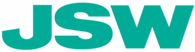
Catalog excerpts
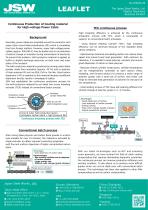
LEAFLET Continuous Production of Coating material for High-voltage Power Cable The Japan Steel Works, Ltd. Plastics Machinery Business Division TEX continuous process High kneading efficiency is achieved by the continuous production process with TEX, which is comparable or superior to conventional batch processes. Background Generally, power cables are insulated around the conductor with super-clean cross-linked polyethylene (PE) which is completely free from foreign matters. However, super high-voltage power cables (approx. 500,000 V) may be broken due to concentration of electric charge on insulator during transmission of electricity. To prevent this problem, half-conductive material is applied as buffer to slightly discharge electricity on both inner and outer sides of the insulator. The half-conductive material is produced by mixing carbon black powder made from acetylene (approx. 40 %) and co-polymer of high-pressure PE such as EEA, EVA or the like. Good carbon dispersion in PE is essential to this material because insufficient dispersion directly results in breakage of cables. JSW has established the continuous production process for the half-conductive material by our latest twin screw kneading extruder (TEX) instead of conventional batch process. ・ Using Special Keading Cylinder “NIC”, high kneading efficiency can be achieved because of the repeated shear stress variations. ・ Optimized tip clearance at kneading section can reduce shear speed and prevent local heat generation. With optimum tip clearance, it is possible to keep polymer viscosity and ensure good dispersion of carbon in base polymer. ・ Because of block cylinder construction, cylinder temperature can be independently controlled at each section (feed, kneading, and forward section) to produce a wider range of polymer grades with a same set of screws. And chiller unit helps to eliminate heat generation of polymer for extrusion at low temperature. ・ Intermeshing screws of TEX have self-cleaning efficiency for smooth change of polymer grade in 2~3 minutes. Protection metal (Lead or Aluminum) Advantages ・ Good dispersion of carbon. ・ Less dispersal of carbon powder ・ Energy saving ・ Easy color change (grade change) ・ Simple production process Wire to cut-off electromagnetic wave Conductor (Copper core wire) Inner & outer half-conductive layers (Acetylene carbon black + high pressure PE) Carbon black Continuous kneading process with TEX Polymer Side feeder Conventional batch process After mixing base polymer and carbon black powder in a batch type kneader for over 10 minutes, the material is extruded by single extruder to obtain required conducting properties with fine and uniform dispersion of highly concentrated carbon black. Polymer Carbon black Batch type kneader Too long mixing time → over 10 min. Advantages ・ Good dispersion of carbon black Disadvantages ・ Bad working condition due to dispersal of carbon powder ・ Large energy loss ・ Difficult color change (grade change) Single screw extruder Pellets Japan Steel Works, Ltd. Tokyo Head Office Gate City Osaki West Tower 1-11-1, Osaki, Shinagawa-ku, Tokyo 141-0032, Japan With our latest technologies such as NIC and kneading screw geometry, we have entered the field of cable coating compounding that requires demanding dispersion properties. Our continuous process can improve production efficiency and working condition. It also allows us to produce more difficult grades which can not be dealt even with conventional batch process. This technology has been also applied to other filler compounding as well as carbon compounding. Europe (Germany) China (Shanghai)
Open the catalog to page 1All JSW The Japan Steel Works catalogs and technical brochures
-
Delta Crown
1 Pages
-
Compact UWC unit "SDC"
1 Pages
-
Technical Center in Europe
1 Pages
-
TEX Controller EXANET5000
1 Pages
-
Mixing Screw Element "BMS"
1 Pages
-
Stock Cutter blade for UWC
1 Pages
-
TWIST KEADING DISC "TKD"
1 Pages
-
DE-GASSING CYLINDER “DGC”
1 Pages
-
JSW Hiroshima Guide
8 Pages
-
JSW corporate
14 Pages