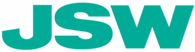
Catalog excerpts
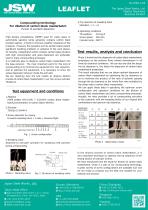
LEAFLET Compounding technology For dilution of carbon black masterbatch Pursuit of excellent dispersion High density polyethylene (HDPE) used for water pipes or automobile gasoline tanks generally contains carbon black powders approx. 2.5wt% to improve weather resistance of the products. However, fine powders such as carbon black present significant handling problems or pollution of the work places. So recently, masterbatch which contains carbon black powders with high concentration and good dispersion are preferably used in many compounding processes. It is relatively easy to disperse carbon black masterbatch into the base polymer. The most important point for this kind of compounding is to minimize the equipment for cost reduction. And to optimize the equipment, it is necessary to know the actual dispersion behavior inside the extruder. We are reporting here the test results to observe dilution process of carbon black masterbatch in our twin screw extruder TEX65α II. The Japan Steel Works, Ltd. Plastics Machinery Business Division 5.Tip clearance of kneading disks Standard, × 3, × 6 6.Operating conditions Throughput 210 kg/h Screw speed 250 rpm Cylinder temp. 200° C Test results, analysis and conclusion 1.Material HDPE pellets (MI=0.04) + 6.25wt% carbon black masterbatch(concentration of carbon black:40wt%) Photo 2 shows that the dispersion of carbon black masterbatch progresses as the polymer flows toward downstream in all three tip clearance conditions. We can also see that the larger the tip clearance is, the faster the dispersion of carbon black masterbatch progresses. This result indicates that we can obtain optimal dispersion of carbon black masterbatch by optimizing the tip clearance so as to maximize the product of the ratio of polymer passing through the tip clearance to the whole flow rate multiplied by the shear rate to carbon black masterbatch. We can apply these data in specifying the optimum screw configuration and operation conditions for the dilution of carbon black masterbatch and other compounding processes. Actually, we have provided a lot of compounding extruders to the customer with the kneading blocks of our original disk combinations and optimum tip clearance. SAMPLING POSITION Test equipment and conditions 3.Screw elements for mixing Forward kneading block × 5 sets + Reverse flight NO NO NO SAMPLE SAMPLE SAMPLE SAMPLING POSITION 4.Sampling valve Attached to extruder cylinders for sampling melt polymer during compounding PACKING SAMPLING VALVE SENSOR HOLE Photo 1 Sampling valve Fig. 2 Structure of sampling valve Japan Steel Works, Ltd. Tokyo Head Office Gate City Osaki West Tower 1-11-1, Osaki, Shinagawa-ku, Tokyo 141-0032, Japan NO NO NO SAMPLE SAMPLE SAMPLE NO NO NO SAMPLE SAMPLE SAMPLE In the dilution process of carbon black masterbatch, it is very important technique to optimize the tip clearance of the mixing section of extruder screws. We have introduced here the study for dilution of carbon black masterbatch, which is a part of our compounding technology. A great variety of screw configurations are available now and we are ready to propose you the best one suitable for your material and process. Europe (Germany) Observation result China (Shanghai)
Open the catalog to page 1All JSW The Japan Steel Works catalogs and technical brochures
-
Delta Crown
1 Pages
-
Compact UWC unit "SDC"
1 Pages
-
Technical Center in Europe
1 Pages
-
TEX Controller EXANET5000
1 Pages
-
Mixing Screw Element "BMS"
1 Pages
-
Stock Cutter blade for UWC
1 Pages
-
TWIST KEADING DISC "TKD"
1 Pages
-
DE-GASSING CYLINDER “DGC”
1 Pages
-
JSW Hiroshima Guide
8 Pages
-
JSW corporate
14 Pages