

Catalog excerpts
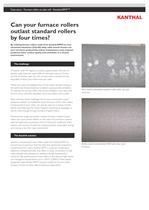
Case story Furnace rollers at tube mill Օ Kanthal APMT Can your furnace rollers outlast standard rollers by four times? By utilizing furnace rollers made from Kanthal APMT, an iron-chromium-aluminum (FeCrAl) alloy, roller hearth furnace ow-ners can boost productivity, reduce maintenance costs, improve produced tubes' surface quality and contribute to a cleaner environment. The challenge A Swedish tube mill regularly produces approximately 200 tons of stainless steel tubes per week. With an estimated value of 10 euro per kilo of stainless steel, the mill's furnace rollers manufacture the equivalent of about two million euro per week. Within two years of installation, four of the rollers started cracking at the welds and showed extensive oxidation, causing surface problems. To overhaul the furnace rollers, the owners needed to shut down the furnace, which cost their operation up to two million euro a week. Many mills face similar challenges: the furnace environment causes excessive oxidation on traditional nickel-chromium (NiCr) alloy rollers. Consequently, furnace rollers can only be used six to twelve months before reconditioning. This means frequent maintenance stoppages as well as costly storage of large numbers of spare rollers. Moreover, the rough and uneven surfaces formed on these furnace rollers can cause surface defects on the tubes. This produces a poorer yield and adds extra production costs. Furthermore, traditional rollers require a fair amount of water for cooling purposes, using higher energy and creating a less than clean environment. NiCr (nickel-chromium) standard rollers after one year of service. The Sandvik solution Sandvik is introducing furnace rollers made from Kanthal APMT an iron-chromium-aluminum (FeCrAl) alloy, that significantly outperform conventional NiCr rollers. Kanthal APMT is a powder metallurgical dispersion strengthened alloy that offers a unique combination of high creep strength and resistance to oxidation at high temperatures -critical for high-performance furnace rollers. It also features high mecha٭nical strength at temperatures up to I250°C (2280°F). These unique properties make Kanthal APMT uniquely suitable for furnace rollers among a number of other high-temperature applications. Rollers made from Kanthal APMT after four years of service.
Open the catalog to page 1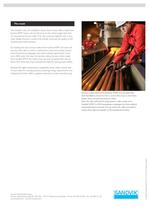
The result The Swedish tube mill installation shows that furnace rollers made from Kanthal APMT have a service life of up to four times longer than that of conventional furnace rollers. The new material, together with a new roller design, ensures a surface that actually improves the quality of the manufactured tube products. By installing the new furnace rollers from Kanthal APMT the tube mill has also been able to reduce maintenance costs and increase produc-tivity Maintenance stoppages have been reduced significantly In fact, since 2004 when the tube mill started utilizing furnace rollers...
Open the catalog to page 2All Kanthal catalogs and technical brochures
-
HIGH POWER HEATING ELEMENTS
8 Pages
-
KANTHAL® AM100
3 Pages
-
Thermocouple wire and strip
32 Pages
-
Resistance heating strip
100 Pages
-
double layer capacitors
40 Pages
-
Axial-leaded resistors
4 Pages
-
Furnace tubes
36 Pages
-
Diffusion cassettes
44 Pages
-
Air heating cassettes
8 Pages
-
heating elements
147 Pages