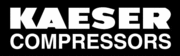
Catalog excerpts
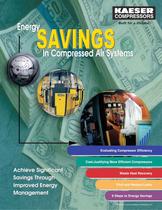
Provided as a service by Kaeser Compressors, Inc. Evaluating Compressor Efficiency Cost-Justifying More Efficient Compressors Waste Heat Recovery Find and Reduce Leaks 6 Steps to Energy Savings Achieve Significant Savings Through Improved Energy Management In Compressed Air Systems Energy
Open the catalog to page 1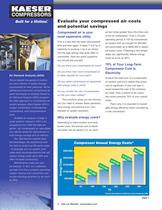
2 Visit our Website: www.kaeser.com Chart 1 Evaluate your compressed air costs and potential savings Compressed air is your most expensive utility This is a fact that has been documented time and time again. It takes 7 to 8 hp of electricity to produce 1 hp in an airtool. Yet this high energy cost quite often is overlooked. Here are some questions you should ask yourself: Do you know your compressed air costs? Do you know how much compressed air is really required for your plant? Do you select compressed air equipment with energy costs in mind? Do you monitor the use of compressed air like...
Open the catalog to page 2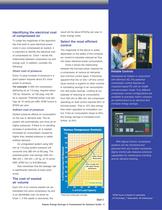
Kaeser Energy Savings in Compressed Air Systems Guide 3 Chart 2 *8760 hours is based on operating 24 hours/day, 7 days/week, 52 weeks/year. Identifying the electrical cost of compressed air To judge the magnitude of the opportunities that exist to save electrical power costs in your compressed air system, it is important to identify the electrical cost of compressed air. Chart 1 shows the relationship between compressor hp and energy cost. In addition, consider the following: Direct cost of pressure Every 10 psig increase of pressure in a plant system requires about 5% more power to...
Open the catalog to page 3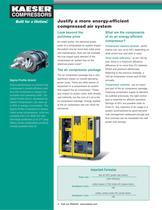
4 Visit our Website: www.kaeser.com Important Formulas (hp) (0.7457) (power rate) (hours) motor efficiency (volts) (amps) (1.732) (motor eff.) (power factor) 746 (volts) ( amps) (motor eff.) (power factor) 746 Power cost = Horsepower (3 ph) = Horsepower (1 ph) = Justify a more energy-efficient compressed air system Sigma Profile Airend Airend performance is critical to the compressor’s overall efficiency and thus the compressor’s energy consumption and operating costs. The Sigma Profile airend, developed by Kaeser Compressors, can save up to 20% in energy consumption. The Sigma Profile is...
Open the catalog to page 4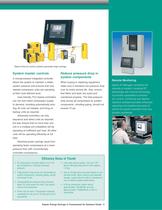
Kaeser Energy Savings in Compressed Air Systems Guide 5 State-of-the-art control systems generate large savings. Remote Monitoring Sigma Air Manager combines the benefits of modern industrial PC technology with Internet technology to provide unparalleled compressor control, monitoring and reports. Optional software provides enhanced reporting and enables end users to control air system operation from any location worldwide. System master controls A microprocessor-integrated controller allows the system to maintain a stable system pressure and ensures that only needed compressor units are...
Open the catalog to page 5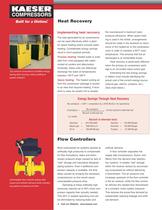
6 Visit our Website: www.kaeser.com Energy Savings Through Heat Recovery Btu savings/yr. = 0.95* x compressor hp x 2545 Btu/hp x hrs operation/yr. $ savings/yr. = x $ fuel cost/unit of alternate fuel *air cooled Btu/unit of alternate fuels: Electricity = 3413 Btu/kWh Gasoline = 125,000 Btu/gal Natural gas = 1000 Btu/cu ft Kerosene = 135,000 Btu/gal #2 oil = 138,500 Btu/gal Propane = 91,500 Btu/gal Btu savings/yr. Btu/unit of alternate fuel Flow Controllers Heat Recovery Implementing heat recovery The heat generated by air compressors can be used effectively within a plant for space heating...
