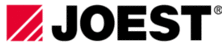
Catalog excerpts
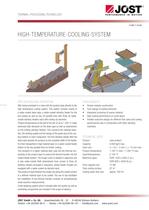
Thermal Processing technology PERFORMANCE in mo t i on JT.008.11.05.EN High-Temperature-Cooling-System Application and Operation: Your Benefit: After being annealed in a rotary kiln the product gets directly to the high temperature cooling system. This system consists mainly of a water-cooled down pipe, a water-cooled vibratory feeder for the pre-cooling as well as two (2) parallel lines with three (3) watercooled vibratory feeders each with cooling rip elements. Product temperatures at the exit of the kiln of up to 1.350 °C make extremely high demands on the down pipe as well as downstream on the cooling vibratory feeders. This concerns the material selection, the working quality and the design of the guide way of the cooling medium in each component. The first vibratory feeder after the down pipe spreads the product on the complete width of the feeder. It is then transported in high material layer on a water-cooled feeder bottom to the two parallel lines for further cooling. The transport in a higher material layer uses the low thermal conductivity of the product layer to reduce the thermal transfer into the cooled feeder bottom. The trough-cover is divided in segments and is also water-cooled. Both downstream lines consist of three (3) vibratory feeders arranged in sequence, whose feeder troughs are equipped with a water-cooled rip element each. The product is lead between the single rips along the cooled surface in a defined material layer to be cooled. The use of rips facilitates the installation of big thermal transfer surfaces at simultaneously small machine measurements. A belt weighing system which is located after the system as well as controlling components are included in the scope of delivery. • • • • • Simple modular construction Fast change of cooling elements Integrated screening of coarse material High cooling performance on small space Flexible maschine design for different flow rates and cooling performances also in combination with other vibrating machines Technical Data: Product: Capacity: Grain size: Product temperature: Austrittstemperatur: Maschine types: Drive capacity inst.: Total cooling surface: Cooling water flow rate: coke product 6.000 kg/h max. d = 0,2 – 5 mm / L = 10 mm max. 1.100 °C nom. / 1.350 °C max. £ 100 °C FUFK 1200 x 5250 (1 pc.) FUFK 800 x 4500 (6 pc.) 27 kW 87 m2 approx. 350 t/h JÖST GmbH + Co. KG · Gewerbestraße 28 - 32 · D-48249 Dülmen-Buldern Telefon +49 (0)2590 98-0 · Telefax +49 (0)2590 98-101 · info@joest.com · www.joest.com
Open the catalog to page 1All JÖST catalogs and technical brochures
-
BIGGEST VIBRATION AIR
10 Pages
-
recycling
6 Pages
-
Mining, Minerals, Quarrying
6 Pages
-
Foundry Industry
8 Pages
-
Lost Foam Process
1 Pages
-
ZUFS sand attrition unit
1 Pages
-
FDL Dosing feeder
2 Pages
-
charging machine
1 Pages
-
Air separation Table
2 Pages
-
Belt weighting scale
1 Pages
-
Spiral elevator cooler
1 Pages
-
FSMG Casting cooler
1 Pages
-
Granulate dryer
1 Pages
-
FSM Bridge conveyor
1 Pages
-
JT.006.10.04
1 Pages
-
JT.007.12.02
1 Pages
-
JT.004.10.04
1 Pages
-
JT.002.10.05
1 Pages
-
JT.003.01.01
1 Pages
Archived catalogs
-
casting cooler
4 Pages