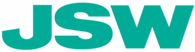
Catalog excerpts
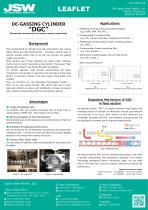
LEAFLET DE-GASSING CYLINDER The Japan Steel Works, Ltd. Plastics Machinery Business Division 1. Pelletizing & Compounding of powdered plastics (e.g. HDPE, POM, PPE, PPS...) 3. Pelletizing & Compounding of water-containing plastics (e.g. ABS...) Remarkable improvement of powder material productivity Filler compounding on extruder have been demanded to get various added values and high performances . Therefore, particle sizes of polymer powder and/or filler to be fed into extruder are getting smaller and smaller. When particle size of feed materials are rather small, materials involve much air and it has quite low bulk density. This causes “Feed 2. Compounding of powdered filler (e.g. Talc, calcium carbonate, magnesium hydroxide...) 4. Compounding of water-containing filler (e.g. wood powder...) 5. Recycling of crushed plastics with low bulk density (e.g. film, carpet...) contained in wood powder is vaporized in the extruder and then bulk density is extremely reduced. That also causes “Feed bottle neck problem”. Here, we introduce our new developed “De-Gassing Cylinder --- Screw speed(rpm) feed-neck problem as above and significantly increase processing rate in plastics compounding with low bulk density material. Screw speed(rpm) DGC” on our twin screw extruder TEX, which helps you to solve Fig.2 PP+50% of No-drying wood powder Degassing Mechanism of DGC in feed section For another example, wood powder compounding, the water bottole neck problem” and limited Extruder throughput. Large processing rate For example, DGC can increase processing rate by three times in compounding of HDPE with mean particle size of 70μm. ■ Strong kneading at low temperature Strong kneading at low temperature can be achieved due to improved material feeding. De-gassing cylinder “DGC” is installed between feed hopper and kneading section of extruder to effectively exhaust gas/moisture out naturally or by force. Bulk density of feed materials are remarkably increased with DGC, and therefore, processing rate can be significantly increased due to improved feeding ability. ■ Excellent de-gassing performance Gas out of polymer can be effectively exhausted by the special filter installed on DGC. It is easy to recover the filter from powder clogging because it has reverse flow cleaning structure. ■ Various filter mesh sizes You can select the optimum filter size depending on the particle size of plastics. Fig.1 Material Flow We believe that the DGC will be a standard technology of the times in powder compounding. Test equipment is available in our Plastics Technology Developing Center in Hiroshima, Japan. You can make trial on TEX with DGC using your plastics materials to evaluate the performance. Japan Steel Works, Ltd. Tokyo Head Office Gate City Osaki West Tower 1-11-1, Osaki, Shinagawa-ku, Tokyo 141-0032, Japan Europe (Germany) Utility model right Patent Patents concerned in Japan No.2585280 Screw type extruder No.2960885 Screw type extruder China (Shanghai)
Open the catalog to page 1All JSW The Japan Steel Works catalogs and technical brochures
-
Delta Crown
1 Pages
-
Compact UWC unit "SDC"
1 Pages
-
Technical Center in Europe
1 Pages
-
TEX Controller EXANET5000
1 Pages
-
Mixing Screw Element "BMS"
1 Pages
-
Stock Cutter blade for UWC
1 Pages
-
TWIST KEADING DISC "TKD"
1 Pages
-
JSW Hiroshima Guide
8 Pages
-
JSW corporate
14 Pages