Open the catalog to page 6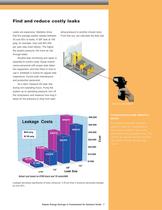
Kaeser Energy Savings in Compressed Air Systems Guide 7 Find and reduce costly leaks Leaks are expensive. Statistics show that the average system wastes between 25 and 35% to leaks. A 3/8” leak at 100 psig, for example, may cost $31,200 per year (see chart below). The higher the system pressure, the more air lost through leaks. Routine leak monitoring and repair is essential to control costs. Equip maintenance personnel with proper leak detection equipment, and train them in how to use it. Establish a routine for regular leak inspections. Involve both maintenance and production personnel....
Open the catalog to page 7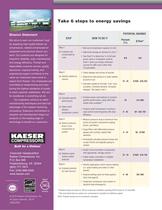
Corporate Headquarters: Kaeser Compressors, Inc. P.O. Box 946 Fredericksburg, VA 22404 (800) 777-7873 Fax: (540) 898-5520 www.kaeser.com © 2010 Kaeser Compressors, Inc. All rights reserved. 05/10 USGUIDE4 Mission Statement We strive to earn our customers’ trust by supplying high quality Kaeser air compressors, related compressed air equipment and premium blower systems. Our products are designed for long-term reliability, easy maintenance, and energy efficiency. Prompt and dependable customer service, quality assurance, ongoing training, and engineering support contribute to the value our...
Open the catalog to page 8All Kaeser Compressors catalogs and technical brochures
-
Compressed Air Filters
8 Pages
-
Automatic Magnetic Drain
2 Pages
-
Air Treatment Solutions
12 Pages
-
Activated Carbon Tower
2 Pages
-
SmartPipe+TM
28 Pages
-
S Series
8 Pages
-
SX - HSD Series
20 Pages
-
ASD, BSD, and CSD Series
12 Pages
-
KRYOSEC SERIES
4 Pages
-
Portable Compressors
8 Pages
-
Screw Compressor
20 Pages
-
Air Treatment Brochure
12 Pages
-
USGLANCE
6 Pages
-
Mobilair ? M350
2 Pages
-
CLEAN AIR
12 Pages
-
Mobilair M250
2 Pages
-
MobilairM27
2 Pages
-
SigmaControl2
6 Pages
-
Mobilair M122
2 Pages
-
Mobilair M100
2 Pages
-
Mobilair M64
2 Pages
-
Mobilair M57 Utility
2 Pages
-
Mobilair M57
2 Pages
-
Mobilair M50
2 Pages
-
Mobilair M15/M17
2 Pages
-
Mobilair Brochure
6 Pages
-
Hybritec Combination Dryer
8 Pages
Archived catalogs
-
Rotary Screw Vacuum Packages
4 Pages
-
Mobilair Tools
4 Pages
-
Mobilair M270
2 Pages
-
Mobilair M200
2 Pages
-
Mobilair M26
2 Pages
-
Booster Compressors
6 Pages
-
Airbox and Airbox Center
4 Pages
-
Water-cooled Aftercoolers
2 Pages
-
Air Cooled Aftercoolers
4 Pages
-
Air Main Charging System
4 Pages
-
Condensate Filters
4 Pages
-
Eco-Drain Traps
2 Pages
-
Automatic Magnetic Drain
2 Pages
-
High Temperature Afterfilter
2 Pages
-
Oil Mist Eliminator
2 Pages
-
Compressed Air Filters
8 Pages
-
Activated Carbon Tower
2 Pages
-
Membrane Dryers
2 Pages
-
Breathing Air Systems
4 Pages
-
Desiccant Air Dryers
12 Pages
-
Clean Air Treatment Brochure
4 Pages
-
SmartPipe Modular Piping Catalog
72 Pages
-
SmartPipe Modular Piping
72 Pages
-
HSD Series Compressors
8 Pages
-
ESD and FSD Compressors
6 Pages
-
DSD Series Compressors
6 Pages
-
CSD Series Compressors
6 Pages
-
BSD Series Compressors
6 Pages
-
ASD Series Compressors
6 Pages
-
AS Series Compressors
6 Pages
-
SK Series Compressors
6 Pages
-
SM Series Compressors
6 Pages
-
SX Series Compressors
6 Pages
-
AirCenter
4 Pages