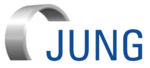
Catalog excerpts
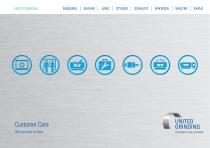
UNITED GRINDING: MAGERLE BLOHM JUNG STUDER SCHAUDT MIKROSA WALTER EWAG Customer Care We are here to help.
Open the catalog to page 1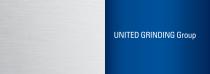
UNITED GRINDING Group
Open the catalog to page 2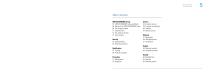
UNITED GRINDING CUSTOMER CARE Table of Contents UNITED GRINDING Group 07 UNITED GRINDING Group worldwide 08 Brands of the United Grinding Group 09 Our company brands 14 Customer Care 14 Our range of services 15 Service index Start Up 19 Commissioning 20 Warranty extension Qualification 25 Training 26 Production support Prevention 31 Maintenance 32 Inspection
Open the catalog to page 3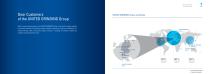
UNITED GRINDING Customer Care Dear Customers of the UNITED GRINDING Group UNITED GRINDING Group worldwide With its eight company brands, the UNITED GRINDING Group is the world's leading supplier of precision machines for grinding, eroding, lasering, measuring as well as combination machining. We also offer an extensive range of services – including our efficient, reliable and customer-oriented Customer Care. UNITED GRINDING Russia UNITED GRINDING North America BLOHM and JUNG UNITED GRINDING China SCHAUDT and MIKROSA WALTER UNITED GRINDING India EWAG MÄGERLE STUDER UNITED GRINDING Group Own...
Open the catalog to page 4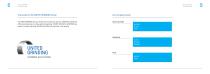
UNITED GRiNDiNG CUSTOMER CARE UNiTED GRiNDiNG CUSTOMER CARE The brands of the UNITED GRINDING Group Our company brands The UNITED GRINDING Group is divided into three business divisions. MAGERLE, BLOHM and JUNG are professionals in surface and profile grinding. STUDER, SCHAUDT und MIKROSA are experts in cylindrical grinding. WALTER and EWAG are specialists in tool grinding. Surface & profile MAGERLE BLOHM JUNG Cylindrical STUDER SCHAUDT MIKROSA UNITED m GRINDING KORBER SOLUTIONS Tools WALTER EWAG
Open the catalog to page 5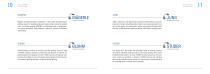
UNITED GRiNDiNG CUSTOMER CARE UNiTED GRiNDiNG CUSTOMER CARE MAGERLE .. -m MAGERLE KORBER SOLUTIONS Magerle AG Maschinenfabrik, established in 1929, builds high-performance grinding systems for handling simple and complex surface and profile grinding tasks. As a turnkey supplier, MAGERLE is a technology leader in superproduc-tive special applications. Great emphasis is placed on customer individuality and flexibility. JUNG JUNG is synonymous with high quality and superior surface finishing in precision machines for surface and profile grinding. Solutions are primarily provided for...
Open the catalog to page 6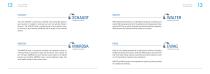
UNITED GRINDING Customer Care UNITED GRINDING Customer Care The name SCHAUDT is synonymous worldwide with cutting-edge technological solutions for cylindrical, noncircular and cam form grinding "Made in Germany". The SCHAUDT brand is a global partner for the automotive industry, focusing on high customer individuality and the supply of fully automatic systems. Walter Maschinenbau GmbH is a world leading manufacturer of grinding, eroding and CNC measuring machines for the production and resharpening of metal, wood and PCD tools as well as rotationally-symmetrical production components....
Open the catalog to page 7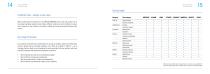
UNITED GRiNDiNG CUSTOMER CARE UNiTED GRiNDiNG CUSTOMER CARE Service index* Customer Care - always in your area With a market share of around 25 %, the United GRiNDiNG group is the clear number one in the relevant grinding machine market. Many different conditions must be fulfilled, to ensure that it remains so: one of these is an efficient, reliable and customer-oriented Customer Care service. Our range of services Our machines must fulfill your requirements for as long as possible, operate cost-effectively, function reliably and be constantly available. From "Start up" through to...
Open the catalog to page 8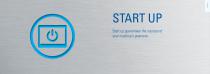
start up Start up guarantees the success of your machine's premiere.
Open the catalog to page 9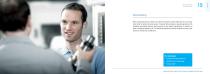
Commissioning When commissioning your machine we check all functions in great detail and carry out integration tests for options and accessories, if required. We provide your operating personnel with individual and detailed training, taking account of your specific requirements. If desired, we grind a workpiece defined by you. The experience gained from several hundred start-ups a year ensures a smooth start to production. Your advantages • Smooth start to production • Optimal basic knowledge • Trained staff mägerle | blohm | jung | studer | schaudt | mikrosa | walter | ewag UNITED GRINDING...
Open the catalog to page 10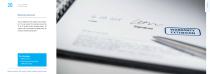
UNITED GRINDING Customer Care Warranty extension You can depend on the quality of your machine. You can extend the warranty period by 12 or 24 months under favorable terms. All repairs and the necessary original parts are covered, excluding wear parts. Your advantages • Ability to plan • Financial security at low additional costs mägerle | blohm | jung | studer | schaudt | mikrosa | walter | ewag
Open the catalog to page 11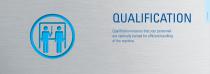
QUALIFICATION Qualification ensures that your personnel are optimally trained for efficient handling of the machine.
Open the catalog to page 12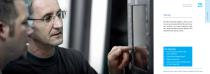
UNITED GRINDING CUSTOMER CARE We offer individually designed , which we can carry out at your production facility and on your own machine. Our course categories range from general grinding through operation and programming to special courses. Your advantages • Learning of processes under real conditions • Trained and motivated staff • Higher productivity • Lower risk of machine failure due to incorrect operation MAGERLE | BLOHM | JUNG | STUDER | SCHAUDT | MIKROSA | WALTER | EWAG
Open the catalog to page 13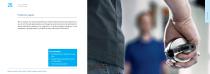
UNITED GRINDING Customer Care Production support We can support your technical employees and machine operators during the production process on site. We will gladly advise you with regard to process and cycle time optimization or special operational procedures (e.g. integration of in-process gauging, changeover to new workpieces or grinding wheels). You define the focus and duration of the service. Your advantages • Increase in your company's knowhow • Support of your production team by our specialists • Increased productivity mägerle | blohm | jung | studer | schaudt | mikrosa | walter |
Open the catalog to page 14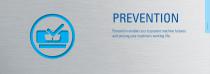
Prevention enables you to prevent machine failures and prolong your machine's working life.
Open the catalog to page 15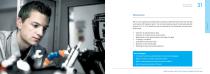
UNITED GRINDING Customer Care We carry out maintenance systematically according to a detailed checklist with more than 200 work steps and 50 inspection points. You can choose between regular maintenance (possible intervals: 4, 6, 12, 18, 24 months) and one-off maintenance. All maintenance activities essentially include: • • • • • • • Inspection of exposed machine parts Inspection of the electrical and control system Replacement of wear parts (included in the scope of supply) Oil change, if necessary Comprehensive functional check Backup of current machine data M aintenance report with...
Open the catalog to page 16All K. JUNG GmbH catalogs and technical brochures
-
j600
16 Pages
Archived catalogs
-
JE600/JE800
9 Pages
-
J600
9 Pages