min) Shaft speed (r/min) 200 300 Shaft speed (r/min)
Open the catalog to page 8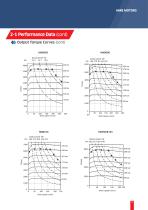
2-1 Performance Data (cont) Output Torque Curves (cont) HMB060 100 150 200 Shaft speed (r/min) Shaft speed (r/min) Shaft speed (r/min) Shaft speed (r/min)
Open the catalog to page 9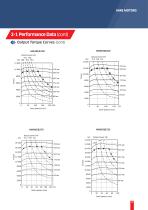
2-1 Performance Data (cont) Output Torque Curves (cont) HM(HD)B200 Shaft speed (r/min) Shaft speed (r/min) Shaft speed (r/min) Shaft speed (r/min)
Open the catalog to page 10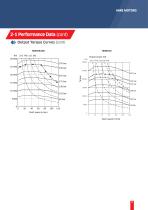
2-1 Performance Data (cont) Output Torque Curves (cont) HMHDB400 Shaft speed (r/min) Shaft speed (r/min)
Open the catalog to page 11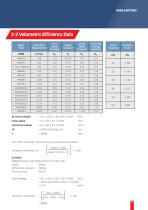
2-2 Volumetric Efficiency Data Motor Type Geometric Displacement Zero Speed Constant Speed Constant Creep Speed Constant Crankcase Leakage Constant Fluid Viscosity Viscosity Factor Creep speed Crankcase leakage The motor volumetric efficiency can be calculated as follows: Volumetric efficiency (%) (speed x disp.) = (speed x disp.) + Qt Example: HMB200 motor with displacement of 3.087 l/rev. Speed 60rpm Differential pressure Fluid viscosity Total leakage Volumetric efficiency l/min l/min
Open the catalog to page 12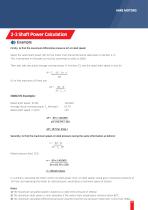
2-3 Shaft Power Calculation Example Firstly, to find the maximum differential pressure ΔP at rated speed: Select the rated shaft power (W) for the motor from the performance data table (in Section 2-1). This is presented in kilowatts so must be converted to watts (x1000). Then also take the actual average running torque in N m/bar (To) and the rated shaft speed in rpm (n). W = To . ΔP . 2π . n 60 Or to find maximum ΔP then use: HMB270 Example: Rated shaft power, W (W): Average actual running torque, To (Nm/bar): Rated shaft speed, n (rpm): ΔP = 60 x 140,000 2π x 63.79 x 125 ΔP= 167 bar...
Open the catalog to page 13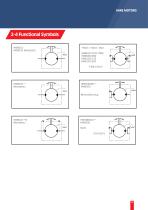
2-4 Functional Symbols HMB010HMB030 (Monobloc) Dual ports
Open the catalog to page 14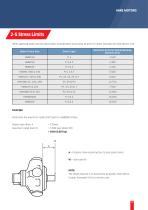
2-5 Stress Limits When applying large external radial loads, consideration should also be given to motor bearing lives (see Section 2-6). Motor Frame Size Shaft Types Maximum External Radial Bending Moment [Nm] Example: Determine the maximum radial shaft load of a HMB080 motor: Radial load offset, A Maximum radial load, W W A A = Distance from mounting face to load centre (mm) W = Side load (N) NOTE: The offset distance A is assumed to be greater than 50mm. Contact Kawasaki if this is not the case.
Open the catalog to page 15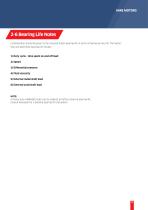
2-6 Bearing Life Notes Consideration should be given to the required motor bearing life in terms of baring service life. The factors that will determine bearing life include: 1) Duty cycle - time spent on and off load 2) Speed 3) Differential pressure 4) Fluid viscosity 5) External radial shaft load 6) External axial shaft load NOTE: A heavy duty HM(HD)B motor can be ordered to further improve bearing life. Consult Kawasaki for a detailed bearing life calculation.
Open the catalog to page 16All Kawasaki Precision Machinery catalogs and technical brochures
-
HPB Series
76 Pages
-
M3X/M3B
35 Pages
-
HPC Series
37 Pages
-
HMC Series
43 Pages
-
K3V/K5V/K7V
8 Pages
-
K3VL Series
76 Pages
-
PV series
2 Pages
-
ERU series
2 Pages
-
HMF Series
72 Pages
-
M7V / M7X Series
64 Pages
-
HPC Series
37 Pages
-
KPM-PV
2 Pages
-
KDRDE KWE series
2 Pages
-
KTEM/ KTMS series
2 Pages
-
K3VL Series
72 Pages
-
HMF Series
72 Pages
-
KMP series
2 Pages
-
ERU series
2 Pages
-
K7VG
32 Pages
-
K8V
36 Pages
-
K3VLS
36 Pages
-
KLSV 18
24 Pages
-
KPES
2 Pages
-
HPC400
4 Pages
-
hydraulic industriel vehicle
20 Pages
-
B - Brake Valve
24 Pages
-
M-Motor
35 Pages
-
CBD - Counterbalance Valve
6 Pages
-
M2X/M5X - Slewing motor
19 Pages
-
Axial Piston Pump Series K3VG
34 Pages
-
K3VG Series
34 Pages
-
HMC-capability-brochure
6 Pages
-
High-Power-HPC-Series-Datasheet
44 Pages
Archived catalogs
-
HMB
70 Pages
-
HMC CATALOGUE
60 Pages
-
Rotary Actuator HR Series
8 Pages
-
B-motor-catalog-
70 Pages
-
Datasheet - K3VL B Series
53 Pages
-
THE K3VLB-SERIES
6 Pages
-
High Power HPC Series
40 Pages
-
Axial piston hydraulic motors
35 Pages