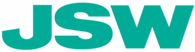
Catalog excerpts
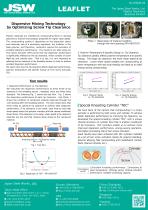
LEAFLET Dispersive Mixing Technology by Optimizing Screw Tip Clearance 1. Dispersion Performance vs. Tip Clearance We evaluated the dispersion performance at three levels of tip clearance in the kneading section ; standard, twice and three times standard. The following Fig. 1 shows the test flow. Fig. 2 shows the dispersion performance at each tip clearance. And Photo 1 shows the condition of compound material observed through the vent opening after the kneading section. The test results show that there exists an optimum tip clearance to achieve ideal dispersion performance. If tip clearance is too small, local heat-up and high shear speed reduce the polymer viscosity and that causes insufficient shear stress. If tip clearance is too large, shear speed at tip clearance becomes too low and that reduces shear stress to the compound material. PP TiO2 Kneading section---Tip learance varied Poor melt Photo 1 Observation of material condition through the vent opening (PP+60%TiO2) 2. Polymer Temperature & Specific Energy vs. Tip Clearance Tip clearance greatly affects polymer temperature and specific energy. The larger tip clearance, the lower shear speed at tip clearance. Lower shear speed enables the compounding at lower temperature with less local heating and leads to an ideal energy-saving compounding. Larger Tip Clearance Smaller Tip Clearance Larger Tip Clearance Smaller Tip Clearance 280 Specific Energy kWh/kg Test results Polymer Temp.℃ Plastics materials are modified by compounding fillers or alloying polymers to improve end products properties for higher value added. The compounding quality is depending on the dispersion status and molecular size of a secondary ingredient, the modifier, in the base polymer, and therefore, customers require the extruders of excellent dispersion performance. The results of our tests using our Twin Screw Extruder (TEX) prove that the dispersion performance is significantly affected by the tip clearance, which consists of screw flight tip, and cylinder bore. That is to say, it is very important to optimize the tip clearance in the kneading section in order to achieve excellent dispersion performance. We report here how the tip clearance affects dispersion performance, polymer temperature and specific energy of Twin Screw Extruder, TEX. The Japan Steel Works, Ltd. Plastics Machinery Business Division Fig.3 Polymer Temp. vs. Tip Clearance Fig. 4 Specific Energy vs. Tip Clearance Special Kneading Cylinder “NIC” We have been of the opinion that compounding in a screw extruder is performed by both screw and cylinder. To achieve better dispersion performance by improving tip clearance, we developed the special kneading cylinder “NIC” with a unique channel structure on cylinder bore that is another constituent of tip clearance. NIC cylinders enable us to achieve more improved dispersion performance, energy-saving operation, and higher processing rate of twin screw extruders. Good results have been achieved with NIC cylinders installed on a lot of twin screw extruders mainly for polymer blending, polymer alloying, filler compounding and masterbatch (carbon black, titanium dioxide, etc.). Japan Steel Works, Ltd. Tokyo Head Office Gate City Osaki West Tower 1-11-1, Osaki, Shinagawa-ku, Tokyo 141-0032, Japan 1)Excellent kneading performance 2)Kneading at lower temperature 3)Energy saving 4)Good coloration performance 5)Higher processing capacity Europe (Germany) China (Shanghai)
Open the catalog to page 1All JSW The Japan Steel Works catalogs and technical brochures
-
Delta Crown
1 Pages
-
Compact UWC unit "SDC"
1 Pages
-
Technical Center in Europe
1 Pages
-
TEX Controller EXANET5000
1 Pages
-
Mixing Screw Element "BMS"
1 Pages
-
Stock Cutter blade for UWC
1 Pages
-
TWIST KEADING DISC "TKD"
1 Pages
-
DE-GASSING CYLINDER “DGC”
1 Pages
-
JSW Hiroshima Guide
8 Pages
-
JSW corporate
14 Pages